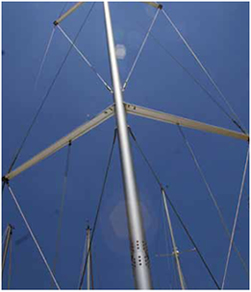
251
The Hunter 33 is built in Alachua, Fla., using high-quality resins and laminates and conventional open molding hand-laminating processes.
Hull: Hull construction begins with a blister-resistant ISO NPG gelcoat sprayed into the female mold, followed by chopped strand mat and, hand-laid with vinylester resin. The rest of the hull is laid up using a modified epoxy resin. The hull is solid below the waterline with Kevlar in the bow for added impact resistance. Above the waterline is a sandwich construction using half-inch balsa-core. Extra reinforcing laminate wraps around the hull at the chainplates, spreading the load. Use of 2-mil e-glass core mat helps combat print-through.
Interior and grid: Hunter uses computer-guided tools to precisely cut parts for the interior. All components, such as the galley unit and the head units, are put together as sub-assemblies, and then bonded to a stout fiberglass grid to form the interior module. After the interior has been built on the grid, the grid and interior are lowered into the hull and the grid is chemically bonded to the hull using Plexus. Structural bulkheads are tabbed to the hull and deck creating 360 degrees of structural support.
Deck: Sandwich construction with marine plywood coring. The marine ply is cut into small squares to prevent any moisture penetration from wicking. Where hardware is mounted, the plywood is replaced by aluminum plates. Hardware is tapped into aluminum plates and through-bolted.
Hull-to-deck joint: Hull and deck are attached using an outward facing flange that is chemically bonded with 3M’s 5200 and then through-bolted with stainless hardware all the way around. A heavy, synthetic rubber rail with a stainless steel insert fits over the joint.
Keel and rudder: The standard keel is iron (lead is $9,800 option) with multiple layers of epoxy barrier coat. The rudderstock stern tube is adhered to the hull with a primary bond and reinforced around the base. The rudder stock is solid Aquamet 22, a high-alloy austenitic stainless-steel solid stainless steel. The rudder is composite construction using fiberglass skins, a stainless-steel skeletal structure, and adhesive foam. It is attached to a stainless-steel stock.
Rig: The Hunter rig is a two-part, deck-stepped mast made by Seldén. Construction varies according to rig type—in-mast furling or standard. The in-mast furling mast is taller and a heavier-gauge aluminum, so adds more weight aloft. Both 33 versions use a B&R rig with spreaders swept back and Dyform wire with swaged studs connected aloft with stemball fittings.
The Hunter 33 is built in Alachua, Fla., using high-quality resins and laminates and conventional open molding hand-laminating processes.
Hull: Hull construction begins with a blister-resistant ISO NPG gelcoat sprayed into the female mold, followed by chopped strand mat and, hand-laid with vinylester resin. The rest of the hull is laid up using a modified epoxy resin. The hull is solid below the waterline with Kevlar in the bow for added impact resistance. Above the waterline is a sandwich construction using half-inch balsa-core. Extra reinforcing laminate wraps around the hull at the chainplates, spreading the load. Use of 2-mil e-glass core mat helps combat print-through.
Interior and grid: Hunter uses computer-guided tools to precisely cut parts for the interior. All components, such as the galley unit and the head units, are put together as sub-assemblies, and then bonded to a stout fiberglass grid to form the interior module. After the interior has been built on the grid, the grid and interior are lowered into the hull and the grid is chemically bonded to the hull using Plexus. Structural bulkheads are tabbed to the hull and deck creating 360 degrees of structural support.
Deck: Sandwich construction with marine plywood coring. The marine ply is cut into small squares to prevent any moisture penetration from wicking. Where hardware is mounted, the plywood is replaced by aluminum plates. Hardware is tapped into aluminum plates and through-bolted.
Hull-to-deck joint: Hull and deck are attached using an outward facing flange that is chemically bonded with 3M’s 5200 and then through-bolted with stainless hardware all the way around. A heavy, synthetic rubber rail with a stainless steel insert fits over the joint.
Keel and rudder: The standard keel is iron (lead is $9,800 option) with multiple layers of epoxy barrier coat. The rudderstock stern tube is adhered to the hull with a primary bond and reinforced around the base. The rudder stock is solid Aquamet 22, a high-alloy austenitic stainless-steel solid stainless steel. The rudder is composite construction using fiberglass skins, a stainless-steel skeletal structure, and adhesive foam. It is attached to a stainless-steel stock.
Rig: The Hunter rig is a two-part, deck-stepped mast made by Seldén. Construction varies according to rig type—in-mast furling or standard. The in-mast furling mast is taller and a heavier-gauge aluminum, so adds more weight aloft. Both 33 versions use a B&R rig with spreaders swept back and Dyform wire with swaged studs connected aloft with stemball fittings.