Insulation is a greater energy-saving expedient; if our heater or air conditioner is undersized, fixing drafts, shading or insulating windows, and insulating non-cored laminate are all ways to reduce the thermal load. For boaters, however, that is only half of the equation.
In Florida, air conditioning ducts can fill with condensate and breed a horrible mildew soup. In Maryland, a cold drip from an uninsulated window can ruin a deep winter’s slumber. PS Tester Drew Frye likes to sail all winter, which drove him to investigate heat-savings options. Just two years ago, he installed air-conditioning on his PDQ catamaran, again taking advantage of the opportunity to various insulating materials and measure their effectiveness.
The effectiveness of insulation is commonly stated in terms of its R-value, defined as R=Delta T/Q, where Delta T is the difference in temperature between the inside and outside, and Q is the rate of heat flow through the wall.
A pane of glass that simply separates inside air from outside air earns a value of about R-1, the resistance to heat flow coming almost entirely from the thin boundary layer of air trapped near the surface by its own viscosity. Plastic materials do just a little better because they don’t conduct heat as well. Add a second layer of glass and the R values double and the heat flow is halved.
In general, when layers of insulating materials are stacked, R values are additive; stack two R-10 layers together and you get R-20. Place an R-2 curtain over an R-1 window and you get R-3. The amount of heat lost is inversely proportional to the R-value; the window that was previously losing 10 BTUs/hour at R-1, will lose only 3.3 BTU/hr at R-3.
There are limitations to this simple math. First, it does not relate directly to heat gain from the sun through radiation. That is why a reflective canvas cover will outperform double-glazing when it comes to keeping a boat cool, but it is less effective at repelling the winters chill. The R-factor calculation also underweights the difference in heat transfer rate between water (the bilge) and air (the topsides); 32 F water feels a lot colder than 32 F air.
In Winter Sailing Tips for Die-Hards, (Practical Sailor, December 2016) we touched on insulating windows, plugging drafts, and humidity control. Now we will drill down on some of the numbers and test some useful materials, both in the lab and in the field.
What We Tested
As a baseline, we tested acrylic and polycarbonate glazing materials, and solid and cored hulls. We then tested several add-on insulation approaches, including uninsulated window covers, bubble wrap, fiberglass, and several closed-cell foam materials. Using an R-value test rig and exposing sample materials to a temperature difference, we were able to compare insulating efficiency (see adjacent table). For more details on the test procedures, see the adjacent article, How We Tested on right.
Observations
Whether a surface sweats-a cold window in the winter or AC ducts in the summer-depends on if the surface is below the dew point. The dew point varies with both temperature and relative humidity. The adjacent chart illustrates the worst-case winter condition (68 F in the cabin, 55 percent relative humidity, 57 F dewpoint), and summer condition (78 F in the cabin, 64 percent relative humidity, 70 F dew point) on the test boat. In theory, any surface below the dew point will sweat, and this was very close to our experience; any surface that was below the dew point for significant time periods got wet and mildew bloomed. Needless to say, we corrected these problems with a combination of insulation and controlled ventilation.
Insulation must be sealed. If the outside or duct temperature is below the dew point, there will always be a location within the material that is at the dew point. Moisture will be drawn to that area. There are only two ways to avoid condensation within the insulation. In the case of fiberglass insulated AC ducts, the insulation has an air-tight jacket, and the jacket is sealed with duct tape and captured under clamps at each cut end. Alternatively, non-absorptive insulation such as closed-cell foam can be used, but it must be tightly bonded-not just taped-to the surface so that air cannot get under it.
Perhaps the most common failure to understand this is demonstrated by mildewed vinyl-covered foam ceiling liners. Installed over a non-cored hull, these are virtually guaranteed to sweat, even if deck fitting leaks don’t get them first. All of the benefits of insulation can be overwhelmed by the downside of mildew growth unless insulation is very carefully installed.
Curiously, the best way to prevent condensation in uninsulated spaces during winter is to let them go cold and restrict ventilation. The more warm dry air you pump into them in an effort to dry them, the more water you have made available to condense. Instead, only ventilate these spaces on the coldest, driest of days, when you can leave the boat (people add moisture) and let the heater and dehumidifier do their work. We have areas in the test boat that are well below the dew point (bilges), but they stay dry so long as we don’t try to air them out.
Air Conditioning Duct Insulation
One reason to insulate air conditioning ducts is to prevent heat loss in unconditioned spaces. It is common to lose as much as 15 percent of the available cooling capacity in a 10-foot run of uninsulated duct. Thus, ducts are generally insulated with about 1.5 inches (R-5) of fiberglass, protected from sweating by an air-tight jacket and carefully sealing the ends during installation. Metal and fiberglass ductwork is typically insulated with 1/8-inch self-adhesive closed-cell foam. The R-value is only about 1, but that is just enough to stop sweating. We have also insulated ducts with 1/2-inch closed cell foam wherever space allowed, further reducing cooling loss. The advantages of closed-cell foam are compactness and ease of fitting. However, it must be fully bonded to the duct with no air gaps. Large building ducts are often insulated on the inside; they don’t sweat on the inside, so corrosion and mildew risks are avoided.
Self Foam vs. Contact Cement
Self-adhesive seems faster at first glance, but it is not that simple. Often the backing was laborious to remove. The grab of the adhesive is also very aggressive and sheets cannot be shifted after the slightest contact without damage; always test-fit before removing the backing. Insulation makers often recommend a special type of glue (often rebranded with their name), but our testers found that common Weldwood contact cement made fitting easier because they could slide the sheets a little as needed if they positioned them while the adhesive was still damp. Applying contact cement in enclosed spaces means exposure to potentially harmful solvents, so ventilate and wear the appropriate respirator when installing (see Best Respirators for the Boatyard, PS September 2017). We recommend getting a mix; use self-adhesive for accessible areas and use contact cement in the tight spots.
Flexibility
The Armaflex/Aerocel products tested are soft and flexible, perfect for conforming to irregular surfaces. Stiffer foam can leave gaps where mildew can grow and may tend to pop away from the surface over time. Stiff foams may work in building and commercial duct insulation but are unacceptable for irregular surfaces such as boat hulls and small ductwork.
Covers and Storm Windows
All of the options were effective in stopping sweating, even uninsulated covers, although the amount of insulation varied. Windows are in well-ventilated areas, so anything that warmed the glazing even slightly was enough.
We originally thought bubble wrap sounded like a cardboard box living solution. However, after trying out standard bubble wrap(3/16 size bubbles) in several parts of the boat, we’ve found it to be a handy (and cheap) insulator, especially for windows. One advantage, it turns out, is that you don’t need to tape it in place in many applications. To apply bubble wrap to a window, simply cut the bubble wrap a fraction of an inch smaller than the window, mist the window with plain water (distilled if available), and press the wrap in place. Miraculously, it sticks and sticks with enough tenacity to stay in place for a season if you don’t rub against it. A combination of static and surface energy is enough to form a weak bond, like cling wrap. At the end of the season, they can either be pitched or peeled off and stored for the next year; they last at least a few seasons.
What about other surfaces? We tried bubble wrap on latex paint, glass, Lexan, and smooth but unfinished FRP. Under the influence of gravity, it peeled away from painted wood and raw fiberglass with a few weeks but stayed in place for the entire season on glass, Lexan and acrylic, including two locations where light curtains brushed across it every few days (a sliding glass door and boat windows. The R-value is low, only about 1.2, but for single glazed windows that cuts the heat loss in half.
Hull Insulation
For bilges, the best wintertime bet is to keep a dry bilge and then cover the floors with carpet as insulation. Any water that is in the bilge will be very cold and as a result, will liberate very little vapor in the winter. Insulating below the waterline can interfere with maintenance and inspection, and even the best-bonded type can trap diesel and moisture. Nonetheless, we did much of our testing in the bilge because the test boat is cored above the waterline and the bilge provides consistently near-freezing temperatures in the Chesapeake region for the entire winter.
Do not attempt to install hull insulation in cold weather. The hull will be sweating, if only slightly, and since the effect is instantaneous, no amount of drying or blowing with fans will eliminate it. The tape and glue will not stick properly.
The cored portions of the hull never sweat; the combined 5-6 R-value of the laminate is enough. Although it worked on air conditioning ducts, 1/8-inch neoprene foam was not enough to raise the surface temperature of non-cored sections above the dew point and they sweated. The 1/2-inch closed cell foam prevented sweating in all cases, although the surface temperature was right at the dew point. Thus, we recommend 1/2-inch or thicker for liveaboards in very cold climates.
Mildew under the insulation depended on sealing. Tightly bonded insulation proved mildew-proof. Samples that were carefully taped in place varied in performance, not due to the insulation type but rather because air got behind it.
The problem with taping the insulation in place is that even with good quality duct tape (Gorilla brand) the adhesive area will stay wet and eventually fail in spots.
Ducts
Masterflow 4-inch Insulated Duct
With an aluminized mylar jacket and mylar tube, this is a common air conditioning duct insulation. Although we know many stories of sodden AC ductwork, invariably they are linked to poor installation practices. Given the fitting problems in tight spaces, no other materials seem practical.
Bottom line: Simple to install, effective and without any real competition, this is Recommended.
Hull
Armaflex Armacel and Aerocel AP
The workhorse insulation product for boats, these did everything right. The self-adhesive versions (AC) grabs permanently; even in damp locations it will never let go. In tight spaces we recommend using contact cement and installing the pieces before the glue quite dries. Armaflex 520 contact adhesive (like contact cement) is recommended for use with Aerocel products. We tested the 1/2-inch Armacel and the 3/4-inch Aerocel AP. Based on our testing the latter may be a better choice for liveaboards in very cold climates.
Bottom line: This is the Best Choice for easy installation.
Armaflex TP 18230
We installed 1/2-inch insulation where it could fit, but some spaces were too tight so we downsized to this 1/8-inch thick tape. The tape bonds powerfully and is easy to work around curves and in tight gaps. It also serves as a sort of duct tape for use with thicker Armacel products.
Bottom line: Recommended where space is tight.
Windows
Optix Acrylic glazing
Available at any hardware store, these acrylic glazing panels are simple to install. You just trace the bug screens and replace them. It doesn’t do anything to keep the sun out in the summer-covers are better for that-but they make a huge difference in the winter.
Bottom Line: Recommended for cold-climate boats.
Sunbrella Acrylic canvas
We use uninsulated covers primarily the protect our hatches from UV damage, but they also add some insulation. If we lived aboard in a cold climate we would either make an insulated set or simply slide a foam sheet under them. In summer they substantially reduce the air conditioning load. They make the boat rather dark in the winter, but on the upside, they reduce window cleaning.
Bottom line: Recommended for UV protection alone.
Generic bubble wrap
Because it functions only by creating an air gap, the insulation effectiveness is about the same as adding a second pane of glazing. The corollary is that the thickness has very little effect on insulating ability; since the smaller, 3/16 bubble wrap clings better and is easier to work with, that is what we recommend.
Bottom Line: Although bubble wrap is hardly a permanent fix, it can offer some temporary solution if you find yourself running behind in your autumn passage south.
Conclusions
All of the window insulation strategies were condensation-free. If a few drops appeared, while cooking, for example, they evaporated quickly. We like interior double glazing in the form of bug screen replacements when possible, but prefer external covers in the summer because they excel at reflecting.
Air conditioning ducts can be insulted with fiberglass but it must be properly sealed. Bonded closed-cell foam is another cheap option. The Areoflex and Armacel products designed for this purpose proved easy to install and effective, worth the extra expense in our opinion.
The best hull insulation is a core above the waterline. Although they can suffer from delamination if poorly constructed or maintained, there is no question that they are warmer in the winter, cooler in the summer, and more resistant to condensation mildew.
For hull insulation, we can only recommend closed-cell foam that is tightly bonded to the surface, whether self-adhesive or using contact cement. On cored hulls, it probably isn’t worth the effort unless you are a cold-climate live-aboard. For non-cored hulls, a good installation should result in a warmer boat (or cooler) and reduced condensation.
We would skip the bilge areas for fiberglass boats unless condensation is a serious problem. Metal boats can certainly benefit from insulation, but the risk of corrosion puts this topic beyond the scope of this article.
We’ve seen a lot of failures of taped-on insulation, polystyrene insulation that was spot-glued as you would do in a house, and ceiling liners that should have been sealed and turned into mold farms. Use the correct material and seal everything.
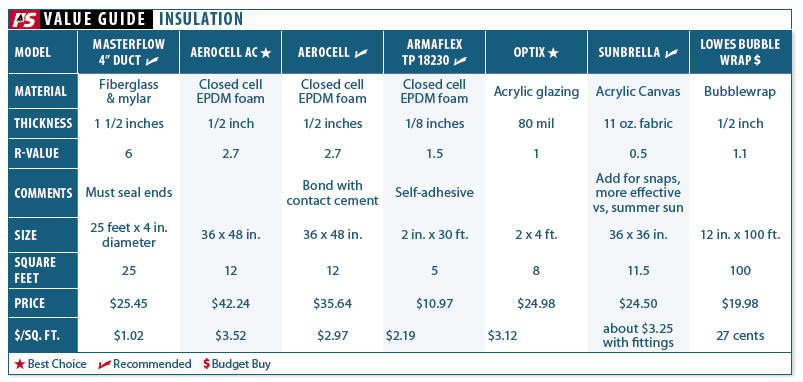
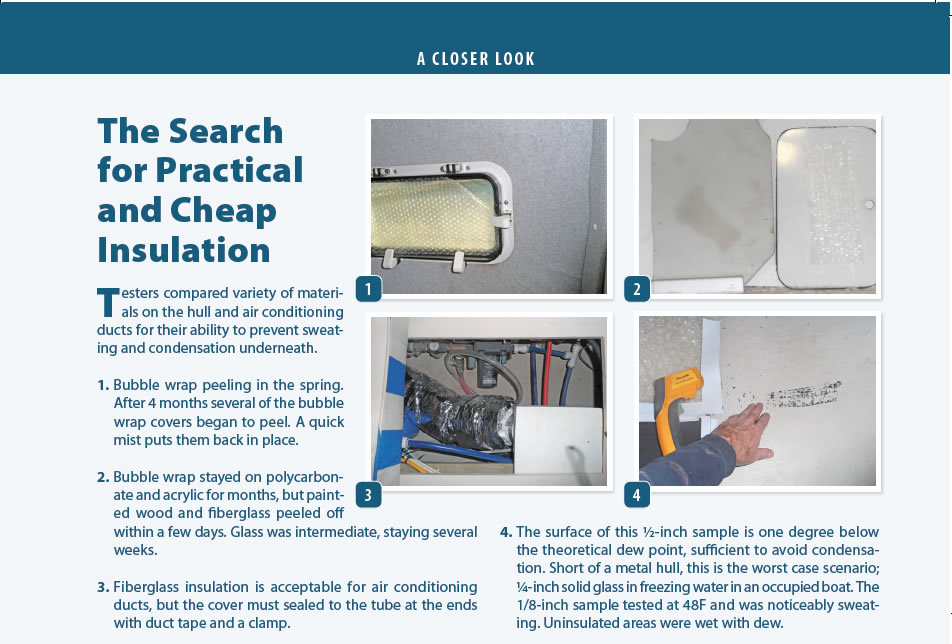
Testers compared variety of materials on the hull and air conditioning ducts for their ability to prevent sweating and condensation underneath.
- Bubble wrap peeling in the spring. After 4 months several of the bubble wrap covers began to peel. A quick mist puts them back in place.
- Bubble wrap stayed on polycarbonate and acrylic for months, but painted wood and fiberglass peeled off within a few days. Glass was intermediate, staying several weeks.
- Fiberglass insulation is acceptable for air conditioning ducts, but the cover must sealed to the tube at the ends with duct tape and a clamp.
- The surface of this ½-inch sample is one degree below the theoretical dew point, sufficient to avoid condensation. Short of a metal hull, this is the worst-case scenario; ¼-inch solid glass in freezing water in an occupied boat. The 1/8-inch sample tested at 48F and was noticeably sweating. Uninsulated areas were wet with dew.
Hello,
We have a 60′ Steel sail yacht, which is completely foam sprayed insulated.
My question is how to stop condensation on the steel frames of our ports only,(23)
Is there perhaps a paint or epoxy available/ out there….
We have some ventilation, and an oil heater on low most of the winter months.(Vancouver Canada.)
I have decided to add AP Armaflex FS SA to the boat but am finding it impossible to find for sale. Where can one actually buy these products?
Wondering the same. Did you find a source?
Very informative!
One issue- I’m reading this article on an apple phone. For some reason, in several locations an expected measurement was represented as a hyphen! ( – ) This is unchanged when I sign in on a Windoze laptop.
Proofread before Publish! First by author & 2nd by a careful reviewer.
We use cheap automotive dash sun shades and cut them to fit inside our ports. We did this ten years ago when we had to leave the boat over the summer in the desert and have never removed them. They reflect the light as well as add some insulation. they do however make it dark below. I would be interested to see how our approach compares to bubble wrap.
We have just been made aware of and purchased a desiccant dehumidifier for live aboard use in a cold damp climate. This type of dehumidifier adds heat to the space along with removing gallons of water each day. If you goal is humidity removal only, then a compressor dehumidifier is best. If you need heat along with water removal, desiccant units are superb!
Compressor units remove water by chilling the air. Desiccant units remove water by desiccation and the desiccant is regenerated using heat. Desiccant units produce warm air as a byproduct of dehumidification.
This unit has literally changed our live aboard life.
Garage door insulation (bubble wrap sandwiched with reflective foil) Is inexpensive, easy to cut to fit nicely in ports, thin and solid enough to slide under a zippered headliner. It is also very light weight with good R value. You can also use tape along a top edge to make an opening flap to block drafts behind canvas access cover in V berth and transoms.
That’s an interesting article – never considered wrapping my heating ducts as I like that they heat the inner lockers behind the cabinetry.
I’ve lived aboard many years in cold climes – the best thing we found for ports to stop sweating was cellophane wrap on 2 sided tape. We’ve done it to the outside and the inside but prefer the outside stuck to the gelcoat, as it’s easier to clean in the spring.
I’ve used mylar coated bubble wrap always – it has a R9+ value, sticks in place with 3M adhesive spray. Cheap and very effective. On my Morgan 382, I lined the entire cabin roof/under deck – it provided amazing reflectivity in the summer heat and vice-versa, keeping the heat reflected back into the vessel.
Anyone have source to purchase Armaflex?