Modern yachts are frequently advertised as having spacious cockpits: and, indeed, they do. But it doesn’t take many afternoons of sailing to discover that the cockpit which seemed so splendidly roomy in the showroom or at the boatyard is too damned wide: it’s impossible to brace your legs across the footwell without sliding down so that your body only contacts the boat at shoulders and tailbone. If you want to sit on the cockpit coaming while steering there’s no place at all to brace your feet.
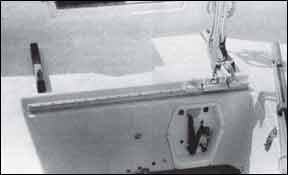
288
The answer to these problems is not to narrow the cockpit, but to install wood foot braces at strategic locations. The project is truly simple, but very satisfying because the results really add to your sailing comfort, enjoyment, and efficiency.
The first step is to decide on the location of the braces. To begin with, you’ve got to have enough experience with sailing the boat to know where the helmsman normally sits, and where passengers/crew will need to have foot braces. When determining the location for the braces, keep the clutter to a minimum. Think about how to retain a clear cockpit for use in harbor. You don’t want to ruin one aspect of the boat to improve another.
The photograph shows the way the problem was solved on our Scampi. The two normal steering positions are on the cockpit seats at the forward end of the well and on the cockpit coarnings right up next to the cabin’s aft bulkhead. For the cockpit position, a strip of wood was bolted down the centerline of the wood cockpit liner. For the coaming steering position, strips of wood were bolted to the bridgedeck on either side of the companionway.
The positions of the bridgedeck strips were arrived at by the simple process of having the regular helmsmen (a short one and a tall one) sit normally to see where our feet naturally fall . . . high tech stuff! We compromised on a position which suits us both and which still leaves enough room between the braces and the cockpit coaming so that most luxurious of activities — sitting reading with your back against the cabin bulkhead, legs up on the cockpit seats and the anchorage spread out before you — can still be enjoyed.
The brace on the cockpit floor runs right down the centerline and serves us well, but a wider well or a crew with shorter legs might be better served by parallel braces set at whatever is the appropriate distance from the centerline.
As to size, the bridgedeck braces are 2″ high and have vertical sides. For the sake of appearance and to diminish bruises and trapped sheets, the ends are angled down and the top edges slightly rounded.
The cockpit sole brace is 1 114″ high and has a rounded cross section.
I’d say the best material for the braces would be teak, oiled or left bare. The mahoganies and woods like oak, fir, or pine will blacken in an application like this where constant abrasion will inevitably wear away paint or varnish.
As to installation, through bolting is the best — perhaps the only good — approach. Because most of you will be bolting through unreinforced areas of foam or balsa cored fiberglass, backing blocks about 3″ square should be used under the nuts to distribute the strain. Also, use a good bedding compound. As this is permanent installation, one of the silicone compounds should serve well, but be sure to clean up carefully before the compound sets or you’ll have later to go to work with buffing compound.
If you don’t want the installation to be permanent, it’s possible to make the braces removable. Many good hardware stores carry threaded inserts which are normally meant to be screwed into wood parts that require frequent disassembly. These inserts are tapped for machine screw threads.
To install, a hole is drilled in the deck or cockpit sole of the appropriate size for the insert. If the deck is cored with balsa at that point, it will be necessary to dig out the core about 1/2″ around the hole and fill it with an epoxy filler such as Marinetex. Fill the hole with the epoxy and press the insert in. The trick here is keeping the filler out of the threads.
Alternatively, you could fill the hole completely, allow the filler to harden, then drill out for the insert. The footrests are then secured with bolts, and are easily removed at any time.
Before buying the inserts, make sure they are not just plated steel. Most are, but brass ones are also available.. A quick check with a magnet will tell you if you’re looking at solid brass or brass-plated steel.
Only an hour or two of work total, and you improve your boat and your pleasure enormously.
-JP