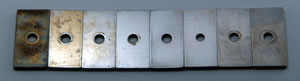
Samples were tested for corrosion protection following the ASTM D1384 Corrosion in Glassware method (www.astm.org). Samples were diluted to 33-percent glycol, dosed with ASTM synthetic corrosive water (similar to 2-percent seawater), continuously aerated, and heated to 190 degrees for two weeks. As a laboratory control, a reference coolant (ASTM D 3585) was also exposed to provide a baseline.
At the end of the test period, the samples were cleaned according to a specified ASTM procedure, dried, and evaluated for both a change in appearance and loss in weight. While this is not considered to be a definitive test of acceptability-extensive fleet testing is always the bottom line-it has a long history as a screening test. Because the test is run with synthetic corrosive water and because of the accelerated nature of the testing, it is best not to read too much into minor differences between products, so long as they meet ASTM specification.
All of the tested engine coolants performed well in the screening level test-literally 1,000 times better than raw water-but there were some differences in performance. Winterization products (-50 burst-point propylene glycol formulas) performed surprisingly well for products intended for much milder conditions; however, we do not recommend any winterization product for engine coolant service-and neither do their respective manufacturers.
Diesel coolants were tested for cavitation pitting by exposing cast-iron coupons in an ultrasound bath for four hours, simulating cylinder-liner ringing. Any evidence of pitting or freckling was considered to be a failure. The purpose of this test was to identify coolants that effectively combat cylinder liner pitting.
The very best coupons, not surprisingly, were from the heavy-duty coolants, specifically formulated to endure the sort of torture commonplace in a heavily loaded diesel engine. Though you might get away with any of the long-life coolants in diesel service, we still like the idea of using heavy-duty coolants in wet-sleeve diesels and in boat engines with severe duty cycles (commercial fishing boats, trawlers, anyone that runs long and hard).
We also tested the products freeze points; all concentrated coolants were properly diluted, and all concentrates met concentrate specifications.