As part of our investigation into anchor chain and its attachments (see PS January 2015 and June 2014 online), we examined new galvanizing processes. Steel products that have clearly undergone an unconventional galvanizing process are making their way into the recreational marine market, but because these methods are proprietary, getting specifics about them is difficult. Industry insiders tell us that the galvanizing process is evolving-but few details are made public.
For decades, the hot-dip galvanizing process has been straightforward: Steel is dipped into a hot, molten zinc bath and cooled, creating a sacrificial coating that protects the steel from corrosion. The process raises two problems: One, there is a wide variability in the effectiveness of this coating (see PS January 2015); and two, the process can’t be used on higher-tensile steels (above G70), because the high temperatures used to create the hot molten zinc bath are hotter than the tempering process used to strengthen the steel. In effect, the hot-dip galvanizing (and re-galvanizing) process weakens heat-treated steels by at least 10 percent, often much more.
The increased interest in high-tensile steel in the recreational marine market, the search for cheaper alternatives to hot-dip galvanizing, and concerns about the environmental impact of the conventional hot-dip process have prompted chain makers to explore new ways to galvanize chain. However, who is doing what remains a bit of a mystery.
Photos by Jonathon Neeves
What We Tested
Before we dig further into the world of galvanizing, here is a brief introduction to the companies whose products we evaluated.
Campbell: Campbell is one of two manufacturers of short-link (BBB) anchor chain in the U.S. (The other is Peerless.) Campbell chain has done well in past PS testing, and the company also makes high-tensile lifting components, such as galvanized bow shackles. It is part of the Apex Tool Group.
Distek/Armorgalv: New Jersey-based Distek is the licensor of the Armorgalv process, a relatively new process generally referred to as thermal diffusion galvanizing. They have licensees on every continent. There are a number of licensees in the U.S., including Spencer Industries. In Australia, there is a locally owned Armorgalv plant in Newcastle, New South Wales. Some licensors already produce Armorgalv chain products, though not all are suitable for anchor chain. (See Sherardizing Alternative, for more detail.)
Maggi: Maggi is an Italian manufacturer of both G40 and G70 anchor chain. A closely affiliated company called ZincOMet handles all its galvanizing needs.
Peerless: Peerless is one of the largest chain makers in the world and a major supplier of short-link anchor chain in America. Peerless has very recently introduced a metric range of short-link anchor chain and is marketing out of a center in Germany. Peerless also manufactures a range of other components, including high-tensile, galvanized, bow shackles.
PWB: PWB Anchor is an Australian chain maker, and it is a significant supplier to the Australian mining industry. PWB is represented in South Africa by SCAW Metals. PWB, also a supplier of steel industrial equipment, produces a G30 short-link anchor chain and a G50 chain on special demand.
Spencer Industries: Spencer is an engineering supplier with strong links to American defense industries. All the Armorgalv samples that we are testing, except that from PWB, came through Spencer Industries, although many, or all, are based on Peerless products.
Van Beest: This Dutch supplier of high-tensile lifting components sells shackles, swivels, hooks, and a range of other products. We tested some that had been treated with Armorgalv.
Thermal Diffusion Galvanizing
The wide range of galvanizing appearance (and performance) in our first round of testing in January 2015 was what inspired us to explore this topic further. For example, some of the Peerless chain we are testing is clearly different in appearance than normal hot-dipped galvanized chain, although Peerless makes no special claims about its process. Maggi describes the ZincOMet process used to galvanize its chain, but says little about what is special or different about its methods.
While chain makers are relatively tight-lipped about newer galvanizing processes, there are some published descriptions of alternatives to conventional galvanizing. One process is known as Galfan, which adds 5-percent aluminum to the zinc bath. Galfan claims better corrosion resistance in a marine environment. Although some European steel makers tout Galfans performance, to our knowledge, it is not being used in short-link chains commonly used for anchors.
While our search for Galfan anchor chain came up empty, we discovered examples of chain protected through thermal diffusion galvanizing (TDG, see Sherardizing Alternative). This process is being used commercially to coat various chain products, including anchor chain. The thermal diffusion galvanizing coating is commonly called Armorgalv, and the only known processors are licensed by Distek. Other major players in the chain industry are experimenting with variations of the Armorgalv process, and we expect to see some of these entering the market.
Armorgalv coating of chain is now a standard process, and it has been extended to other marine components such as swivels and shackles. At least one anchor maker has been testing it. Armorgalv chain can be found in the oil fields of Norway and on U.S. Navy ships in Alabama, but the process is still very new. Currently, Armorgalv-coated, short-link anchor chain is not available outside of Australia and New Zealand, where it is made by PWB Anchor. In business for nearly a half-century, PWBs reach extends to Southeast Asia, South Africa (represented by SCAW metals), and the Oceania region.
Armorgalv-treated products are about 5 percent more expensive than hot-dip galvanized products in Australia. We suspect there will be a higher markup in the U.S., because the most prominent U.S.-based manufacturers- Peerless and Campbell-normally do their own galvanizing and would have to subcontract the work.
In the U.S., Armorgalv-coated chain from Spencer Industries has found a range of applications-although anchor chain is not yet one of them. It is a preferred option for tying down heavy equipment on naval landing craft.
Campbell also has developed Armorgalv products, and testers have seen several Peerless-forged products-chain hooks, shackles, etc.-that have been treated with the Armorgalv process; however, as far as we can tell, none are sold under the Peerless name. Pewag USA, the U.S. branch of one of the worlds largest chain manufacturers, is also involved in supplying Armorgalv products to the U.S. military in cooperation with Spencer.
The big questions for the marine industry is whether the claims for Armorgalv are real, and do they offer us any advantage. To find out, we had to do a little testing.
How we tested
As in our most recent review of galvanized chain (see PS January 2015 online), we tested 3-foot samples to failure, or ultimate tensile stress. All samples were either 8 millimeter or 5/16-inch. All of our UTS testing was conducted at J.L. Robertson in Australia (www.lifting.com.au), a government-certified testing facility.
To test for abrasion, we took 12-inch lengths of every chain and suspended them from a galvanized piece of reinforcing bar under a moored catamaran, so that the chains were continually dragged over the seabed as the boat swung. We considered that this technique was close to the mechanism of abrasion of an anchor chain. As in the January 2015 comparison of galvanized coatings, the test again lasted for 70 days. Each piece of chain was weighed before and after, to 0.1-gram accuracy, to determine the amount of coating lost.
Our Armorgalv chain samples included 5/16-inch Peerless G80, 8-millimeter PWB Grade L (G30), and a 3/8-inch Peerless G43. We compared the PWB samples to PWBs hot-dip galvanizing Grade L, and compared the Peerless Armorgalv G80 (marked P8) to Campbells hot-dip galvanized G70. Keep in mind that the G80 is a heat-treated (quench and tempered), high-tensile alloy lifting chain, and as far as we are aware, has never been used as an anchor chain. The Campbell G70 is a quench-and-tempered product that uses similar steel to Campbells G43, but is strengthened through the heat-treatment processing. We also have a sample of 3/8-inch Peerless Armorgalv G43, as well as several samples of 8-millimeter G30 from PWB that were treated with various thicknesses of Armorgalv. Finally, we had some standard, hot-dip-galvanized samples from the first abrasion test and a length of uncoated, 8-millimeter G80.
For this test, we measured coating thickness using a standard coating-thickness meter. These meters measure the change in flux density at the surface of a magnetic probe as it nears a steel surface. Unable to get our hands on a flux meter for our first round of tests, we measured thickness with a micrometer (see PS January 2015 online). As it turned out, our micrometer readings were in line with the measurements using the thickness meter. This is good news for consumers. It means that if you do want to check the coating thickness on any chain sample, a micrometer and some basic math (described in the January 2015 report) will suffice.
What we found
Based on initial results from PSs abrasion tests, Armorgalv seems to be about twice as abrasion resistant as hot-dip galvanizing. After 30 days, all of the chains coated with hot-dip galvanizing showed about twice as much abrasion as the Armorgalv-treated chains. We had expected that some variability among chains that had undergone the same treatment would complicate our comparisons, but abrasion was surprising consistent by type: Hot-dipped galvanizing simply wore faster. Here are the abrasion levels by type, expressed as a grams: PWB Grade L (G30) hot-dip galvanizing, 2.6 grams; Campbell G70 hot-dip galvanizing, 2 grams; PWB Grade L (G30) Armorgalv, 1 gram; Peerless G80 (P8) Armorgalv, 0.8 grams.
Before we get too excited, a couple of issues need clarifying. First, the nature of hot-dipped galvanizing means it will wear faster at the beginning of its life. Second-and this is the key point-the Armorgalv coatings were all very thin to start with, so over the long haul, conventional galvanizing came out ahead.
Both hot-dip galvanizing and the Armorgalv coating are made up of iron/zinc alloy layers. Hot-dip galvanizing also contains an outer layer of pure zinc. This thin layer of pure zinc is soft and quickly abrades, but it adds a cosmetic shininess. As a result, hot-dip galvanizing will abrade more quickly than Armorgalv in the early stages of use, but the initial loss of pure zinc is not greatly significant.
Hot-dip galvanizing and Armorgalv coatings are harder and more abrasion resistant than the underlying steel. As long as the coating exists, the chains integrity is protected. The importance of this coating became clear when we looked at the uncoated G80 chain, which abraded 3 percent in just 70 days-two to three times faster than the coated chains.
For cruising sailors, this means that as soon as the coating is lost, the chain will begin to degrade much more rapidly. The pace of abrasion will more than double, eventually weakening the chain. This will be of particular concern to sailors who have downsized to a smaller-diameter, higher-tensile G43 chain, which has less meat than the larger-diameter G30 it replaced.
Rates of abrasion will vary with bottom environments, but in our view, anchor link diameters should be checked at least annually. Once the link diameter is reduced by 10 percent, the chain should be replaced. If regalvanizing is part of your game plan, this should be carried out before any of the unprotected chain has begun to erode.
When measuring for link abrasion, pay close attention to the areas about 30 to 60 feet from where the chain sweeps along the bottom and also where the chain dips below and above the water surface, where we frequently see corrosion starting in our chain tests.
Regarding hot-dip galvanizing, it was clear in our earlier test that thicker coatings generally lasted longer, although there were some anomalies-possibly due to the alloys used. The Armorgalv results showed the same pattern: Thicker coats lasted longer. Unfortunately, none of the Armorgalv-coated chains lasted as long as the best of the hot-dip galvanized chains; the Armorgalv was more abrasion resistant, but it was simply too thin.
Our best performing Armorgalv chain had a coating thickness of just 100 microns. The best hot-dip galvanizing coatings were about 150 microns thick, and some were over 200 microns. Distek claims that Armorgalv coatings up to 200 microns thick are possible, and this would almost certainly improve durability.
Although our long-term results with Armorgalv were disappointing, we think the method holds promise. The fact that the U.S. Navy has found Armorgalv-coated chain to be more corrosion resistant is encouraging. The possibility of Armorgalv coatings that are 200 microns thick also holds hope. Finally, Armorgalv does offer the opportunity to galvanize (and possibly re-galvanize) high-tensile chain, G70 and G80, without the inherent strength loss imposed by conventional hot-dip galvanizing.
We did some limited testing on the effect of Armorgalv on chain strength, but without a greater number of samples, ours should not be considered conclusive. We will be looking into this further as the technology progresses.
Out of curiosity, we examined some G80 omega links made in France by Van Beest and coated with Armorgalv. Compared to chain, the omega links are very close to precision-made items; the smallest component was a 2-by-5 millimeter pin with a recessed slot in the link to accept the pin. The coating was thorough and complete, indicating that intricate items do not present a special problem for thermal diffusion galvanizing.
These links were specifically treated to minimize strength degradation by coating at a lower temperature in a production run. The break strengths for these links were equal to the specified minimum. For us, this was further evidence that the thermal diffusion galvanizing process is kinder to high-tensile steels than high-temperature galvanizing.
A third plus for thermal diffusion galvanizing is its resistance to flaking. When we took a magnifying glass to the break surfaces of the Armorgalv samples, we saw no signs of coating flaking or peeling. This was not the case for some of our hot-dip galvanizing samples, which showed poor adhesion between the coating and the base metal after they had been tested to failure.
We discussed our findings with Distek, the licensors for the Armorgalv process, and they were frankly disappointed with the results. In examining photos of our testing, they suggested that the very black color of the coatings indicated sulfuric acid corrosion that is common in oxygen deficient (and polluted) environments. According to Armorgalv, acidic corrosion will be the same for a hot galvanized or thermal diffusion galvanized coating, and this was why our results were not as impressive as those in the U.S. Navy tests.
The black coloration of the samples might be a chemical effect from organic runoff from shoreside suburban properties, but this seems unlikely given the location of the test area, about 400 yards from a highly regulated swimming beach that is regularly monitored and supports a diverse range of marine life. Although anoxic conditions can exist in deep mud, this also seems unlikely in our test location, where the chains were exposed to the surface waters at all times. Moreover, the high levels of abrasion shown on the underlying metal, a composition that would be more resistant to acidic corrosion, point to abrasion-not chemicals-as the source of degradation. In our view, any black coloration was superficial. Regardless, Armorgalvs concerns about anoxic conditions suggest that if you primarily anchor in soft mud, you will want to keep a close eye on your galvanizing because the coating can come under a chemical attack.
Conclusion
We see no justification for the Armorgalv process for G30 and G40/43 short-link anchor chain. Our tests demonstrated that conventional hot-dip galvanizing appears at least be as good or better than Armorgalv. Short-term hot-dip galvanizing is proven and effective, but there is still room for improvement. Shortly after our tests, PWB withdrew, at least temporarily, its Armorgalv coated G30 chain from the market, presumably because the company is re-evaluating coating thickness.
In our view, chain makers should publish the minimum specified thicknesses for galvanized coatings on their chains for consumers. We would also like to see thicker and more consistent hot-dip galvanizing coatings, where possible.
The promise of thicker Armorgalv coatings is intriguing but not yet a reality. Where we do see immediate opportunity for thermal diffusion coating is in the coating of high-tensile chains, including G70, and high-tensile components, such as shackles, swivels, and connecting links.
Our top picks remain conventional hot-dip galvanizing made in America. We continue to question the use of G43 chain as we find G30 more than adequate in terms of safety; it also offers excellent durability and is cheaper than G43. G70 does offer some opportunity for weight saving, but this advantage is gained at considerable cost, as the chain will wear once the galvanized coating is lost, and being thinner, it will have a shorter life span and cannot be re-galvanized.
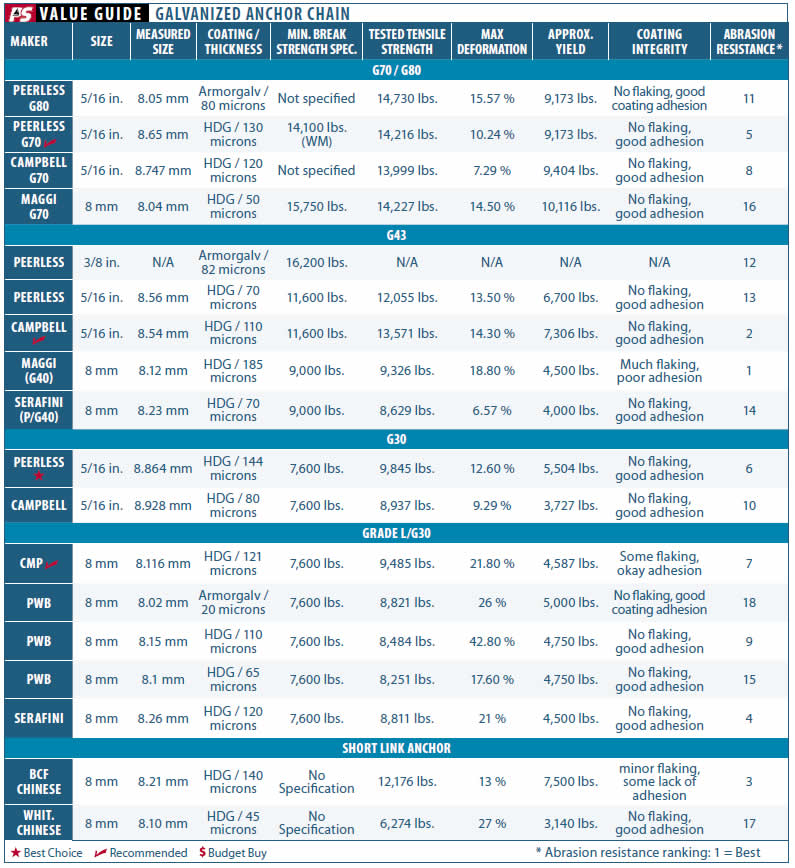
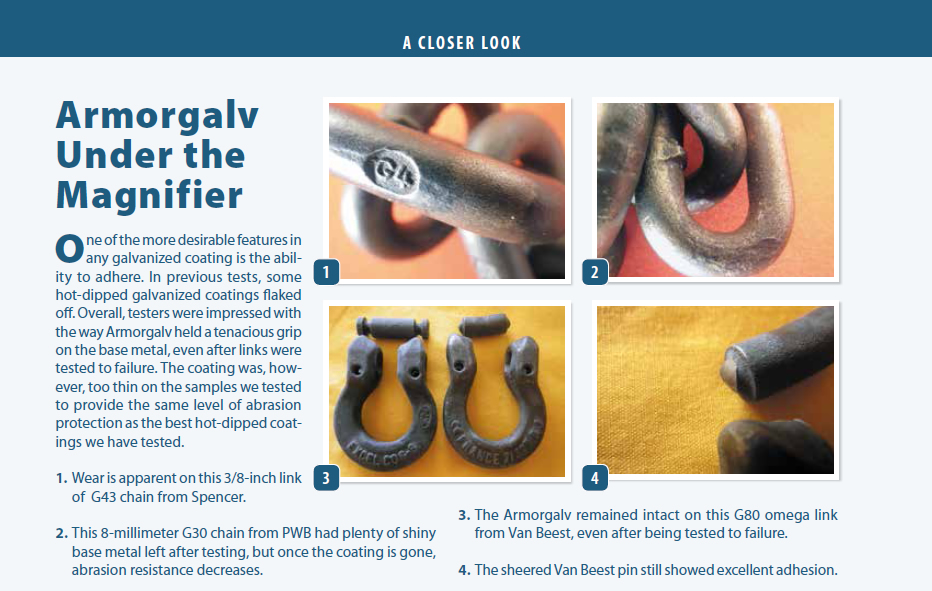
Hello,
I’m Mr.George Landry and I would like to place an order of some 2,000 feet of 6ft high 9 gauge galvanized chain link with no polls, only the wire. and will like you to go ahead and email me back with the price without shipping. What kind of credit card do you accept as payment?
Thank you.