Practical Sailor finds the Alado Nautica headsail furler to be easy to install and a worthwhile sail-handling tool. One feature that sets the Alado apart from other jib or genoa furlers is its staggered slotting of five-foot foil sections that slide together and interlock over a conventional wire or rod headstay. This design allows the do-it-yourselfer to fit each foil section over an attached headstay, and simply push the formed furler up the wire or rod. Mainstream headsail furlers tend to be assembled on the ground and installed with the mast horizontal. The Alado furlers design uses integral halyards to place a compression load on the foil, eliminating the need for Loctite, set screws, and a top swivel. We tested the Alado over five months of coastal cruising and daysailing.
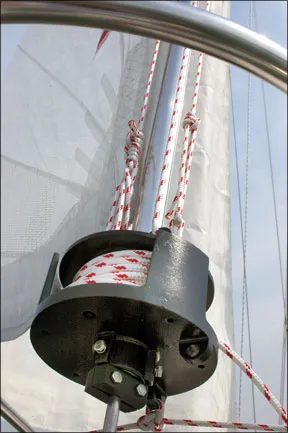
Photos by Ralph Naranjo
****
Its been a few years since Practical Sailor took a look at jib/genoa furlers. The results of a reader survey evaluating 15 different headsail furlers were published in the Feb. 1, 2004 issue. In that article, Practical Sailor editors determined that overall, readers were satisfied with their furlers installation method, performance, and maintenance as
long as they were sized and installed correctly. (More recently, we tested furlers for light-air sails in the March 2008 issue.)
Among the furlers reviewed in the 2004 article was one made by Brazil-based Alado Nautica, which has been making headsail furlers since 1990.
At the heart of the Alado furling system is a sensible self-installation foil design with a built-in halyard arrangement thats similar to what Cruising Design Inc. (CDI) pioneered some years ago. But what sets Alado apart is its staggered slotting of five-foot foil sections that slide together and interlock over a conventional wire or rod headstay.
This design allows the do-it-yourselfer to fit each foil section over an attached headstay, and simply push the formed furler up the wire or rod. Once the furlers top assembly butts against the headstays upper terminal, its time to trim and fit the last two interconnecting sections. This is accomplished by momentarily loosening the headstay and slipping on the roller drum. After reattachment, the drums bushings and end stop are put in place.
When installing a furler designed to go over an existing headstay, it may be a safe bet to go ahead and replace the headstay wire before installation-some new furlers even come with replacement wire-because once the foil goes over the wire, theres no way to monitor the wire condition.
The Alado installation process seemed very user friendly, but to make sure, we did our own test installation aboard a Bill Shaw-designed Pearson 32.
Comes As a Kit
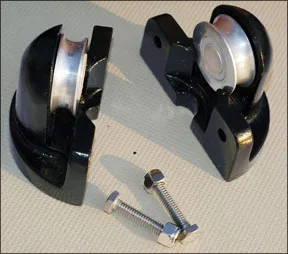
The whole show is shipped in two boxes, and parts are astonishingly few in number, a feature thats trumped only by the even smaller number of tools needed to get the job done.
The top of each half-foil extrusion has a pre-drilled hole, which accepts a plastic bushing that clamps over the headstay. These high molecular-weight plastic bushings allow the foil to rotate freely on the headstay. Two 2.5-foot extrusions are included; the first is used to establish the halfway-up stagger that keeps the seams of the foil halves spaced optimally for maximum torque handling.
Each extrusion is an example of careful fabrication and quality control. Even after going through acid washing and anodizing, the smooth sliding joints allow each segment of the foil extrusion to slide into another with impressive precision.
The installers best friend is an existing halyard used to hold the growing stack of foils in place. All it takes to engage this handy helper is tying a rolling hitch around the lowest extrusions and cleating off the halyard so that the bitter end is on the headstay foil, about seven feet above the deck.
The only drawback editors found with the Alado in the 2004 survey was its owners manual, which they deemed lacking. Our test installers found the manual to be adequate but not exemplary. Alado plans to offer a how-to video on its website in the near future.
Design Differences
Mainstream headsail furlers today (Harken, Profurl, Furlex, etc.) tend to be assembled on the ground and installed with the mast horizontal. They can be hoisted aloft using a crane, or winched into place with a spinnaker halyard and a person at the masthead in a bosun chair ready with tools and a generous dose of expletives.
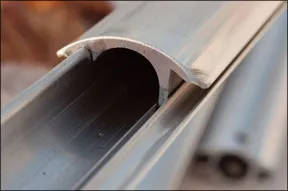
These systems use a genoa halyard from the spar itself to hoist a sliding top swivel thats shackled to the head of the sail. This system puts foil sections in tension and requires a bearing system in both the swivel and the drum. Its a tried and proven approach, and it dominates the market, especially among boats over 40 feet.
The Alado furlers design uses integral halyard(s) to place a compression load on the foil, causing the sliding extrusion segments to stay where they belong and eliminating the need for Loctite, set screws, and a top swivel. Headsail tension is relatively modest on a small cruising boats furling jib, so not being able to use your masthead halyard and winches is an acceptable compromise in this case. The down side is coping with the furling sail halyards (one or two, depending upon user preference), and how to tie them off in a manner that will keep them free from slatting against the sail or keep their tails from snarling up the furling process.
We found taming the halyard spaghetti issue a reasonably easy challenge to mount. We set up two halyards, and although the quarter-inch line initially seemed more string than rope, it has the load handling and low-stretch characteristics to do the job.
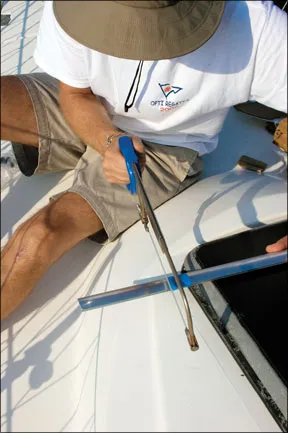
In order to further lessen the excess line issue, we cut the halyard tail off once the sail was hoisted, recognizing that when it was time to douse the sail, we would reattach the tail via a sheet bend.
The second halyard was run with the assumption that “twins” in a wing-and-wing headsail combo could be a useful downwind sail plan. The unused halyard was, like the working halyard, rigged externally and terminated on one of the top fittings of the roller drum. It could be messengered with a lighter piece of line, but already using a quarter-inch line for the halyard, downsizing to a messenger wouldnt be much different. Despite the fact that it led along the luff of the genoa, it seemed to remain reasonably out of the way. Time will tell whether or not flogging is an issue, and this will be something well keep an eye on during our long-term testing.
Furler Function
With an easy pull, the 120-percent genoa we hoisted wound into a tight, evenly rolled bundle about the headstay. The fore and aft slotted foils seemed quite capable of handling the torque loads associated with the furling process.
Energy derived from the line pull was imparted to the foil via the drum at the tack of the sail. The rotary force traveled aloft to the head of the sail via the foil itself, and the entire structure demonstrated that it was able to handle the torque of furling.
Weve so far put the Alado through its paces during five months of coastal cruising and daysailing. A short-handed crew has used it to furl a 120-percent genoa and to reef the sail as much as 90 percent. This testing has shown that the halyard tension of the thin-line system is perfectly adequate, and the units furling ease matches that of much more costly competitors. Whether or not we will be as optimistic about how the furler functions in a 35-knot squall remains to be seen. But we can say that our initial look revealed a well-designed and well-made unit that was a snap to install, literally. Continued testing of the system will evaluate friction, corrosion, and the impact of repeated use.
Please do not purchase an Alado furling system. My system was installed for 3 years and caused the forestay to snap while under way. The fact that the system contains its own halyard system is in no way “better” or more advanced that the other systems that use masthead forestay. Since the system is essentially floating on your forestay, all of the lateral weight caused by furling and winds on the jib are being forced upon the fittings at the top of the mast and right above the turnbuckle on the bow. On conventional furling systems the masthead halyard tightens the luff tape on the jib which helps to take some of the side loading. Stainless steel is strong when tensioned, but can break like a paperclip under constant side loads which is exactly what happened to mine. Luckily everyone on the boat was safe and I was able to recover everything. I will NOT be reinstalling the Alado system.
Where did the headstay part? What size of wire or rod? Was it a new headstay when you installed the Alado system?
Same thing happened with my Harkin furler. The foils are installed basically the same way as Aldo but without the offsetting of the joints. Not sure why you would think the halyard carrying any of the forestay load. The forestay is under 1,250 pounds for 1/4″ your halyard is maybe a 300 pounds. Sorry for the lost Kev but it sounds like a bad install
I disagree with Kev on blaming the lateral loads during furling and on the wind. Besides the furling load which are really not that strong you have much more point loads on your forestay when you use a conventional hank on sail compared to the more evenly distributed loads with the slides of the Alado system. I am using the Alado system for over 20 years now on my 27′ boat and I never had an issue besides a corrosion of the forestay wire which I could not blame the furler system for.
We are the USA Alado Roller Furling Distributor (icwstore.com) and we are very sorry to hear that the forestay failed, but this is very unlikely not due to the Alado Furling System design, weight or halyard design.
The lightweight aluminum 5 -foot foil sections weigh less than 5 lbs. each, and even on a 70-foot forestay the accumulated weight would not be more than about 85 lbs., including the top headers and halyard(s). The forestay must be capable of taking several hundreds or thousands of lbs., of weight when under the force of air pressure.
Depending on the angle of the forestay, the vertical weight effect is reduced by as much as 50% and is shared by the deck fitting which, supported by the deck takes the weight differential including the drum.
To have a catastrophic failure of this kind, is indicate of a metal failure at the mast connection.
We will be at the Annapolis Spring and United States Boat show in 2023 and would be very pleased to show from an engineering perspective how we know the Alado could not have caused the problem.
The Alado Roller Furling Team.