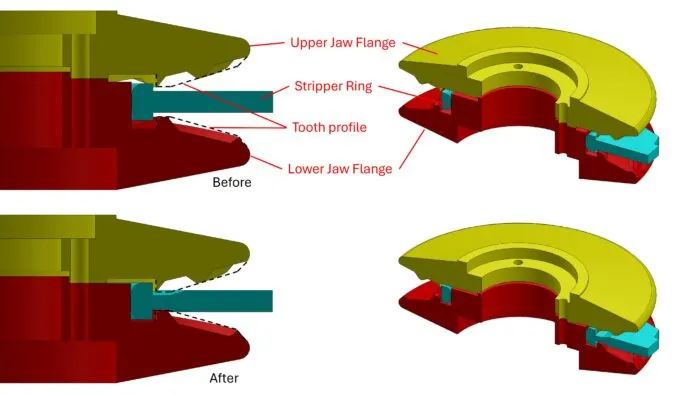
I love my winches. Like a trusted companion, they have been with me through thick and thin and have always performed for me when I needed them. They are a little old, like their owner, but they are strong, well cared for, and with regular maintenance, in no danger of wearing out. However, they have just one problem, and it’s a big one.
In our constant quest to modernize and upgrade our vessel, we have started using high strength, low stretch ultra-high molecular weight polyethylene (UHMPE) sheets and halyards. Our new 1/2-inch (12 mm) genoa sheets significantly outperform our old 5/8 inch (16 mm) polyester sheets. In fact, almost every highly stressed control line in the boat has gone to a smaller diameter high modulus line. Our primary winches are vintage 2-speed, self-tailing Lewmar 52STs—a very popular winch on boats from the 1980s and 1990s, that are still in common use today. Like many first generation self-tailing winches, the 52STs have a fixed, self-tailing jaw V-groove that was originally sized for big fat polyester line. Our new 12 mm sheets slip under high loads and our 10 mm light air spinnaker sheets are out of the question for use in the self-tailer. So, should we abandon our old friends and get new expensive winches that handle smaller line?
NARROW THE GROOVE TO HOLD THINNER LINE

Fortunately, a simple modification can rescue older self-tailers and assure many more years of useful service. In a nutshell, the modification we are making is simply moving the upper jaw flange and the lower jaw flange closer together, narrowing the V-shaped groove between them so it can grip smaller diameter line. The modifications described herein are specific to the Lewmar 52ST, however the same principal can no doubt be applied to other sizes, models and makes with a little reverse engineering.
USE A LATHE, WITH CAUTION

The modifications described here require the use of a lathe. I realize not everyone has access to a lathe, but there are plenty of machine shops around that would be willing to take on a small job like this, as long as you can accurately describe what you want done. Again, instructions to the machine shop should be based on your measurements. The dimensions I give here are what worked for my winch. Yours might be completely different. If you do decide to take on machining the parts yourself, the parts being machined are plastic and well within the capabilities of most hobby lathes, provided you take slow gentle cuts. Patience is key here, as an aggressive lathe cut might grab and ruin a part for which no spares are available. Proceed cautiously at your own risk.

The goal. The owner’s manual tells me our winches are rated for 1/2- to 3/4-inch (12 to 18 mm) diameter line, though as mentioned, 12 mm is marginal at best. My goal was to reliably handle our 12 mm UHMPE racing genoa sheets as well as our 10 mm light-air spinnaker sheets. I suspect we will never use ¾-inch (18 mm) ever again, so reducing the V-groove gap by a little more than 1/8 inch (3.2 mm)—let’s call it 0.15 inches (3.8 mm)—should be just about right.

Shave off extra width on jaw flange. On the Lewmar 52ST, the upper and lower jaw flanges are bolted to the winch drum and sandwich the stripper ring between them (See fig 1). The top and bottom surfaces of the flanges meet and determine the width of the V-groove opening. The stripper ring must be free to rotate and not interfere with the flanges, including the radial “teeth” on the inner groove surfaces. The easiest way to narrow the V-groove with by .150 inches (3.8 mm) is to take that amount off the top surface of the lower jaw flange, while preserving the locating boss that keeps the flanges concentric and shortening it by the same amount (see fig 2).

Assess stripper ring clearance. Once modified, fit the upper and lower jaw flanges together with the stripper ring sandwiched in between. If the stripper ring does not rotate freely between the jaws, you will have to relieve the part of the stripper ring that interferes with the “teeth” on the flanges. It may be tempting to simply grind back these teeth, rather than relieve the stripper ring, but this would compromise the V-groove’s ability to grip smaller line, which, after all, is the whole point of this exercise. For my winch, there was generous clearance between the flange teeth before the modification, so I only had to remove a small amount from the stripper ring to clear the teeth. Measure the tooth gap with the flanges together and relieve the stripper ring until it moves freely with about 1/32-inch (1 mm) clearance.

Reassemble. Once the modifications are made, all that remains is to reassemble the winch and test it with your new high modulus line. The reward is many more years of service from a trusted old friend.
Neat!
I always just covered the tails with polyester covers to match the existing winches and clutches (not genoa and spin sheets–they don’t commonly go through clutches, except on some of today’s over-clutched boats), but this certainly saves a lot of bulk, particularly with the spin sheets.
I have the lathe and skills, I just never considered this surgery. I think it is because I like the feel of the fat lines in my hands and find the fat tails easier to haul by hand during tacks and jibes.
But very cool.
For those of us on the Eastern Shore of the Chesapeake without those skills, it is getting more and more difficult to find the old machinist who can seemingly take on projects like this with aplomb. It is a dying art that is being replaced by CAD/CAM machines that cost a fortune to buy and hire. This looks like a project that some enterprising techy could take on and produce on demand with 3D printing once the design work is done. I think that 3D scanners might even be good enough now to avoid the laborious and error-prone process of hand-design.
Whaddya think?
Why not? A year ago I would have argued FDM printing wouldn’t be strong enough for the application, but I’m seriously impressed with some of the new materials, PETG CF (carbon fiber filled) in particular is my go-to material these days. I hope to address 3D printing boat parts in a future article, so stand by.
I’ve been searcing the Internet for a solution for this exact model winch with no sucess…until today! This is the kind of PS content that keeps the fleet running for the rest of us.
Get lines with a larger diameter or new winches.
A perfectly viable solution. It’s nice to have options.
Backing up a step here, you say “Our new 1/2-inch (12 mm) genoa sheets significantly outperform our old 5/8 inch (16 mm) polyester sheets.” Can you explain in what way the smaller lines outperform the larger ones (setting aside the issue of new vs old)? To me it seems the smaller lines would be less comfortable to handle.
By performance I am referring to strength and stretch resistance. A hi-mod 1/2” line beats a 5/8” polyester in both these categories. You are not the first to mention the comfort factor in larger line.