The true test of marine gear is not whether it works when installed, but rather how it functions after years in the field. To that end, we have left samples of sewing materials and sewn test samples in the sun, wind, rain, and snow for two years, and have also sailed with sewn samples in service on our test boat.
Why sewing? The main impetus behind this series of tests was the desire to put eye splices in old braided lines as well as to incorporate webbing into various rigging and marlinspike projects. Webbing almost always requires sewing, and sewing is often the only way to put an eye splice in older braided ropes. Even if an older, braided line is still soft enough to splice, most riggers advise against it. Fortunately, stitching an eye splice proves to be an excellent alternative.
For our first round of evaluations, we load tested various stitched splices. Here, well see how well these splices and related protection products held up in a variety of onboard applications.
What We Tested
We tested three types of products:
Whipping twine-We tested both polyester and Dyneema (PS, December 2014) whipping twine, along with sewn splices using each in webbing.
Physical cover protection-Heat shrink tubing, tape, and tubular webbing remained in service on tethers, traveler lines, and genoa sheets with mixed results.
Coating protection-We also looked at products that protect onboard stitching from UV and chafe: latex paint, rubbery surface coatings (liquid electrical tape, 3M 5200, etc.), and impregnating coatings (Spinlock RP25 and Yale Cordage Maxijacket). We tested these on both sewn splice samples and shackle splices. The RP25 and Maxijacket coatings were big winners in the chafe resistance review (PS, March 2015). The test samples that these coatings were applied to are still in service on our snubber, dock lines, and furler line.
How We Tested
We tested in the lab and in the field.
Laboratory-To long-term test stitching protection against UV, testers fabricated 8-inch dog bones (a short length of line with an eye spliced in each end, commonly used for strength testing) of 1-inch tubular webbing, 9/16-inch webbing, and 3/8-inch polyester double braid. Each was sewn with 0.8-millimeter, waxed polyester whipping twine, coated with test materials (RP25 and Maxijacket), and left to weather. Control samples were kept indoors. All samples were broken at two years. Unprotected line, webbing, and whipping twine (0.4, 0.8, 1, and 1.5 millimeter) were also tested.
Onboard field test-Several webbing dog bones were kept in the test boats rigging (mainsheet, topping lift, davit tackle) so that they would be subjected to both weather and load. We also observed the function of several splice coverings and rope slices.
Laboratory Findings
Waxed polyester whipping twine samples retained about 58 percent of original strength after two years in the Virginia weather, or 21 percent loss per year. Dyneema lost slightly less strength, retaining 66 percent of its initial strength after two years and losing 17 percent per year. Most likely, the wax coating provided considerable protection for the polyester twine, whereas the white, slender Dyneema was naked. This compares well with industry data for desert locations.
The performance of naked, sewn splices was surprising. After two years in the sun, we measured no loss in strength among the samples. The samples broke at about 80 percent of webbing minimum breaking strength. Because all of the splices tested at full strength, we couldnt determine the effect of protective coverings or coatings.
We expect the decline in the strength of the thin, naked twine to be fairly linear with time at about 20 percent per year. Rope also loses strength in the sun, but the UV damage begins to level off after two to four years with 65 to 75 percent of its original strength. Most of the damage is to the cover. Because a sewn splice can be over stitched-our recommended stitching schedule includes a 2:1 safety factor-the strength at five years remains equal to the line.
Previously, we reported that for highly loaded polyester lines (genoa sheets), polyester whipping twine results in a stronger and more durable splice because the twine stretches as much as the line, distributing loads evenly, while less-stretchy Spectra stitching tends to tear through. However, we also reported that Spectra is more chafe resistance. Since our first test, we learned that Dyneema twine is minimally more UV resistant than waxed polyester twine. In our view, Dyneema is just as good as Robline polyester for stitching projects. The waxed polyester twine is more pleasant to work with, but the durability of the Spectra is impressive.
Onboard Field Test Results
Splices will always be the gold standard for durability, but they can be bulky and arent recommended for used rope. Knots and sewn splices are alternatives.
We tested sewn splices in-service by inserting dog bones into the rigging, just as you might add an extra shackle. The intention was to look at the effect of cyclical loading and abrasion. The samples suffered no significant chafe. Some were coated, and some were naked. Although these are not highly loaded applications, we also under-stitched the splices by 75 percent so that we could induce failures in the stitching and not the webbing; in other words, they were operating at reasonably high load factors. Again, they showed no strength loss, within experimental error. This agrees with actual practice, where we have lost a few webbing slings over the years to chafe, but never failed stitching.
A sewn splice on the test boats traveler car had to be removed in order to replace a failed fairlead. We had chosen a sewn splice in order to test its longevity and because the long tail of a double braid splice would have restricted the movement of the car. After replacing the fairlead, we simply tied a bowline, which also allows free movement but is easier to undo to remove twist in the line. In the end, we decided the splice looked more seamanlike, but a knot did just as well.
On the other hand, we are quite pleased with other tested applications. Splices on our genoa-sheet splices, with their heavy-duty chafe protection, eliminated a nasty snagging problem, and allowed us to re-use an old sheet. They show no wear after five years of frequent weekend use.
The rubbery coatings we tested were uniformly disappointing. Both Liquid Electrical Tape and 3M 5200 abraded easily from high spots.
Using latex paint in this application seemed a little silly, until the crew of a tall ship explained that they had switched from tar to black latex paint for seizings because it was so much easier to work with. We applied the latex paint to tether ends and topping-lift splices. Though initially, testers didnt care for the feel, we admit it seems practical in many places. Basically free, easy to apply and renew, durable, and available in whatever colors are in your paint locker, the latex paint hasn’t failed us.
Testers continue to be impressed by the RP25 and Maxijackets performances. RP25 has effectively stopped drum-exit chafe on our furler line. Maxijacket has slowed what was rapid chafe on our docklines to the point where it is imperceptible; note that this is chafe on a relatively smooth surface, like a chock, and we would not expect the same performance on a truly aggressive surface. However, it works in places where chafing gear either will not fit or will not run well.
Whipping Twine
For stitching, seizing, or preserving stitched splices, we needed good twine that was easy to handle and lasted. We reviewed various twine products from Marlow, Robline, and Berkley in the December 2014 issue and recommended several of them. The aging tests didnt change our recommendations, although the Spectra twine seemed to lose slightly less strength to UV exposure than the other types.
The larger spools of waxed polyester from FES Robline are very affordable and remain our Budget Buy. The braided No. 10 thread earned our all-around Best Choice for excellent strength and ease of sewing, and the Robline No. 15 is best for heavier jobs; the Marlow No. 16 is a good choice if you want a smaller spool and for heavier projects.
FES Roblines Dyneema sews well without wax, but because it is so thin, it is not as easy to use as polyester. Its small dimensions also make it a poor choice for whipping ends of lines or for serving a splice. On the other hand, Dyneema twine shows exceptional abrasion resistance, wearing five to 10 times longer than polyester twine, making it a better choice where abrasion is concerned.
Since we always have some fishing line in our tackle box line, we decided to try Berkleys Fireline, a fine Spectra with a considerably stiffer feel than the Robline Dyneema. The Berkley and two other whipping twines-from Marlow and Sherrill Tree-earned our Recommended rating.
Physical Coverings
We tried several different physical covers to protect our sewn splices from the sun. Some, like electrical tape, were clearly easier to apply, and others, like whipping, looked more seamanlike. Our long-term test helped us find a middle ground, something that looks good and lasts.
Whipping
For covering splices, we used the same No. 8 whipping twine that we use for the seizings. We applied it very tightly (lines shrink under load and the whipping becomes loose). You can expect to use about 10 feet of twine to cover each half-inch eye splice. Using two layers, plus a coating will increase durability.
Bottom line: We Recommend using twine, if you like a traditional look.
Heat shrink tubing
To test heat-shrink tubing as splice protection, we used three-quarter-inch Gardner Denver tubing. We tested this on tether ends, and after two years, it still looks new. It was fast to apply, although a special size is needed for each size line. It costs about $9 for an 8-inch section.
Bottom line: Heat-shrink tubing provides a neat finish for applications with limited abrasion and snagging potential. It is Recommended.
Tubular webbing
We tested New England Ropes Climb-Spec tubular webbing for chafe protection on dock lines for 20 years, and its proven as durable-perhaps more so-as the line. Secured with stitching or seizing, tubular webbing requires only occasional inspection. Often it can also cover an adjacent lashing, providing a cover that can be slid easily aside for inspection.
The materials thickness makes splicing in the ends or whipping them impractical, but it heat-fuses well, and no further finishing is required. While this looks a bit unfinished, it has proven very durable. Pricing varies from 30 to 68 cents per foot.
Bottom line: Heavy-duty physical coverings, like tubular webbing and leather, are the most durable answer for protection. It gets the Budget Buy pick for splices that will see heavy wear.
Electrical Tape
We used 3M-brand electrical tape. Testers have found that even with no abrasion, it comes loose in two years. Prices run about $5 for a 22-yard roll.
Bottom line: Expect to replace it every year, or more often if there is wear.
Line coatings
From the beginning, we were dubious about any sort of coating that can be painted on a line. It just seemed too easy. We tested two types of coatings, those designed to protect against chafe and lock the fibers together (particularly useful in highly-loaded rope clutches), and those that also provide some physical barrier to against the sun.
For chafe protection and for locking fibers together, a couple of specialty products from Yale Cordage and Spinlock impressed testers. Our long-term findings have convinced us that these relatively new products are just as handy for the cruising sailor as they for racers.
Two coatings recommended by readers for protection against chafe and weather-liquid electrical tape and 3M 5200-fell well short of expectations, but ordinary latex paint proved to be a decent option for the low-budget sailor looking to keep the sun and salt off splices.
Yale Maxijacket
Yales Maxijacket is a quick-drying, water-borne, polyurethane coating that both soaks in and stays on the surface. While it stiffens line considerably, it also increased chafe resistance against wood and grindstone on the chafe machine, and carabineer and seabed on our test boat by five to 10 times. It was pretty impressive for a product that brushes on in moments and cleans up with water. Splices can also be dipped, firming them up a bit, locking them together, and providing even deeper chafe protection.
The drying time is typical of a latex product; it dries to the touch in a few hours and is ready for use in 24 hours, with maximum wear protection in about two weeks.
Formulated specifically for protecting rope, Maxijacket is a real winner. Some users have reported that the colors can rub off onto the deck; we tested the clear product and were happy with it. It costs about $7.10 for a 4-ounce jar or $40 to $50 per quart.
Bottom line: Useful on both tucked splices and sections of line prone to light abrasion, Maxijacket earned the Best Choice pick for protection of polyester line.
Spinlock RP25
A high-dollar coating, the RP25 is intended to reduce cover/core slippage, increase durability in clutches, and reduce chafe. Solvent based, it soaks in deeper but is messier to work with than Maxijacket.
The RP25 does not offer as much chafe protection for polyester line as Maxijacket does, but that is not the focus of the product. The manufacturer recommends RP25 for protecting highly loaded lines of larger boats; we tested it on a chafe-prone roller-furling line and have been very pleased.
Splices should be either dipped or very heavily coated with the RP25; two coats are recommended, if abrasion protection is a concern. It costs about $50 for 250 milliliters or $200 for 1 liter.
Bottom line: The RP25 is useful on both sewn and tucked splices, as well as sections of line prone to light abrasion. It stiffened the line much less than Maxijacket. We have no reservations about rating RP25 as Recommended, particularly for ultra-high-molecular-weight polyethylene (UHMPE) line, in spite of its higher price.
Latex Paint
We tested Painters Touch Latex Paint, but any ordinary latex will do. Cheap, easy to apply (two coats), and available in many colors, latex paint has become common coating for protecting rope seizings on tall ships. It costs about $16 per quart, but you could use whatever you have on hand as well.
Bottom line: Latex isn’t very comfortable to handle, but for protecting stitching that sees limited abrasion, it is a very affordable option.
Conclusion
We continue to like tubular webbing for heavy-duty chafe protection and Maxijacket for places where an added layer can’t work. Heat shrink can serve well in light-duty applications.
We expect well-sewn, stitched splices to remain at full strength for five years or more. Dyneema twine, because of its greater resistance to UV and chafe, should be used in all but the highest load applications and should last as long as the line, whether covered or bare. Covered, stitched polyester splices can last as long as the line. In low-load applications-those where a splice is desirable for neatness or space savings-either paint or heat shrink is enough to make them permanent. For high-load applications, tubular webbing, leather, or some other sturdy chafe guard material is preferred. We upgraded our position on Dyneema twines from Recommended to a tie for Best Choice, based on better UV and abrasion resistance. We continue to like Robline twines.
As always, the right termination depends on the job: Use knots where short length and removability are critical; sewn splices for used line, webbing, and tight spaces; and conventional splices where abrasion resistance and peak strength are critical. All terminations should be inspected regularly; all are vulnerable to wear and loosening.
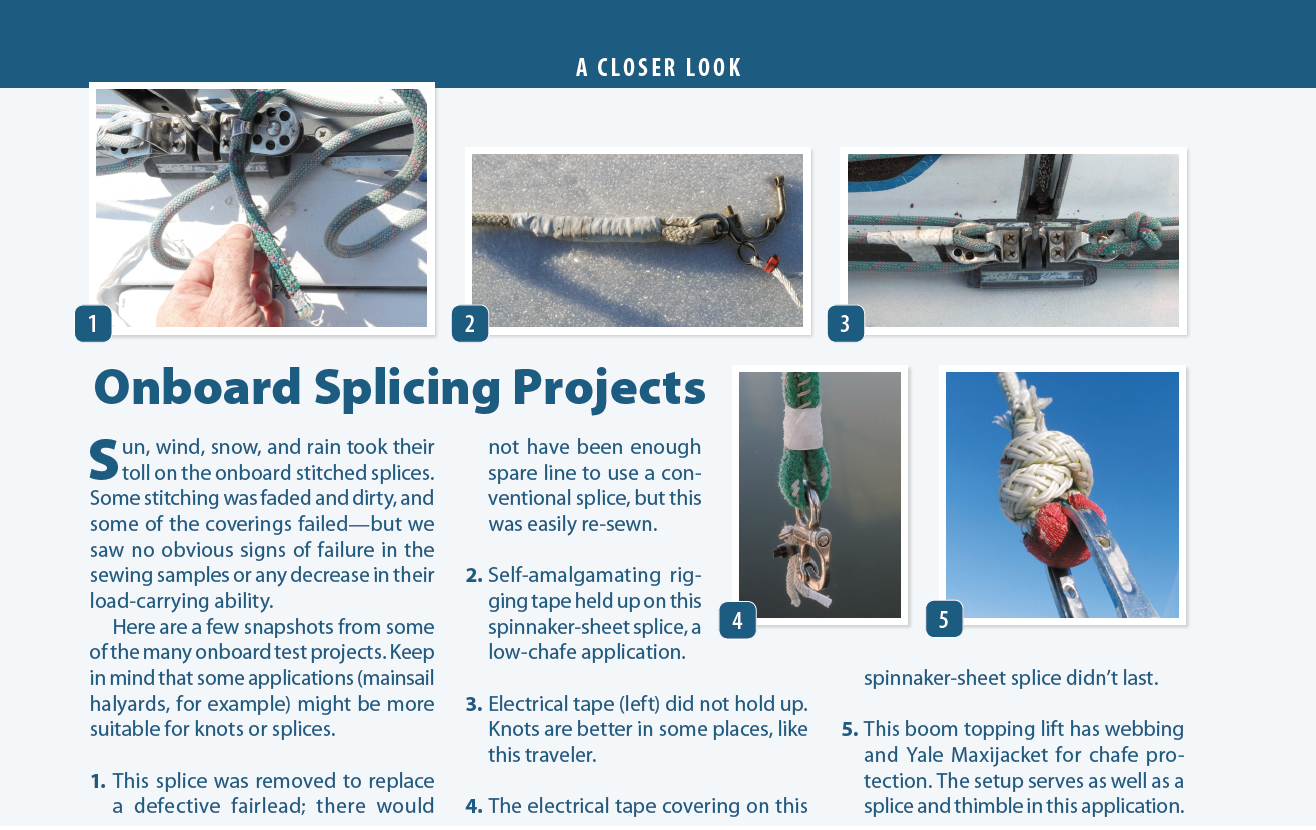
Sun, wind, snow, and rain took their toll on the onboard stitched splices. Some stitching was faded and dirty, and some of the coverings failedbut we saw no obvious signs of failure in the sewing samples or any decrease in their load-carrying ability.
Here are a few snapshots from some of the many onboard test projects. Keep in mind that some applications (mainsail halyards, for example) might be more suitable for knots or splices.
1. This splice was removed to replace a defective fairlead; there would not have been enough spare line to use a conventional splice, but this was easily re-sewn.
2. Self-amalgamating rigging tape held up on this spinnaker-sheet splice, a low-chafe application.
3. Electrical tape (left) did not hold up. Knots are better in some places, like this traveler.
4. The electrical tape covering on this spinnaker-sheet splice didnt last.
5. This boom topping lift has webbing and Yale Maxijacket for chafe protection. The setup serves as well as a splice and thimble in this application.
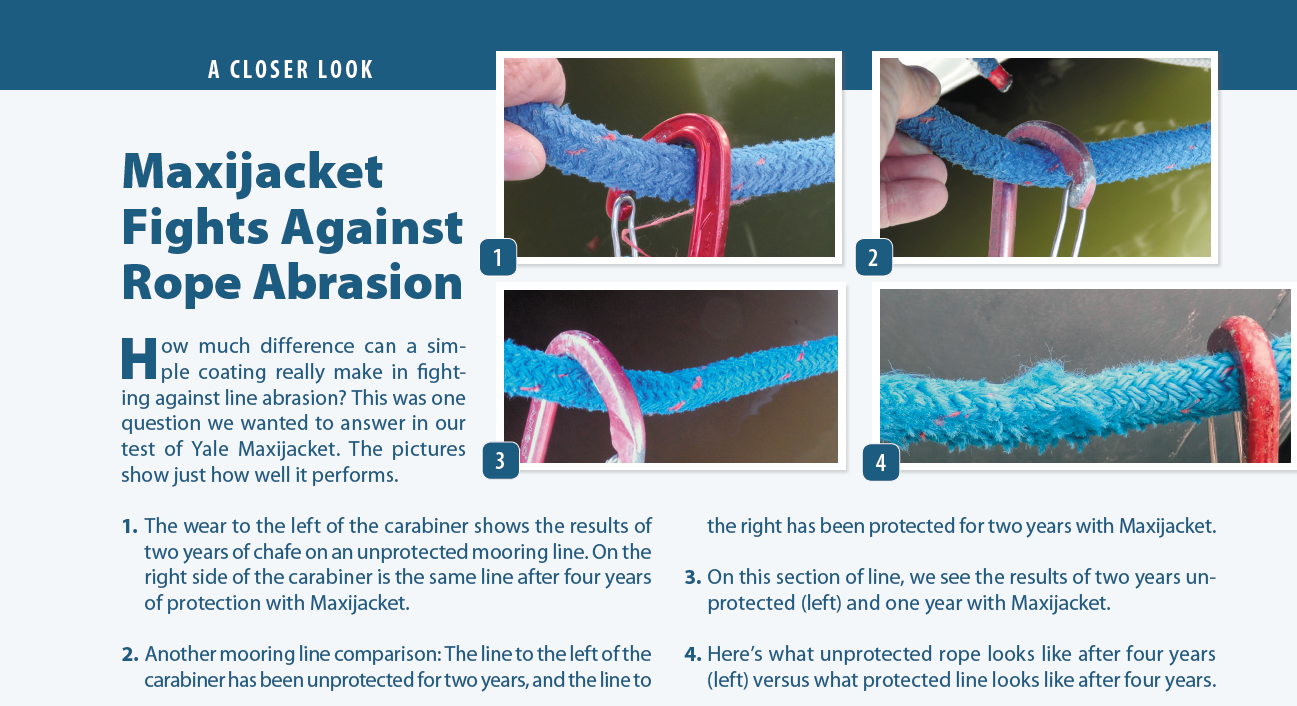
How much difference can a simple coating really make in fighting against line abrasion? This was one question we wanted to answer in our test of Yale Maxijacket. The pictures show just how well it performs.
1.The wear to the left of the carabiner shows the results of two years of chafe on an unprotected mooring line. On the right side of the carabiner is the same line after four years of protection with Maxijacket.
2. Another mooring line comparison: The line to the left of the carabiner has been unprotected for two years, and the line to the right has been protected for two years with Maxijacket.
3. On this section of line, we see the results of two years unprotected (left) and one year with Maxijacket.
4. Here’s what unprotected rope looks like after four years (left) versus what protected line looks like after four years.