In 1990 Practical Sailor published Comtex Development’s definitive findings about the causes of blisters on fiberglass hulls. The author was Rick Strand, then president of Comtex and formerly chief engineer at Tillotson-Pearson boatbuilders in Rhode Island. Today Strand runs a testing and consulting firm and lab under his own name in New Hampshire. Here’s his update, 11 years down the line.
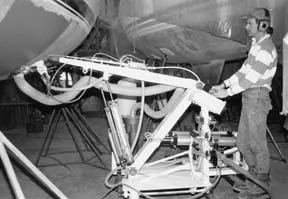
———-
Luckily, we don’t have to report that we were all wrong about blisters 11 years ago. In fact, research and experience in the intervening years have helped confirm the findings of the research we did at Comtex, and before that at Tillotson-Pearson. Unfortunately, despite that research, and the fact that our findings were widespread among boatbuilders and the boating media, plenty of boats are still being built in ways that are likely to invite blistering.
Blister History
At Tillotson-Pearson in the early to mid-1980s we looked long and hard at the blister-generation problem, but never fully understood exactly what caused it. Bits and pieces of the puzzle were lying around waiting for someone to properly assemble them. Many other researchers who looked at this problem drew shallow conclusions and created misconceptions where causes were concerned. For example, gelcoats were the initial recipients of the blame for blistering. After all, it was the gelcoat that had all the bumps showing on it.
It soon became evident, however, that hulls with blistered gelcoats all had wet laminates underneath. We already knew a lot about the moisture and chemical resistance of various resins, so it made sense to look at their possible role in keeping water out of hulls. We eventually learned through iterative lab studies that higher-quality resins helped the problem significantly. Soon we knew that building with vinylester resin could yield relatively blister-free hull laminates.
By 1985, the practice developed by TPI, working with Interplastic Resins, was to build the layers closest to the exterior gelcoat finish using vinylester resins, then switch back to lower-cost resins. This process is known today as skin coating. Interplastic went on to market the use of their resins nationally as a blister resistant “skin coat” product.
At Comtex in the late ’80s and early ’90s we focused on discovering the fundamental causes of blistering. We dissected over four hundred samples taken from blistered boats all over the United States. We offered a service to assist the yard and owner to determine what factors caused blisters on a vessel in question as well as to what the best repair course was. A complete vessel history was submitted along with photographs and through-hull core samples (exterior skin only of cored laminates) for review and analysis in the lab. Microanalysis was combined with chemical and physical analysis to determine cause and severity.
In some of our tests we looked at fillers and solid modifiers that were present in the laminate layers during construction. This was done by burning off resin from fiber in laminate layers using a small kiln. As long as the melt temperature of glass (E glass) is not approached in the process, one can effectively remove all the resin from a fiberglass laminate, leaving fibers and fillers undisturbed. What remains is subjected to microanalysis as well as density separations for identification.
The most important factor found in this type of test related to the use of fumed silica. Silica is used to thicken resin, somewhat like cornstarch thickens sauces. Fumed silica is added to most production laminating resins so that it won’t drain out of glass reinforcements when the boat is being built in the mold.
The fumed silica particle is shaped like a flat potato chip, only much smaller. It has irregular edges and a variable aspect ratio. It’s a lot like mica in that it has very low shear strength parallel with its surface. It’s a very weak substance to begin with, it tends to flake — and, as it turns out, it was implicated in many blistering problems we found.
Depending on the training received by the laminator or the techniques used by the builder in producing the first couple of laminated layers behind the gelcoat, fumed silica can be concentrated at different depths in the laminate thickness. This can happen when a laminate layer is rolled out in production. As resin flows up through the reinforcement from a pre-wet surface in the mold, the glass fibers in that layer tend to filter the fumed silica out of the resin. This happens most commonly when the builder is using a thick layer of mat reinforcement (over 1-oz. per square ft. in weight). The result is a fine layer of silica platelets spread over the surface of the reinforcement layer. This usually occurs right up against the backside of the gelcoat or between the first and second plies of mat, and can cause moderate to severe interply adhesion problems. In our testing we found that 31% of all blistering problems were caused by the concentration of silica in either of the first two laminated layers.
All marine laminates will absorb moisture to some degree. If you consider the laminate as a fixed volume, introducing water into it must either cause an increase in volume, or internal pressure, or both. The reality is that both occur, but at slightly different times.
As a blistering laminate degrades in the presence of water, internal pressure is created. The resin in the laminate also weakens due to hydrolysis (molecular chain breakage). Like the weak link in a chain, the weakest interfacial layer will allow separation to occur and a blister dome will rise up at that point to relieve internal pressure. Simultaneously, the area around the blister dome swells and the resin in that area begins to tear away from itself. The tearing is usually worst where the weak silica platelets are concentrated. They tend to shear apart at relatively low pressures.
Silica is still the primary thixotrope (thickening agent) used in marine production resins. That’s not necessarily bad, but today we now know a lot more about the importance of working with the material correctly.

For example, timing is critical: The proper way to build the first laminate layer behind the gelcoat is to do it immediately after the gelcoat has become tacky but will not transfer color to your finger. The reason is that when the gelcoat is still tacky, it’s not completely cured. The next layer (and its wet resin) going onto the backside of the gelcoat will slightly re-dissolve its surface. The molecules of the wet layer can mingle with the surface molecules of the tacky gelcoat layer and co-cure. The co-cure of the entangled molecules at the interface creates an almost inseparable bond that is nearly seamless. If the gelcoat cures hard and tack-free, there will be less solvation, entanglement and co-curing when the next wet layer goes down on the backside of the gelcoat. The result is a significantly weakened interface-one of the weak links we discovered years ago. Nearly 22% of all blisters were caused by poor chemical adhesion between the gelcoat and first laminated layer.
I would estimate that using conventional materials, a boat with a bad gelcoat/first layer interface would blister three to five times more quickly. This same type of problem is why some epoxy coatings won’t stick well enough to polyester laminate to function well as a blister resistant coating.
Ironically, the first layer of laminate is best made of chopped glass – a technique that was frowned upon in the days when many builders associated quality construction with a hand-laid and rolled first layer made of mat. In fact, the 1- to 1-1/2-oz. mats that were used caused a lot of the silica filtering problems. Those problems are drastically reduced if the first layer is shot on with a chopper gun. In a double irony, many builders operate that way these days-not necessarily because the mat might cause blisters, but because chop is faster and cheaper to use.
Fix-It History
At Comtex, as we were investigating the causes of blistering, we were also evaluating blister repair materials and methods. Knowing the initial cause and severity of a particular case of blisters became invaluable when estimating repair longevity. Thanks to our friends at Jamestown Boatyard in Jamestown, Rhode Island, we had a seemingly endless supply of blistered bottoms and scrap blistered laminate to work with.
During this time, there was a lot of emphasis placed on the importance of drying a hull prior to repair. Jono Billings, owner of Jamestown Boatyard, was busy experimenting with drying techniques. At that time, they consisted of tenting the bottom with polyethylene film while heating and dehumidifying the tent. The techniques used today are roughly similar but much better understood.
Back then we wondered how much drying time was enough, and why there was always still some moisture left in the hull. At Comtex, we would section a pie slice of our through hull core sample (across the surface plane) using a scalpel and a small hammer. Each wafer of slightly varying thickness was carefully weighed, then dried (heat and vacuum) and re-weighed to provide a moisture gradient through the thickness. We quickly found that a front-loaded approximate bell curve was typical for a blistered laminate. We placed some wet laminates with pre-measured gradients into the boatyard’s drying environment and took new samples for a gradient check on a regular basis. We found, quite interestingly, that even an extensive dry time in a tented environment provided only marginal drying to any laminate depth beyond 20/1000 of an inch.
Using a similar method, we quickly found that heat and vacuum would dry exterior surfaces more quickly as well as reach further into the thickness. Unfortunately, a vacuum assist would only provide moisture draw to about one tenth of an inch of laminate depth. This varied widely depending on the condition of the degraded laminate sample.
In the majority of laminates analyzed by Comtex, usually no more than the outer tenth of an inch of laminate was affected by blister degradation. In the worst cases it was about a quarter of an inch. It was also found that no matter how badly degraded from blistering a laminate was, the insulating power of about eighty thousandths of an inch of vinylester would hold off the osmotic permeation of water.
The method used to remove the old and degraded laminate was, and still is, to “peel” it with a routing (planing) device set to remove flat, controlled amounts of laminate. Removal of the laminate does several things. It gets rid of the worst layers of degraded (and osmotic) material, thus also removing some of the moisture and providing a cleaner, drier surface for re-lamination. At this point the hull could be dried or washed with a solvent to facilitate the removal of surface moisture. This is where a graph of moisture gradient is useful to the “doctor.”
When the surface is clean and dry, laminate is replaced exactly as it was removed. In some cases there may be stronger fabric layers present, which need reconstruction. This is where the ply count is found from the kiln burn-off data; again, useful to the doctor. (The strength and stiffness of your vessel might improve a bit with heavier or increased lamination, but it’s important to model the re-construction to yield a similar boat structure). During re-lamination, all those adhesion-related considerations need management. Finally, the finish coat is properly entangled (tacky adhesion) with the last re-laminated layer to yield the finished repair.
Where We Are Today
Vinylester re-lamination is still about the most effective way to repair a blistered hull. How much comes off or goes on depends. Without any diagnosis, about one tenth of an inch will do in a quality job. Other coatings -urethanes, epoxies, etc.- can be considered, but boatowners would certainly need to have an expert evaluation before knowing if one of these alternatives might work.
The reality is that vinylester skin coating is still not the norm. Builders of high-performance and quality vessels in the marine industry do use vinylester barrier technology to cut the legs off of the blister problem. Companies like Thunderbird Products of Decatur Illinois (builders of Formula) use other types of high-performance resins that achieve the same end. I would estimate that somewhere in the range of 15 to 18 percent of all boats manufactured in the US use higher-quality (and higher-cost) resins to address the potential blister problem. (The percentage is higher in the sailboat-only industry). The rest use lower-cost resins based on DCPD polyester.
There are a vast assortment of products and methods out there for fixing or preventing marine blistering. Most are expensive, but, like dealing with health problems, dealing with blister problems is best done in consultation with experts: The patient needs to be subjected to a few tests before we can fix him.
If a boat has a fundamental problem like a poorly bonded gelcoat, the task of removing and replacing it with a suitable gelcoat might last for years, provided there are no other problems. A situation where the blisters are located between laminated layers one and two, caused by light silica concentration in a moderately degraded laminate (pH around 4.0) might take only one season to reblister after having been repaired by the same method. If you want to do a longlasting repair for the right cost, find a yard that will do the job right – a gelcoat peel of 0.1″ at a minimum, followed by drying and vinylester relamination. See the sidebar on page 11 for a list of surveyors and yards known for doing things the right way.
Also With This Article
Click here to view “The Sponge You Never Wanted.”
Click here to view “Top Warriors in the Blister Battle.”
Click here to view “Anatomy of a Laminate.”