Nylon three-strand dock lines, anchor rodes, and mooring pendants are the sailors safety net, so to speak, and have been for nearly a century. But as often happens with gear that has stood the test of time, the reliability of this cordage has to some degree given way to a false sense of security. Sun, sea, and salt rob rope of its tenacity, but just how much has never been accurately quantified.
Being skeptics at heart, Practical Sailor testers suspected our old nylon lines were a lot weaker than we thought, and decided to see just how much original oomph an old set of dock lines actually retained over time. In order to take a closer look at this issue of line longevity, we rounded up a set of in-service dock lines with a known history, and enlisted the patient help of Steve Parola and his quality-control team in the lab at New England Ropes.
Our approach was to take the weathered 10- to 12-year-old nylon three-strand line, cordage that for half of its life had been used as part-time dock line, and for the other half, enlisted as full-time (24/7) dock line, tethering a 41-foot sloop to a fixed pier in a very protected cove on the Chesapeake Bay. The nylon had weathered significantly, and chafed noticeably where the lines exited chocks and made contact with cleats. Our plan was to put these lines under increasing tension in laboratory conditions and test them to destruction (See “The Fine Art of Stretching Lines Until They Snap,”.)
During each test, it was interesting to note that as the nylons elastic deformation range was exceeded, filaments began to permanently stretch and the line would not return to its starting length when the load was removed. This is a classic example of what happens when a material exceeds its limit of elastic deformation and moves into the tenuous realm of plastic deformation. As the load was reinstated and continued to increase, there were crackling sounds of intra-strand filament failure, and in several cases, the throw, or length, of the dual rams extension was not long enough to break the line in one run. In such situations, the ram was retracted and the permanently stretched line pulled shorter prior to the final test to destruction. The amount of elongation in the tested ropes prior to destruction was impressive, but it was still shorter than the up-to-25-percent elongation that new nylon cordage will exhibit prior to failure.
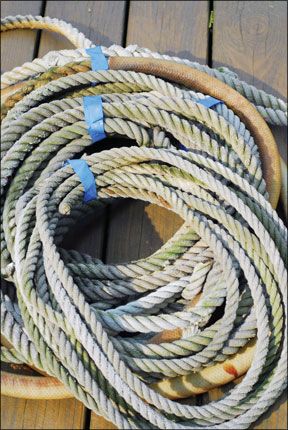
Inspection
A close inspection of the frayed ends of each parted line provided some interesting data. The first issue of interest was that some lines became very stiff and outer filaments along the entire line began to rupture, giving the line a fuzzy feeling. A few of the samples, specifically those with spliced ends or more serious mid-line chafe actually failed at these weak points and did not show total filament failure along their entire length.
Underlying all the destruction tests was the important lesson in elasticity. Each nylon line tested proved that once its elasticity had been exceeded, and the materials yield point met, a spectacular ending was imminent. As the filament strain reached a critical level and the line neared its failure point, everyone was backing away from the jig and holding their hands over their ears, prepared for the gunshot-like report as potential energy became kinetic.
As stated earlier, these lines had been in rigorous use as dock lines and showed significant signs of weathering and UV degradation, as well as some physical abrasion associated with the on/off cycle loads that years of stress impose. It was easy to see where chafe damage had occurred, but what proved to be more insidious was the effect of UV degradation and weathering.
What We Found
Not unexpectedly, the spliced lines tended to fail at the end of the splice away from the loop where the tucked strand tails enter the line. The experts at New England Ropes indicated that the more tapered a splice, the better it resists failure. Even so, one should expect a 10-percent drop in line strength due to a splice and a 30-percent drop if a bowline is used in lieu of a splice. The unspliced rope ends faired better with most of the lines failing in the midsection, usually at abrasion points that had been marked during pre-test evaluation.
It was interesting to note that there was very little filament melting seen in the failure of these older lines. New nylon line, which tended to break at two to three times the load at which the older lines failed, showed extensive melting. At these higher loads, inter-filament pressure becomes so great that significant heat develops, enough to melt the filaments. Each of the older lines burst with a massive failure of filaments that was preceded by some preliminary popping sounds, signifying random filament destruction.
In two cases, the degree of destruction along the entire length of the rope indicated a structural consistency and was indicative of a complete failure, rather than a fuse-like break at a chafe-induced weak point or splice. One three-fourths-inch diameter, double-spliced line burst with a loud pop, separating as expected at the terminus of an eye splice, while at the other end of the line, the second splice hung by only a few remaining filaments, indicating once again a structural consistency one would hope to find in a uniformly engineered structure.
A Closer Look
Microscopic inspection revealed sheared strands and a small number of melted or heat-damaged filaments. One half-inch line was gold in color, and parted with a fluffy burst of filaments looking more like a seed pod than a dock line. In order to make sure the material was nylon, one of the lab techs took a sample and placed it in a crucible to which she added formic acid. The acid dissolved the gold, fluffy yarn, indicating with certainty its nylon pedigree. One couldn’t help but wonder how years of exposure in an environment prone to acid rain would impact the material.
Nylon arrives at cordage manufacturers as large spools of bundled extruded filaments. Each filament on the spool is a thin, continuous extrusion of nylon usually bundled in groups of about 20 filaments. These oversized spools are place on braiding machines that wind filaments together in a clockwise pattern into fibers, and these are spooled and put on another braiding machine to wind fibers in a counterclockwise direction into yarns. Continuing this twist and counter-twist process, the next step is to form these thicker bundles of yarn into strands that are finally twisted in the opposite direction into three-strand nylon rope.
The large machinery that does this work clacks and clatters with a uniform amount of tension and twist imparted to each bundle of nylon. The filaments are factory-coated with polymers that lubricate each fiber and reduce water absorption. The loss over time of this chemical coating is a key factor in a ropes deterioration. Its also interesting to note that wet nylon decreases in strength by as much as 15 percent, but its superior shock-absorbing characteristics (up to 25-percent elasticity) make it the preferred choice for dock lines, anchor rodes, and mooring lines.
The crew at New England Rope still favors three-strand nylon line for its toughness and ability to take physical abuse. Double-braided and plaited nylon dock lines are more susceptible to chafe and tearing caused by sharp objects. For the same reason, these alternatives to three-strand nylon do not fare well when used as anchor rode, especially when it makes contact with an underwater obstruction. Three-strand nylon is also easier to splice.
However, if space in an anchor well or line locker is limited, braided line compacts much better than three-strand. Tightly coiling an anchor rode to fit its locker is a recipe for hockles-twists in the line that will prevent it from paying out smoothly. You are better off stuffing a rode in a bag, or better yet, laying the line in a figure 8 configuration prior to stowing and make it fast with some small lines or sail ties.
Conclusion
Our test shows that even when you eliminate the effects of chafe, up to 75-percent of the original tensile strength in our sample ropes was lost. Although experts tell us that nylon has great ultra-violet damage resistance and chemical stability, our testing revealed a worrisome trend.
If you are basing your buying decisions on breaking strengths for new rope, you will obviously want to allow a generous safety factor for deterioration, or else plan to replace the rope soon. Keep in mind that the abysmal numbers seen in our testing actually optimized the cordages breaking strength because it was a straight line pull, did not include on/off cycle loading leading up to higher strains, and provided minimal chafe generating factors. Even so, the best showing was only 51 percent of the lines original tensile strength, and some samples of the dock lines broke at only 25 percent of the original rating!
These findings fly in the face of the conventional rhetoric that views nylon as such a strong material that one should always opt for thinner line due to its better elastic effect. To the contrary, within reason, this overly springy, rubberband-like function is a foe rather than a friend, and a couple of its downsides are significant. The first is that the heat build-up associated with repeatedly stretching the material gets critical as surge stretches the dock lines or gale-force gusts tension an anchor rode. The second is that the acceleration afforded by the springy dock lines actually encourages a vessel to “sail” at anchor or saw back and forth on its dock lines. Lastly, the smaller-diameter line has less sacrificial surface to lose in the chafe process, and damage to the line will jeopardize the vessel sooner rather than later.
Anti-chafe protection must allow rain to cool and lubricate the stretching and contracting fibers. Leather or water-permeable canvas are better than impervious PVC hose. Yes, wet nylon loses some strength, but the trade-off is minor in comparison to melting the filaments at the point of maximum strain.
We left the lab realizing the importance of taking a close look at dock lines and other nylon-line applications, noting the last time they had been replaced and why tropical storms and noreasters take such a heavy toll.
Check your boats nylon lines before the next storm season, and even if they look OK, consider our test results and decide how secure your boat will be with 25- to 50-percent of your lines original breaking strength remaining. Remember that we tested dry nylon lines and that wet nylon loses even more strength. These lab findings reminded us that a new set of dock lines is cheap insurance, and money well spent.
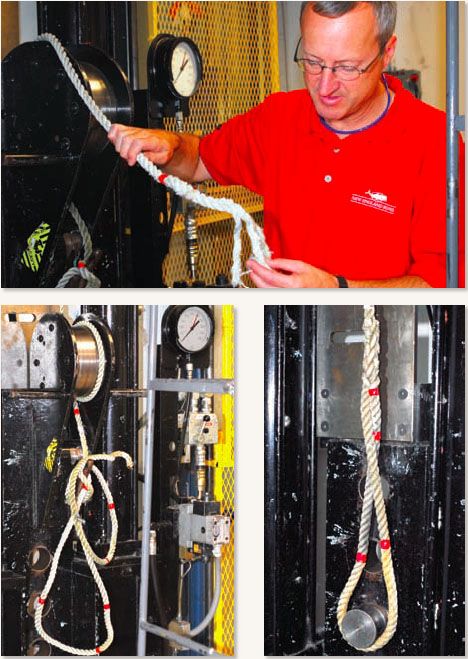
To evaluate the effect of sunlight and weather on nylon cordage, Practical Sailor, with the help of New England Ropes, tested several weathered 10- to 12-year-old dock lines to destruction. The New England Ropes testing lab contained a large, dual vertical-piston hydraulic ram with a jig arrangement that allowed a line to be positioned between two attachment points that moved apart at a slow and uniform rate. Because we had a variety of lines, some with spliced ends and others with free ends, we used two differing pieces of termination hardware. The free ends were given a single turn around a large winch like drum (right, below) and made fast to a conventional cleat. Through the use of the unit’s spacing adjustment, we were able to keep the chafed ends of each line out of the test. When securing a line with an eye splice, the drum and cleat fitting on the jig were replaced with a piece of hardware that allowed the spliced loop to be held on a smooth, cylinder-shaped attachment (far right).
A load cell linked to a computer tracked the strain imposed by the jig. The amount of elongation in the tested ropes prior to destruction was impressive, but it was still shorter than the 25-percent maximum elongation that new nylon cordage will exhibit prior to failure.
Nylon Dock Line Breaking Strength
SAMPLE NO. | SIZE | FAILUTE POINT TESTED LINE | BREAKING STRENGTH NEW LINE | PERCENTAGE* |
---|---|---|---|---|
1 | 1/2 inch | 1,893 pounds | 7,500 pounds | 0.25 |
2 | 1/2 inch | 1,892 pounds | 7,500 pounds | 0.25 |
3 | 5/8 inch | 3,493 pounds | 12,000 pounds | 0.28 |
4 | 5/8 inch | 6,105 pounds | 12,000 pounds | 0.51 |
5 | 3/4 inch | 5,861 pounds | 16,500 pounds | 0.36 |
6 | 3/4 inch | 6,288 pounds | 16,500 pounds | 0.38 |
7 | 3/4 inch | 5,678 pounds | 16,500 pounds | 0.34 |
*Percentage of original breaking strength remaining, as tested. |
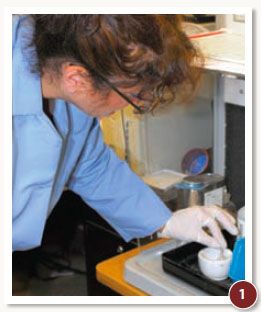
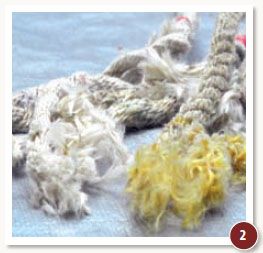
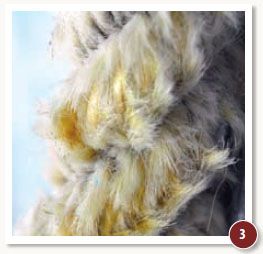
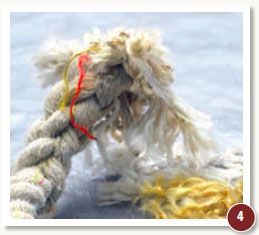
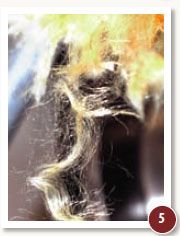
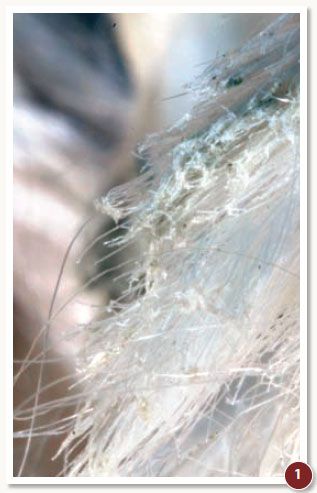
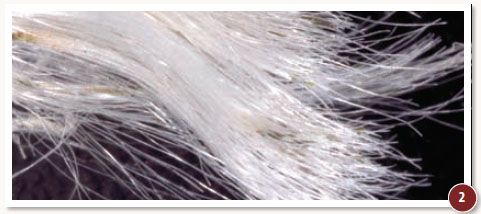
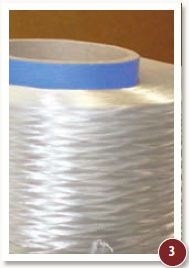
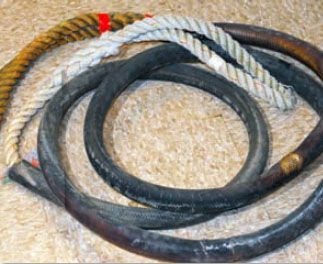
Anti-chafe efforts must be carefully considered. Prior studies have noted that many boats have broken mooring or dock lines that had been carefully covered with heavy PVC hose. It is presumed that despite the abrasion abatement afforded by such anti-chafe gear, it actually hastens the line’s demise by allowing inter-filament heat to build up more quickly. Rather than being abraded by the chock or rail, the line actually melts due to friction generated between the filaments as the rope is repeatedly tensioned.
Interestingly, the spliced rope, at left, did not fail where it was covered by plastic. This could be because the PVC provided some UV protection, but more likely this was because the failure points (at or near the splices) were local stress risers. In our view, PVC hose is not the ideal chafe gear. Traditional leather chafe guards with an open, laced top stitched to and around the line at key points of contact offer superior protection and allow heat to dissipate better than PVC.
This was a good one! although looking back I realized I seldom if ever keep primary lines to the age you were testing…good thing too!
Now alternatives….double braid poly used with fresh nylon “fuses”?
I’ll be there were some interesting ideas in circulation after this session!
ChrisCod
Interesting archival article. I believe I have read in a previous PS article that sailors tend to use too large a diameter nylon line for an anchor snubber. As such the line does not “stretch” enough thus reducing its effectiveness as a snubber on an all chain rode. Does this info suggest otherwise? Do I really want to swap my long used 1/2″ snubber for 3/8″ snubber in my 16,000 lb boat if the stretch shortens its life? Or do I just need to replace it more often? And how do I know when it’s time to replace it if I am looking for something other than chafe?
Thanks for reposting this article.
Thanks for the informative reprint. Curious what “ram” is.
For my 36 foot sailboat I used 20 feet of 1 inch nylon line from my mooring chain (8′ 1/2 inch of chain at the end of 20′ of 1 inch chain) that failed during a hurricane (the boat held on a backup line and was not damaged). The nylon line failed well below the chocks where chafe would occur. The line was over 5 years old, but still looked good and had never been through any severe weather before. I have to assume that 5 years exposure to the sun degraded the nylon?