My friend Nick and I are still debating which bolts are tougher to break free: shaft coupling bolts or the lug nuts on an old trailer. Nick argues that lug nuts spend more time underwater and are usually torqued down a whole lot tighter than a shaft coupling screw. On the opposite side, I contend that shaft coupling bolts require you to assume the yoga pose Downward Pretzel just to see the bolts. The argument will no doubt carry on for years, but this week, as I began the slow work of liberating three seized seacocks on the 50-year-old Yankee 30 Opal (formerly Bay Star) our recently acquired project boat, I was reminded that even the most stubborn bolts can often be coaxed loose with a judicious application of penetrating oil, the right tools, patience, and muscle.
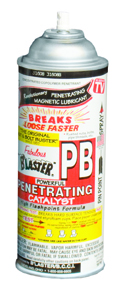
Longtime readers will remember our previous encounter with Dustin Rahl, owner of a very busy mobile trailer service in Sarasota, Fla., Trailers 2 Go. While the most corroded components must often be cut free, many of the seized nuts and bolts he encounters in his work can be liberated. On our first meeting with Rahl, the axle on the trailer for our Catalina 22 test boat Jelly (now replaced by the 1983 Catalina “Lil’ Spitfire”), had cracked at the weld, so that its left wheel splayed outward at a 20-degree angle. Dustin arrived early Tuesday to remove the axle, which was rusted beyond hope, so that he could measure it and order a new one. Alas, the lug nut bolts stood in his way. He didn’t even bother to try them cold. “I’ll just give it a shot of PB Blaster,” he said. And that was that.
Since that first encounter, Rahl has provided faithful service, most recently replacing the leaf springs on the trailer, for a projected long haul up to Practical Sailor‘s new summer office in Marquette, MI near the shores of Lake Superior. He is, as they say in the industry, a stand-up guy.
We’ve tested spray petroleum products to a fare-thee-well. Some are good for loosening bolts, others for sealing electrical connections, and others for protecting against corrosion. When it comes to loosening bolts, we’ve found the PB Blaster works best. That’s not to say the others won’t work. Its just that when it comes to the really tough bolts, PB rises to the top.
But what happens if the PB isn’t enough? Carefully applied heat from a butane, MAPP-gas, or propane torch is usually the next step. After that, its time to break out the specialty tools. As contributing writer, and former boatyard manager Ralph Naranjo explained more than a decade ago—the tools required for nut and bolt extraction can range from the most basic to the esoteric.
“Like a chef with a favorite set of sauce recipes, a good mechanic needs a tried-and-proven list of tricks to help coax rusted fasteners into submission,” writes Naranjo (see “Rust Busters: Spray Solutions for Seized Fasteners and Other Metal Hardware,” PS April 2009). Naranjo’s tools range from penetrants and ingenuity to pure brute force. The following is quoted from that report:
“For sockets, a breaker bar and the learned wisdom of just the right amount of torque works much of the time. An impact screwdriver is often our go-to tool for slotted fasteners. For really stubborn fasteners, there are nut cutters, and a wide range of torque- and shock-inducing gadgets.
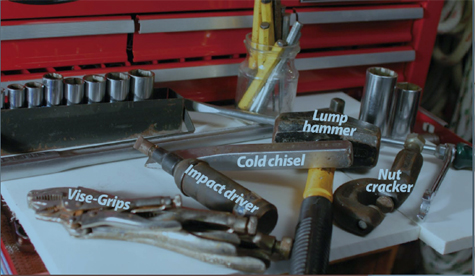
“One unusual but effective fastener-freeing technique involves massive thermal change that causes an abrupt material expansion or contraction. A piece of dry ice is pressed against a stubborn bolt head to shrink its dimensions. This results in the disruption of the rusty bond and more willingness for the bolt to turn.
“Less esoteric solutions include box or socket wrenches with fewer facets, which afford a tighter grip on a nut or bolt head and allow more torque without stripping the hardware. The better your ability to apply force, the more careful you must be to avoid breaking the fastener.
“Sometimes, all a bolt needs is a few good wacks to loosen the bond, but be careful! You don’t want to damage the threads. If you can only approach from the threaded end of a bolt, you can put another nut on the bolt and tap that – not too hard. Alternately, you can use a rubberized mallet, or a piece of hardwood to insulate the bolt from the hammer.
“The rusting process also degrades bolt head shape. A last ditch effort may require a pair of Vise-Grips or sockets designed to grab deformed bolt heads. For stuck, slotted-head bolts, an impact screwdriver can be a real lifesaver
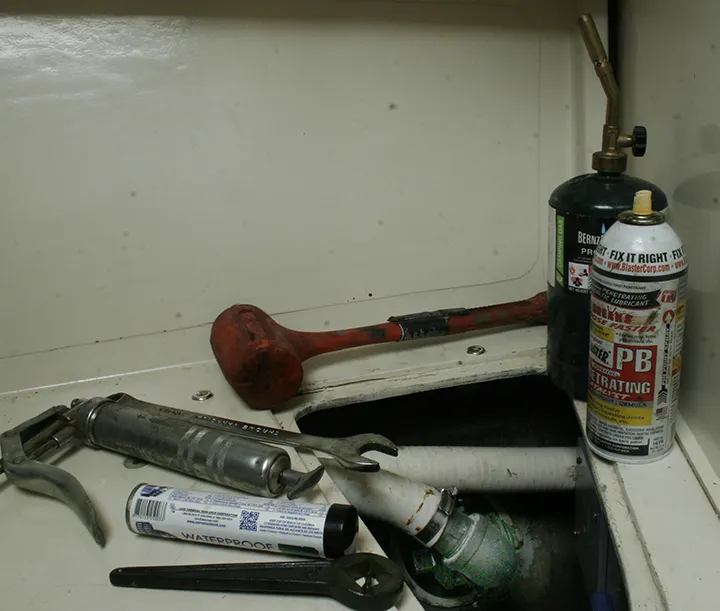
“Frozen, rusted nuts present a similar problem, but there are tools that allow you to split the nut without destroying the bolt. Nut crackers use a chisel-like edge that is screw-pressed against the side of a nut. Once the tool is tightened, a machinists hammer is used to smack the tool, and its blade splits the nut.”
If seized hardware in spars is your problem, extraction and retapping or new rivets may be your only option. If you are adding or replacing hardware on your mast and boom, two relevant reports can set you on the right path. In “Anti-seize Coatings for Spars,” (PS July 2018) and “A Riveting Report: Spar Fasteners.”
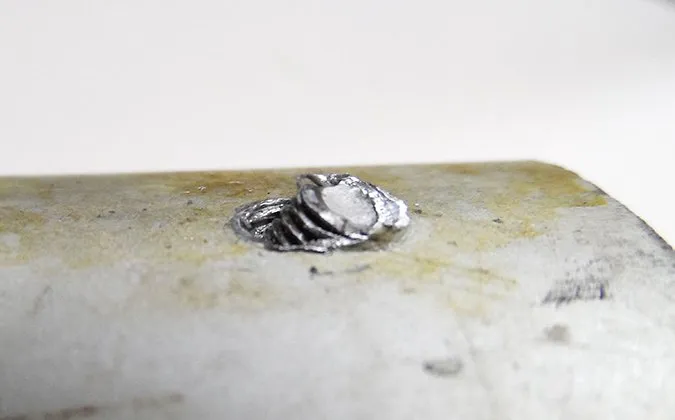
As for my own project on “Opal,” the seized tapered-cone bronze seacocks eventually freed with only a little coaxing and spray. The process described in this ancient, but still perfectly valid Practical Sailor article on keeping seacocks working smoothly was very helpful.
Freeing this leaking water pump from ye ol’ Universal Diesel 5411 took a little more patience. I doused the severely corroded mounting bolts in PB Blaster and returned the next day to begin coaxing them free. Gentle tap, tapping with a peen hammer—I hoped—would break the bonds of corrosion in the threads.
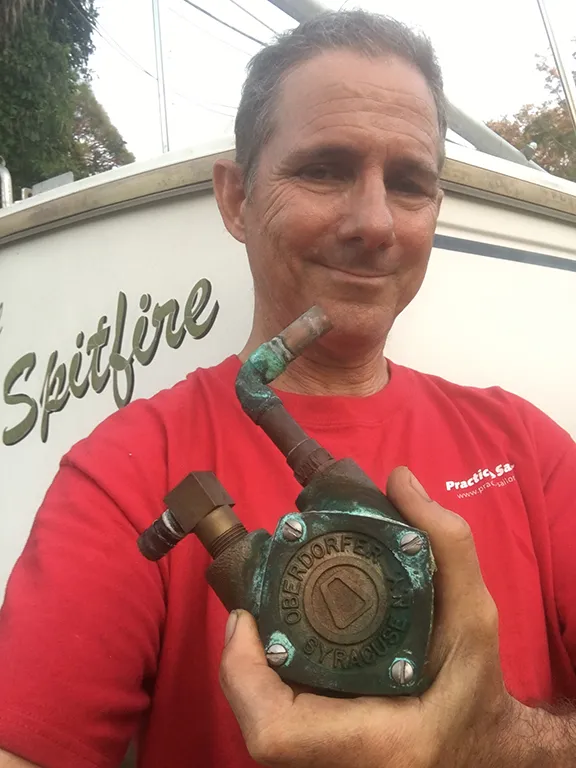
As I fitted my breaker bar and a six-point socket (12-point, bi-hex, sockets are more prone to stripping) that fit snugly on the mounting bolts, I was already going through my options if the bolts were stripped during the extraction process. None of them were cheap. I started tentatively, adding a six-inch extension to the breaker bar, giving me about 18-inches of leverage on the 3/8-inch mounting bolt. When the most corroded bolt budged, I breathed an immense sigh of relief, but instead of further loosening it, I applied a little more spray, tapped some more and moved the bolt back and forth before advancing it any further. In many ways, steel engine bolts are far more forgiving than stainless steel, which can gall, creating a nearly impossible-to-break bond.
Now for the next engine project, the dreaded shaft coupling bolts. Time to break out the Allen wrenches. If you have a favorite “secret sauce” for loosening bolts that we should test, let us know in the comments section.
I love that you talked about being careful when applying force to avoid breaking a fastener. My husband is looking for marine fasteners for his boat and he wanted to get tips for working around it during maintenance. We will keep these tips in mind as we search for a professional that can help us out best.
Useful info. Eventually most of us if you haven’t yet will encounter a stuck nut. Back in the ’70s worked in a bicycle shop. When most bicycle frames were made of steel. Many bikes brought in corrosion fused stems, seat posts. Releasing agent, time, torque would usually free the parts. Occasionally there were the real stuck parts. Out came the heat and cold. The rapid thermal change would cause the corrosion bond to break. Bit more aggressive than your cold only process. Probably more limited application if any.
A very good article Darren. Growing up on a farm, I am also very inventive when it comes to finding ways to remove 50 year old rusted bolts and nuts. Like you say, the biggest danger is that you will break it and then really have a mess on your hands. Time really is your best friend… all of these penetrating oils need lots of time to work properly. You are depending on a chemical reaction to break down the iron oxides and that takes time (and a bit of brushing to loosen up the scales and give the oil a better chance of penetrating. If I have a really stuck fastener, I’ll spray it on liberally and wait 24 hours, brushing it on often. Back and forth with lots of lubrication once you get movement… heat also helps (heat the nut not the stud) but I’ve also found that Liquid Wrench is as good as PB Blaster and generally it comes in a squirt can so much easier to apply upside down and twisted like a pretzel.
“As I fitted my breaker bar and a six-point socket (10-point sockets are more prone to stripping) that fit snugly on the mounting bolts,” ER, and on yachts from which country does one fine five sides bolts that might be gripped with a ten point socket?
Very good Garry, I was about to respond in the same way but you beat me to it.
There metric. lol
A sailboat rigger friend introduced me to “Freeze Off” spray 30 years ago and it’s been a mainstay in my toolbox ever since. I’d long known about torching and cooling rusted-on frozen fasteners to break them loose through expansion and contraction, but he taught me that the same type of expansion and contraction cycles could be accomplished through supercooling cycles, reducing the posibiity of torch caused heat damage to surrounding parts.
This lesson was hammered home when another local rigger fell from the mast head when the torch she was using to free a frozen nut melted the halyard she was hoisted on.
“Freeze Off” is but one brand of supercooling spray available and others I’ve tried work equally well.
I’ve had good luck with a mixture I found recommended by an old hand somewhere on the web a few years ago.
It’s 50% automatic transmission fluid (red Dexron or Mercon) and 50% acetone. It can be sprayed from a repurposed kitchen-cleaner bottle or used in a small tray to soak fused parts. Clean and dry the parts when done, leaving a slight oily sheen.
In the last few weeks I have failed to free steel bolts from aluminium. They are the devil. I have tried everything on one – an outboard. Now I am struggling with a windlass. On the outboard I tried WD penetrant, heat, tapping etc.
Best bet is to drill it out and put a helicoil in if it is in a place that this can occur; it will be far stronger than just threaded aluminum. I’ve done it on motorcycle parts frequently.
If the heads are in good shape, a cordless impact driver, typically used to drive decking screws, can be useful. The downside is that the tool is powerful enough to distort the nut or bolt head, but most of the time power persuasion works. It a real risk to use it on Philips head screws. Push hard on the tool while using. A representative tool is a Milwaukee 2853 Impact Driver.
There are special purpose tools that grip ruined bolts and screws. Search Amazon for bolt extractor and Easy-Out.
If all else fails, a Dremel style tool with an abrasive cutoff wheel can remove the head. I find the cutoff wheel much easier to use than nut breakers, etc. It is also possible to drill out a fastener, but cutting oil is a must. If the fastener is threaded in, removing the head won’t be enough. You will have to drill out the remains, tap new threads, and use a slightly larger replacement fastener. Try an Easy-Out first.
Well, I got some good info in here, however, I used in the past (quite a few times) something you might luff at as it was regular classic COCA-COLA! Yes, it did work! It also works on winter salty dirt on your windshields!
Patience and lots of penetrating oil will often free stuck nuts and bolts also try tightening the stuck bolt slightly, even a fraction of tightening movement will often free it.
In my youth I hung out in an outboard repair shop. The mechanic taught me two things. Heat the metal around the bolt with a torch. He called it his smoke wrench. The other thing he taught me was to coat the threads with Aviation Permatex #3 when you put them back. He never had a problem disassembling them the next time they came in for service.
The idea of shrinking the bolt with cold should work as well as heating the surrounding metal. There are now sprays on the market to do just that. I haven’t tried them yet but I have a can in my shop. The dry ice I was keeping on the shelf disappeared. Someone must have borrowed it.
We can add the Magnetic Induction Heater as a tool to remove bolts, seacocks, NPT to Hose barb… where a flame would not be safe.
My father was an auto mechanic and I learned a lot from him. Patience is the first lesson. Correct tools as well – as you say, 6 point sockets. Another trick is to try to slightly tighten the fastener to break the rust bond; the hidden threads will not have rust, or as much rust, since they’ve been sealed in. A very slight amount is all you want, and if it doesn’t budge, don’t force it and break the thing. This is best used for large fasteners, like lug nuts, to avoid breakage. As for lug nuts, never put them on without a coating of moly-coat/anti-seize compound.
Screw and nut extractors are cheap and can be very handy.
If you break a bolt, or simply can’t get it out, centre punch it and drill into it with a small drill bit. Use cutting oil, don’t push too hard. Usually the drilling itself will loosen the remnants. If not, use the extractor. Don’t break one of those in there, or the cutting torch is your only option (ask me how I know).
A rounded bolt head can be filed flat and an open end wrench used. Pipe wrenches can work too since they tighten down as you put torque on; but don’t use them for nuts as they will squeeze and create even more friction.
A file or Dremel tool can cut slots in a bolt or nut head to get some purchase with a chisel. Either can also completely remove a nut, as could a hacksaw blade, oscillating tool with metal cutting blade, or even an angle grinder if you have room.
Few things are as satisfying as the moment you do get the impossibly stuck piece out.
Safe sailing!
To use the heat/expansion method of freeing stuck fasteners/screws/bolts without burning the surrounding area you can use your engine battery. Hook up one end of the jumper cables of sufficient length to reach the item to the battery. Then at the other end attach one of the leads to the thing to be freed, and the other lead to the closest point available. The intervening metal will soon become quite hot, red hot even. Watch closely and disconnect when desired temperature is reached.
1) Best. Penetrant. Ever.
Kroil by Kano Laboratories in Texas. All others bow in Awe & Shame!!! Look online and find home-brews that *attempt* to equal the overnight magic it offers professionals & shade tree mechanics alike!
2) For thermal attack, on the cold side; grab a can of computer dust spray: turn it upside down & it will spray *liquid*!! Avoid contact & ensure fresh air supply at all times!! Cheap & effective.
I’ll second the recommendation of Kroil, formerly Aero Kroil in a spray can. A local foreign car repair shop in RI used it and we adopted it at our spar shop in Bristol, RI. It’s the best.
For frozen nuts I have had lots of luck heating the nut red hot with an acetylene torch and immediately pouring cold water on the nut. The thermal shock breaks the nut loose from the bolt and usually comes off easily. For small bolts that break off drill all the way through the bolt with a drill size that allows a bolt extractor to work. Heat the bolt and melt bees wax (from a sewing or craft store) against the hot bolt. The bees wax has a very low viscosity and works it’s way into the seized threads allowing easy removal of the broken bolt. I learned these tricks from working as a diesel mechanic for 45 years.
Threadlocker (Loctite) not only keeps bolts from coming loose but also fills the space on the back side of the threads to prevent rust. An NCT bolt only has about 15% thread engagement leaving lots of space for moisture (rust). I use blue thread locker on everything I put together.
It makes a mess, but I ALWAYS use NeverSeez when ever I put something back together on my 20 year old boat. I can attest that even stainless bolts through aluminum threads exposed to the salt water environment always free up with a minimum of effort. I’ve thought many times about going over the whole boat and Never-Seez ing every bolt I can find, but alas, there are always more pressing projects to do.
Working at Economy Tackle in the “Fishing Reel Service and Repair Department”, we come across corroded, frozen, rusted screws, nuts and small parts daily.. We’ve had good luck using JB Blaster in the past but, when we have to apply a propane torch as well, man does that stuff stink.. This past year we tried a new product from Seafoam Company called “Deep Creep”.. Works fantastic and smells good whether we use the propane torch on it or not.. It’s our “go to” spray now, we use it every day..
Time is your friend when it comes to removing corroded – stuck fasteners. If you have the time , dousing them every day or so for a week will definitely help even the saddest cases. Penetrants work their way in VERY slowly. Also if a bolt head is a bit undersized from rusting or previous abuse sometimes there MIGHT be one that fits a bit tighter – if its English try metric etc.
Another superior penetrant product is Gibbsbrand (gibbsbrand.com). It has worked wonders with rusted fasteners and seized pistons in engines. It is worth testing along side the other products if PS has not already done so. Employing patience with any penetrant is generally essential, but patience is typically in short supply. I concur with Kent and Parks to always use anti-seize compounds, except for instances when loctite must be employed to preserve the integrity of the assembly.
That’s really nice post. I appreciate your skills. Thanks for sharing.
Faced with a stripped Allen head bolt in the shaft coupler on my boat, I searched the internet for suggestions and solutions. A video on YouTube suggested driving a slightly larger torx headed bit into the stripped Allen head recess in the frozen bolt. After a two-day treatment with PB Blaster, the bolt responded to the torx head bit and saved me the nightmare of drilling the darn thing out while dangling upside down in the shaft space!
My $.02: If the threads beyond the nut are accessable wire brush the rust off before adding penetrant. Otherwise as you unscre the bolt/nut, the rust particles combine with the penetrant & form a mud that gets pulled into the threaded hole. This increases the friction evaporating the lubricant leaving you worse off than when started.