Putties and caulks originated as tar and tree sap, and probably were first used by Neolithic boatbuilders trying to keep water on the outside of a crudely planked hull.
Today, hulls are tighter, but theres still a need to seal various joints, seams, and fastened hardware. The job now is done with a wide range of improved sealants and adhesives that offer less shrinkage, better elongation characteristics, long-term structural stability, and resistance to chemical deterioration. The majority of these hydrophobic marine gap-fillers tends to fall into four generic chemical categories-silicone, polysulfide, polyurethane, and polyether sealant/adhesives.
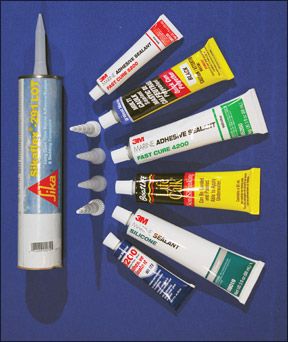
For decades, bedding compounds such as Dolfinite were industry favorites and were put into service between two mechanically fastened surfaces. They had no adhesive quality and remained soft and pliable until time, heat, and weathering left them dry and brittle. Modern alternatives go a big step further, melding an adhesive quality with a flexible gap-filling ability that improves the materials watertight integrity.
This article will look at seven of the most popular products on chandlery shelves that perform the dual role of bonding agent and bedding compound.
What We Tested
Practical Sailor
Silicone sealants are inorganic polymers that contain silicon. They are inert, non-conductive, UV-tolerant compounds that fit the bill as effective gap-filling sealants and are moderately effective as adhesives.
Silicone sealers in the consumer market use acetic acid as a reaction agent rather than hydrogen chloride. This makes them more user-friendly as they are non-toxic and have an extended working time. Prior to skinning over, silicone is a toothpaste-like gel that transforms into a flexible solid over a 24-hour period. Paint will not adhere to cured silicone, and care should be taken not to contaminate surfaces that are destined to be refinished.
Polysulfides are polymers that comprise alternating chains of sulfur and hydrocarbons. This gives them a natural Gumby-ish quality when theyre cured, as they return to their natural shape after being tensioned. Polysulfides have good adhesive quality and can be recognized by their distinct egg-like odor. For decades, they remained the seam-sealers of choice when it came to caulking teak decks.
The chemical company Thiokol, a key player in the aerospace industry, actually chose its name based upon the combination of the Greek words for “sulfur” and “glue.” Thiokols epoxy-modified two-part polysulfide sealers were a favorite among boatbuilders and repairers. Today, single-part polysulfide sealers remain a popular gap-filling compound with a good blend of adhesive quality and weathering resistance.
Polyurethane sealants and adhesives have grown in popularity and are preferred by boatbuilders for projects like sealing hull-to-deck joints and installing through-hulls. The long-chain molecules that crosslink in the curing process include isocyanate resin that reacts with moisture to form a flexible solid.
These highly adhesive polymers offer both excellent surface grip and desirable gap-filling characteristics. There are numerous formulations that lead to products with different cure rates, elongation characteristics, and tensile strength.
Polyether-based caulks are the newest genre of ultra flexible gap-filling adhesive/sealants, and their cure is dramatically accelerated by a more reactive methyl silyl-enhanced reaction with water vapor that causes polyether products to skin cure faster than silicone and deep cure much quicker than polyurethanes. Their lack of solvents eliminates odor and minimizes shrinkage-based skin stress. They have very favorable stretch capacity and good resistance to ultraviolet rays and weathering.
Background
Practical Sailor
The adhesive quality of polyurethane caulks is superior, and they also remain flexible enough to handle the elongation differentials associated with wood, metal, fiberglass, and other mixed-material junctions. The new addition of polyether products to the fray may challenge polyurethanes stronghold.
Cohesive failure is defined as the inability of an adhesive to resist internal separation; it separates from itself. During cohesive failure, the adhesive sticks to both substrates, but cannot hold them together.
The products in this evaluation were all tested to failure, and testers noted the type of failure each showed. Find out how we pushed the products to their break-in points in “How We Tested.”
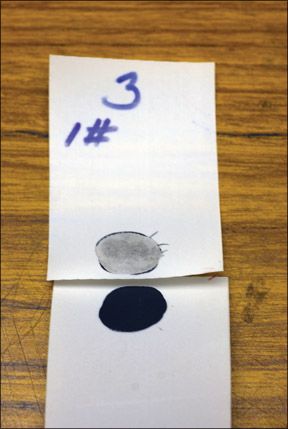
3M 5200 Fast Cure
This modification of 3Ms signature high-strength polyurethane adhesive dries in 24 hours and can be used for hardware bedding, hull-to-deck joints or through-hull fittings.
The manufacturer suggests that the impressive adhesive quality of traditional 5200 is retained in the fast-cure version, but our testing indicated that the sample we purchased in a local chandlery did not meet this claim. The Fast 5200 did top the scale as an adhesive attaching wood to fiberglass, but its adhesive quality in FRP-to-FRP joints left much to be desired. The same lower-than-anticipated results surfaced during the tension test of a metal to wood bond, and the shear-strength testing of Dacron sailcloth.
The manufacturer says that the material can be softened by some teak cleaners and solvents, and is best not used as a paying compound for teak decks.
Bottom line: Tapped as one of the best adhesives, above and below the waterline, in the 1998 test, 3Ms 5200 Fast Cure left us with more questions than answers in regards to its adhesive shortfalls, especially on FRP to FRP joints. However, we do recommend it for wood to fiberglass joints, as it out-performed all others in this area.
3M 4200 Fast Cure
This polyurethane adhesive/sealant is billed as a less tenacious version of fast-cure 5200, and yet in our testing, it outshined its big brother in all but its ability to bond fiberglass to wood. It cures in 24 hours and can be used above and below the waterline.
One of the big surprises of the test was how tight a grip 4200 had when it came to shear testing the FRP coupons. It out-performed all but the Sikaflex 291 LOT (also a modified polyurethane sealant/adhesive). The 4200 also showed good adhesion to metal and sailcloth.
Bottom line: Near across-the-board excellence makes 4200 Fast Cure a useful product to carry on board.
West Marine 8200
A fast-curing polyurethane adhesive/sealant, West Marines 8200 is suitable for use above and below the waterline. It adheres to glass and metal and resists UV degradation. The 8200 attained earned high scores as a versatile moisture-resistant adhesive.
Packaged in small, fluid-ounce tubes, 8200s fast-cure moisture-accelerated chemistry results in opened tubes hardening quickly. Star brite, which manufactures 8200 for West Marine, recommends using the contents within 24 hours after opening. However, the single-use tubes are convenient to stow in a toolbag and erase the worry of paying more for a larger-volume tube or cartridge, only to have it turn solid before its used up.
Bottom line: The versatility of this adhesive makes it a good addition to toolkits and paint lockers.
Sikaflex 291 LOT
Sikaflex 291s “LOT” designation stands for a “long open time,” an indicator that this version of Sikas polyurethane sealant is slow to skin over and slightly more flexible than the regular, faster-curing 291. This is a well-balanced medium modulus adhesive/sealant that can be used above and below the waterline, and it turned out to be a strong performer in our testing, scoring high on all but the Dacron-to-Dacron fabric adhesion test.
In addition to delivering impressive adhesion numbers, the slow-curing 291 was easy to handle and was thixotropic enough not to sag but viscous enough to be smoothed, wiped, and spread evenly.
Bottom line: Recommended for applications where a slow-cure sealant is needed such as fastening a toerail or rubstrake, or when working in hot, humid conditions. Sikaflex slow-cure also is less likely to harden in the tube between work sessions.
3M Silicone
The 3M Silicone is a high-quality, non-conductive, gap-filling adhesive/sealant for use above the waterline. It skins over in five to 10 minutes and cures in 24 hours. Its adhesive ability on fiberglass-to-metal bonds proved better than we expected. In fact, our testers found that silicones easy to use, quick-dry chemistry make it a good choice for quick fixes or more lasting repairs where maximum adhesive strength is not an absolute necessity.

3M bills its Silicone sealant as a low-strength, easily removable sealant, testers found its shear and tensile strength good on fiberglass and capable of providing a flexible gasket-like seal between two mechanically fastened parts.
Bottom line: When gap-filling is more important than ultimate adhesive strength, 3M silicone is a good option. It can help keep water off electrical connections, and its non-toxic nature makes it a good choice around sinks and countertops.
BoatLife
BoatLifes Life-Caulk is a Thiokol synthetic-rubber compound that adheres to wood, fiberglass, and metal. When cured, it provides a desirable blend of flexibility and adhesive strength. A full cure requires seven to 10 days, depending upon the temperature and humidity. Moisture actually accelerates the curing process. When using it on oily wood like teak, its recommended to apply Life-Caulk Primer first for improved adhesion.
Life-Caulks relatively poor results in our adhesion tests was a disappointment, but it showed good elongation and cohesiveness, making it a durable bedding compound when mechanically held between two fastened surfaces. We plan to re-test it using the primer for a follow-up evaluation.
Bottom line: Life-Caulk is worth considering for paying deck seams, but our top pick is still Teakdecking Systems caulk, the Best Choice in our 2008 test.
West Marine Multi-Caulk
Polyether sealants were developed for the building trades, but their good adhesive quality and excellent elongation characteristics led several companies to market marine versions.
In the tension test, West Marines Polyether Multi-Caulk grabbed onto the metal bolthead like a vice. It also aced our warm-water submersion test, but it fell short in our wood-to-FRP adhesion test and the emergency sail repair simulation.
Made by Star brite for West Marine, this fast-curing polyether product gets a cure boost from moisture. It has much to offer in applications that involve metal and FRP sealing, high flex and expansion rates, plus lots of moisture. It was the standout performer in our “wet test,” and its reluctance to release its grip on the Starboard surface resulted in a shearing of the sealant bead rather than the material peeling from the surface.
Bottom line: We liked Multi-Caulks fast cure and the bond it developed on stainless steel as well as its ability to stay stuck on Starboard.
Conclusion
In this round of testing, no one product met our every adhesive need, so weve tapped a few recommended products for specific applications. For example, as much as we liked West Marines fast curing 8200, 3Ms versatile 4200 (fast), and longer open time Sikaflex 291 LOT-all of which are polyurethane products-we recognized their shortcomings. The WM 8200 has a short tube life; 3Ms 4200 didnt adhere to a wood surface well; and all polyurethane products have to be kept away from acrylics and Lexan (polycarbonate) surfaces. Otherwise, the 8200, 4200, and Sikaflex 291 LOT are good choices for sealing jobs where adhesion counts-like bedding a through-hull. The 8200, 4200, and Sikaflex all get PSs recommendation.
For projects that involve bedding stainless deck hardware like a stanchion base, wed use the Sikaflex, but if the hardware is aluminum, any of the three recommended products would work.
Silicone, which wont harm most plastics, can be used to re-bed plastic hatch and port lenses. In this test field, 3Ms Silicone stands out as the choice for these projects.
A polysulfide compound such as Life-Caulk remains a good option for filling teak deck seams, but the 2008 top pick Teakdecking Systems caulk is a bit less expensive.
We were disappointed with the FRP-metal adhesion of the fast-cure 3M 5200, but its wood to fiberglass bonds were impressive. For jobs like bedding a teak handrail to a cabintop, wed use the 5200 or Sikaflex 291 LOT.
Very useful infor. Still uncertain what is the best goo to seal teak toerail to the gelcoated fiberglass deck joint? There is no load obviously, but it must stick very well to both materials.
Thanks
I think 3M marine adhesive sealant is a good product. If you want a fast-curing yet permanently-bonding marine sealant, then this product from 3M will never disappoint.
I would like to see how 3M 4000UV compares. I used it to re-bed all our deck hardware and after 14 years, not a single fitting as leaked a single drop. The boat has remained uncovered year round on a lake near Atlanta, GA. It’s UV resistant and it is not too difficult to separate if needed.