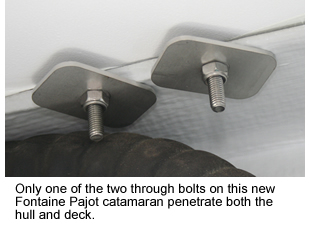
Improperly mounted stanchion and pulpit bases are a major cause of gelcoat cracks in the deck radiating from the attached hardware. The cracks are usually the result of unequally stressed mounting fastenings or inadequate underdeck distribution of hardware loads. Frequently, a boat is received from the builder with local cracks already developed. Once the deck gets dirty enough, these minute cracks start to show up as tiny spider webs slightly darker than the surrounding deck gelcoat While repairing these cracks is a fairly difficult cosmetic fix, the underlying problem – poor mounting – is fairly easy to correct in most cases.
For better or worse, production keep the cost of their boats competitive. Unfortunately, cutting corners is the rule rather than the exception in production boatbuilding. While you can’t change that situation, you can do a lot to correct the shortcomings that are a function of corner- cutting, including poorly mounted stanchions and pulpits.
The most typical problem in stanchion mounting is the base which straddles the inward-turning flange of the hull-to-deck joint. Frequently, the outboard bolts will go through both the hull and deck, while the inboard fastenings merely go through the deck. When a backing plate is installed that straddles the edge of the inward-turning hull flange under the deck, it is frequently distorted as the bolts fastening the stanchion bases are tightened. Tightening down the bolts when the backing plate doesn’t lie flush to the underside of the deck inevitably causes local stresses in the deck, frequently resulting in the characteristic spider web of gelcoat cracks.
In order to avoid the problem, some builders simply use oversize washers under the nuts of through-deck bolts. These are not adequate to resist strong local loads, such as leaning hard against a lifeline stanchion. A backing plate of rigid material, at least the size of the base of the hardware to be attached, is the proper solution.
It is fairly common for builders to use fiberglass backing plates, cut from discarded sections of moldings such as cutouts for hatches. While a fiberglass backing plate is better than nothing, it can easily split or distort when bolts are tightened, reducing its effectiveness.
With stainless steel or aluminum hardware, fastened with stainless steel bolts, backing plates of stainless steel or aluminum, between 1/4-inch and 1/2-inch thick are a good choice. Marine-grade plywood, if it is sealed properly, also makes a good backing plate, although you will want to seal it with epoxy to prevent rot. One of our favorite backing plates is G-10, a superstrong – but not cheap – fiberglass laminate especially made for use in highly loaded areas.