As more and more anchor-makers source their materials and move their fabricating offshore, Practical Sailor has been fielding an increasing number of questions regarding anchor quality. Is the tensile-strength steel used to fabricate anchors consistent with the application? Is it consistent with how the anchor is being represented in marketing materials?
At the heart of this discussion is shank strength. There seems little point in having a high holding-capacity anchor if the shank isn’t strong enough to cope with these projected loads. Why isn’t shank strength getting much attention? Is anyone actually measuring this? And how much does it matter?

Photos by Jonathan Neeves
In fact, various classification societies-Lloyds Register (LR), American Bureau of Shipping (ABS), and others-have been evaluating shank strength for decades. They call it proof testing, and currently it is the only measure we have of shank strength. A number of anchors, the ones we use on recreational sailboats, have been tested, type-approved, and classified by the classification society (CS) members. Among those that have gone through this testing process are Lewmars CQR and Delta, Fortress anchors, Wasis Bugel anchor (made in Germany), the Quickline Ultra, and most anchors from Manson Anchors. One reason these anchors are CS tested is that certain vessels in survey-typically commercial vessels that must meet insurance requirements-are required to carry individually CS-certified anchors. Large commercial vessels carry individually certified anchors, and it is the commercial marine sector that shapes the focus of the classification work with anchors. Leisure market anchors are, for the most part, unregulated.
The certification process is divided into two parts. First, the basic design is type approved. Once it gains type approval, individual anchors made to that design might then be individually tested.
Before awarding type approval, the classification society must review and accept design drawings, the method of manufacture and raw material (as described on paper), independent holding-capacity tests (similar to those Practical Sailor has conducted in the past) and proof testing. Proof testing loads the shank of the anchor with the fluke held immobile. Basically, this exerts both tension and a lever-arm load to the shank, therefore testing the hinge or weld junction between the shank and fluke, and making some attempt to assess whether the shank might bend under normal, straight-line anchoring loads-in the direction the anchor is set. The test also confirms that the fluke is strong enough to sustain the stated loads.
Proof testing is not conducted to destruction. Tables of proof-test loads are published, but these loads are not particularly extreme. For example, a 50-kilogram (110-pound) Manson Supreme (rated as a super-high holding-power anchor by Lloyds) would be tested under a proof load of 3,987 kilograms (8,790 pounds), yet even a 15-kilogram Supreme could reasonably have a holding capacity in excess of 2,000 kilograms. Some anchor makers arrange and publish their own proof-testing results, and these tests are sometimes conducted to considerably higher loads than demanded by the classification societies.

unless otherwise noted
The CS, under their corporate rules (from the International Association of Classification Societies, IACS) produce guidelines for anchor testing. The preamble for testing states: The anchor equipment . . . is intended for temporary mooring of a vessel within a harbor or sheltered area when the vessel is awaiting berth, tide, etc. The equipment is therefore not designed to hold a ship off fully exposed coasts in rough weather . . .
In the leisure sector of the market, we expect our anchors to withstand whatever-well almost-whereas the anchors for commercial vessels are tested only to hold the vessel in benign conditions. In fact, in some ports, ships are ordered offshore in winds greater than 25 knots.
Leisure anchors by Fortress, Delta, Manson Supreme, and others are tested by the CS in exactly the same way as a large commercial anchor, by exactly the same procedures. However, one look at common large commercial anchors indicates some fundamental differences. Many commercial anchors have shank cross-sections with width-to-depth ratios of roughly 1:1. In other words, the cross-section is roughly square. Some large, modern commercial anchors might be rectangular in cross-section with width-to-depth ratios of 2:1.
The shank cross-section of modern recreational anchors like the Supreme, Anchor Rights Excel, or the Rocna is a knife-blade by comparison, with long rectangular cross-sections of 10:1. Even the Fortress, which has a thicker-than-average shank to make up for the loss of tensile strength in aluminum, has a ratio of approximately 5:1.
In the past, the shanks of leisure anchors such as the CQR and the original drop-forged Danforth were not all that different from those of commercial-vessel anchors. Look at an old CQR, and youll see it has a beefy I-section shank with considerable thickness, close to the 1:1 ratio we see in ships anchors. The simple motivation for the thinner shanks of todays leisure anchors is efficiency and the availability of different, stronger steels. A thin shank allows an anchor to set more deeply, giving it more holding power-and a more likely chance of being rated as having a super-high holding power (SHHP).
One of the topics we want to explore in this report is whether standardized testing-the emphasis on straight-load holding power, in particular-encourages designers of leisure anchors to use thinner shanks that might make them more vulnerable to bending.
This wouldnt seem so unreasonable if we, the consumers, werent indirectly paying for this testing when we purchase higher-priced type-approved anchors. Leisure-anchor makers are more than happy to imply that type approval imparts a high degree of credibility to their product. While the latter might be true (any testing is better than no testing), in our opinion, it would be better if the testing of leisure anchors was more in line with how they are actually used.
Anchor Loads
If a shank is loaded at its end, through the shackle point, then the force required to bend the shank would be most effectively applied at 90 degrees to the length of the shank. The shank would then be at its most vulnerable.
There are standard engineers formulas for calculating the yield strength of metal bars (the point at which they bend): The Force (W, expressed in Newtons) to achieve yield strength equals 1/30 x Y x B x D2/L where:
-Y = Yield Strength in Megapascals (MPa)
-B = Breadth of bar, millimeters
-D = Thickness of bar, millimeters (basically this is the thickness of the steel plate), and
-L = Length of lever arm, millimeters
The development of bending stresses is linear, half way along the beam the stress is half that at the fixed end. At the point where the beam is fixed, the maximum peak stress occurs.
For example, lets look at the yield strength of two straight bars, held at one end and a load imposed at the other end.
Bar 1, which well call our commercial shank has a 30 millimeter x 30 millimeter cross-section (roughly square) and is 1 meter long; Bar 2, our recreational shank is the same length, but has a 100 millimeter x 10 millimeter cross-section. (See illustration No. 3 in Load Factors.) Both bars are made from steel that has the same yield stress: 600 MPa. Bar 1 has a roughly square cross-sectional area of 900 mm2 (30 mm x 30 mm), and Bar 2 has a long, thin cross-sectional area of 1,000 mm2 (100 mm x 10 mm). They are both 1 meter long.

When we apply the formula, the yield strength of our commercial Bar 1 is 5,400 Newtons. This is the equivalent of 550 kilograms of bending force. The yield strength of Bar 2 when the load is applied directly to the thin section (at a 90-degree angle, if it were a shank) is just 2,000 Newtons, a bending force that equals 203 kilograms, less than half that of the commercial bar.
But if you take that same bar, and apply the load in the other direction (i.e. in a straight pull, as is done by the classification societies), the recreational shank appears immensely strong, with a yield strength of 20,000 newtons, a bending force equal to 2,039 kilograms. It doesn’t matter which way you test Bar 1, it has an equal strength, because it has a square cross-section. Stress Bar 2 in one direction, and it is weak, stress it in the other direction, and it is immensely strong. To get to the point: The classification societies make no attempt to measure the strength of the shank in its weakest orientation, when a wind gust hits the set orientation of the anchor at 90 degrees.
Now, imagine Bar 1 as the shank of a small commercial anchor and Bar 2 as the shank of a Danforth or sand-anchor type. It wouldnt matter how you tested the commercial anchor that had Bar 1 for its shank, its equally strong in any direction. However, the Danforth shank is strong in one direction-the direction used by classification societies-but weak in the other direction, the direction it would be loaded if the wind were to shift suddenly 90 degrees while the anchor stayed put.
Deeper Setting Anchors
Leisure anchors have become more efficient and have increased holding capacity. By definition, increased holding capacity means they can set more deeply and more securely than previous, older models. The fact they can become immovable has obvious advantages. A disadvantage is that if a deeply set anchor is loaded at 90 degrees to the direction of set, the fluke might not have time to turn and the shank must be able to withstand a load applied to its weaker section.
While a few leisure anchors like the Fortress, Bugel, and Danforth have regularly shaped, straight shanks, most do not. However, leisure anchors with a shank similar to the Delta (of which there are many variants), including Rocna and Anchor Rights Excel, are effectively L shaped, an almost straight lever arm joined to a vertical.
Using formulas to compare anchor shanks, however, can quickly lead to problems. Comparing the shank of the Manson Supreme to that of a Delta, for example, would require a serious analysis of leverage in an irregularly shaped beam. In the same manner, the complex hollow shanks of the Ultra and Spade defy any quick strength calculation without the help of some sophisticated engineering software. Ultra reinforces its tubular shank with a strengthening section inside the tube to impart additional strength in the transverse section. However, it is possible to compare the calculated strengths of the same anchors comprising different metals.
Shank thickness is obviously important to strength, but the anchor maker has a number of problems with which to contend. Steel plate comes in standard thicknesses, and sometimes that thickness might not match the scaling for some anchor sizes. Bisplate, a popular brand of anchor steel from the Australian company Bisalloy, comes in certain thicknesses (8 millimeter, 10 millimeter, 12 millimeter, 16 millimeter, 20 millimeter, and so on). An anchor that might need a 14-millimeter-thick shank is either made with an undersized 12-millimeter plate or an over-sized 16-millimeter plate.
Carrying stock of thick plate is expensive, especially since sales of very large anchors are infrequent. For this reason, some anchor makers resort to welding to increase thickness. Technically, there is nothing wrong with this approach, as long as it is completed correctly. Inadequately welded, these shanks, however, could allow water ingress and unseen corrosion.
So much for the theory on shank strength.
Anchor Metallurgy
Metallurgy in anchors has come under increased scrutiny, and the anchor maker Rocna faced the closest scrutiny of all in 2011 when a former employee reported that the shanks of many of its anchors did not meet the advertised claims or metallurgy. (See Inside Practical Sailor blog post Rocna Anchor Exchange Program Begins.)
The yield strength of one bent anchor was found to be 357 MPa. At the time the anchor was purchased in France, Rocna was promoting on its website that its shanks were made using Bisplate 80, which has a typical yield stress of 750 MPa (minimum 690 MPa). While both Rocna and its major U.S. distributor admitted that certain Rocna anchors were made with a weaker grade of steel compared to that published on the Rocna website, the actual number of anchors remains unknown.
Rocnas major distributor in the U.S., West Marine, offered to exchange the anchors of any unhappy owners, and Rocna has since adjusted its marketing claims. We recently met with the new owners of Rocna, Canada Metal Pacific, at the Miami Boat Show. We were impressed with the companys commitment to clearing the name, and their confidence in the current construction and materials. As a prelude to an upcoming physical test of shank strength in a variety of anchors, we recently conducted a crude test of yield strength on the shank of an ungalvanized, 10-kilogram Rocna. The 10-kilogram Rocna has a lever arm of 529 millimeters, a width at the end of the lever arm of 92 millimeters and thickness of 10 millimeters.
Based on these measurements and the assumption that this was one of the Chinese-made anchors of a lesser-grade steel, we projected the shank would bend somewhere between 210 kilograms (for 356 MPa steel) and 263 kilograms (for 445 MPa steel). We checked the theory with practice by bolting the fluke into a reinforced concrete floor and loading it at 90 degrees with a block and tackle. We then measured the load at various intervals until a significant permanent bend was achieved.
We did not shock-load the shank but steadily increased the load, relaxed the load to zero and looked for deformation, and then continued the process, increasing the load in 20-kilogram increments.
We were able to achieve a noticeable 10- to 15-degree permanent bend in the shank with a load of about 230 kilograms. At lower loads, the shank demonstrated considerable elasticity, but minimal permanent bending.
The theory and practice of forces enabling shank bending look to be in relatively close agreement. The theory suggested bending at between 210 and 260 kilograms; in practice, the bending occurred around 230 kilograms.
In the May 2012 edition of Practical Sailor, we published some results on measuring the load of a 38-foot catamarans anchor rode at a 6.6:1 ratio, in winds up to about 30 knots. At 30 knots, loads were measured at slightly higher than 300 kilograms. Of course, we would be using a larger, 25-kilogram anchor for this boat. Based on its measurements, this anchor (assuming it is made with the same steel as the 10-kilogram model we tested) would require about 500 kilograms of load to begin bending.
Although our wind-load data did not lend itself to precise extrapolation, the curves suggested that a 40-knot wind would generate enough load to produce the 500-kilogram load required to bend the shank of a 25-kilogram Rocna-if that load were applied at a 90-degree angle. At the end of the day, this is all speculation, though. What we are more concerned about is what happens in actual load testing, and what happens when anchor makers use the same design for a range of anchors made of very different metals.
Mixing Metals
One could say that the Rocna example is an isolated case, and it has been resolved. However, anyone who has spent any time in marinas or boat yards knows that bent anchor shanks happen-probably more frequently than we would guess.
Anchors are possibly one of the few items of marine equipment, whether a safety item or not, that isn’t made within a standard and is, with a few exceptions, sold without any specification at all. Anchors are sold by weight, sometimes by surface area-but nothing else is specified. Buy a new halyard and you will find it specified by size, strength, and elasticity; buy a life jacket and it will meet specific regulations-not so for anchors.
Whether the anchors we see on chandlery floors are designed to have no safety factor or a safety factor of four, no one knows. And it does make us uncomfortable that a product so reliant on its metallurgy does not proudly advertise its composition. Having bought an anchor deemed by a distant classification society as fit for purpose is little comfort when you have just been forecast a storm warning and you have nowhere to go.
Look at most of the anchor makers who have CS-type approval-excluding Fortress, which only makes alloy anchors, and Ultra and Wasi, who only make stainless-steel anchors-and it is possible to find manufacturers who make both galvanized-steel anchors and stainless-steel anchors to the same exact design.
Manson, Anchor Right, and, originally, Rocna made claim to the high-strength steels used in their anchors. All three claim (or claimed) use of quenched and tempered high tensile steels. Other anchor makers make less specific claims. Lewmar claims its Delta uses a high-grade manganese steel (and stainless steel) for maximum tensile strength. All of these companies also claim, or claimed, to have a form of approval, but should that approval carry over to all metals? Type approval demands specific drawings, specific raw materials, an ability to meet holding capacity, and an ability to meet proof testing requirements. As we have seen, proof testing is not onerous.
In our view, it is contradictory to suggest, on one hand, that a quench and tempered steel, with a yield strength of typically 750 MPa, is necessary for the shank of a galvanized anchor, and then, on the other hand, to sell an identical design, typically made from 316 stainless steel with a tensile strength of only 205 MPa. Higher grades of stainless steel are available, but if it is used in anchors, its use is not advertised. (Grade 2205 stainless steel, for example, has a yield strength of 450 MPa-roughly the equivalent of the Chinese Q420 steel Rocna reportedly used.)
Other possible anchor-making materials include mild steel (minimum yield strength of 240 MPa), aluminum (minimum yield strength of 125 MPa), 5083 marine-grade aluminum alloy (minimum yield strength of 240 MPa), 6061 T6 aluminium (minimum yield strength of 276 MPa), and 7075 aluminium alloy (minimum yield strength of 503 MPa), though this latter grade is expensive and hard to find.
Based on the measurements of Anchor Rights Excel, which is a flattened, convex-fluked model with a shank similar to that of the Delta, the force necessary to bend the shank-assuming it is made of high-quality Bisalloy 80-would be 562 kilograms. To achieve the same strength with 316 stainless steel would demand a shank thickness of 22 millimeters. With 5083 aluminum, a 20-millimeter-thick shank would be required. Having a shank 1.7 times wider than the standard galvanized version will obviously alter both balance and performance.
In fact, Anchor Right makes a 5083 aluminium version that weighs 8.3 kilograms, compared to 16.5 kilograms for the galvanized version. This aluminum version has a 16-millimeter-thick shank, so the load required to bend the shank would be about 348 kilograms.
The stainless version of the 16.5-kilogram Excel has exactly the same dimensions as the galvanized version. If this is 316 stainless steel, then the 90-degree load required to bend the shank would be a mere 167 kilograms.
All anchors are a compromise, but sometimes beauty, or light weight, comes at a cost.
Sailing has risks that most sailors understand and accept. They know information on the weather is simply a forecast; there is no certainty. They know that electronics subjected to a salty, humid environment might fail. However, they expect their properly serviced life raft to inflate and float, and they expect newly purchased flares to work. We believe they should have the same level of confidence in their anchor quality and performance.
In our opinion, there is a strong case for the leisure anchor makers and the classification societies to make the testing and approval of anchors more meaningful. We all might have become single-minded in our fascination with holding capacity to the exclusion of other anchor parameters-namely the anchors ability to withstand all the potential loads that might eventuate.
There is a very strong case for anchor makers to be more accountable and open regarding the raw materials and performance of their products, and there is certainly a case for more probing analysis by magazines, including Practical Sailor, to investigate and monitor anchor characteristics. In the final segment of this two-part series, coming up next month, we finally get to bend some anchors.
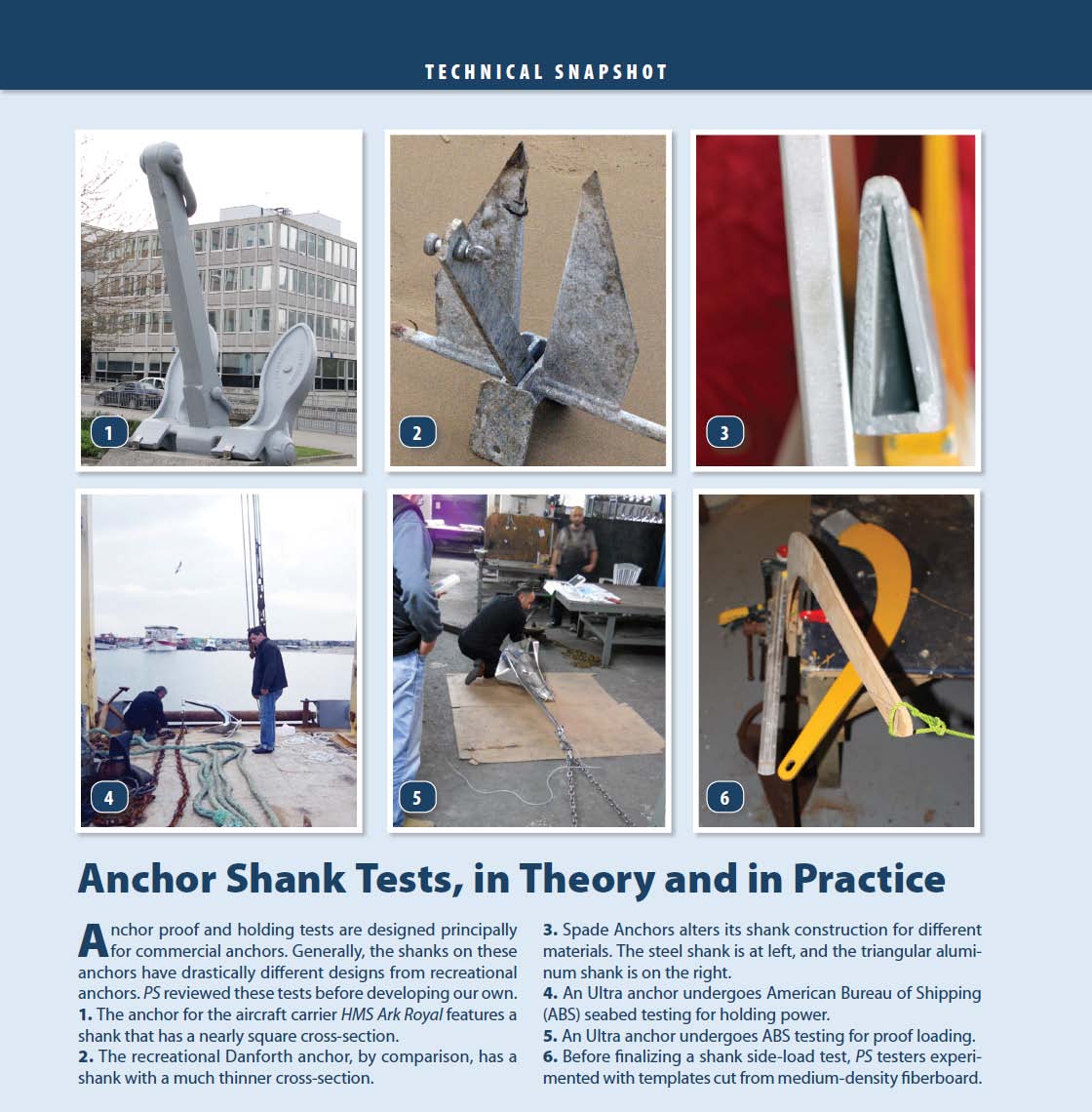
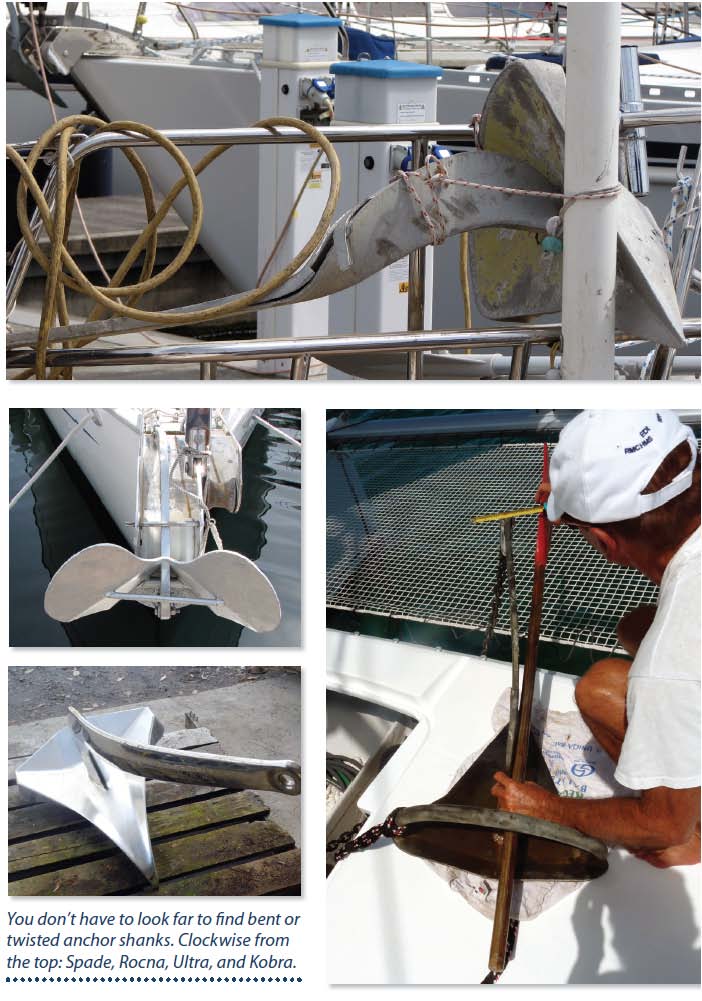
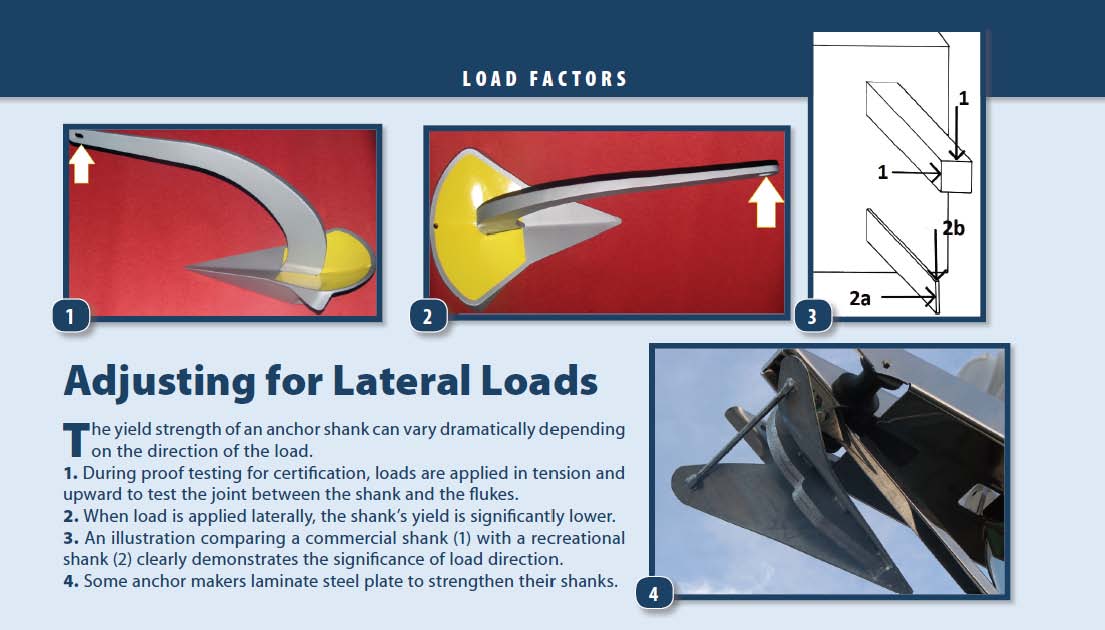