
Technical Editor Ralph Naranjo equates spare time with boat projects. His basement shop/test facility has spawned a wide range of boats, boards, and parts for bigger boats. The two latest are test platforms for long-term evaluation of the resins and materials looked at in this round of epoxy evaluation.
“Bits and Pieces” is a kayak hull skin made of E-glass/polyester resin and was hand laid up using a rotomolded Wilderness System Pamlico kayak as a male mold. The hull was intentionally built with a thin laminate schedule. Ralph planned to stiffen the structure with a carbon fiber/epoxy longitudinal and transverse grid that would be secondary-bonded to the inner skin.
Care was taken to de-wax, sand (80-grit), vacuum debris, and solvent-wipe the hull in order to create a good anchoring pattern. High mechanical strength fillers were used to thicken the epoxy resin for gluing when needed. Easy to sand, lower shear strength fairing fillers were used for only cosmetic purposes.
The kayak will serve as a long term-test platform looking at secondary bonds used to attach pre-formed carbon epoxy longitudinal stringers to the polyester hull. He also laminated in place transverse E-glass and carbon fiber supports. In some areas, core material from Lantor (Coremat) and Gurit (Corecell) were added to increase stiffness. How well these tabbed-in secondary bonds and glued-in stiffeners hold up will be carefully tracked.
The second floating artifact in our epoxy sea-trial was a stand-up paddleboard made from thermal foam insulation, remnants of Practical Sailor’s refrigeration testing. After doodling a sketch of a paddleboard, our intrepid technical editor glued the 2-by-8-foot sheets of 2-inch thermal insulation foam to form a big block. Next he lofted his sketch and cut out a plywood template (full length but only one half of the deck plan). He scribed a centerline on the foam block and used the template to create an identical rail curve on each side of the centerline, shaping the contour with a power plane and long boards.
From the start, he recognized that the structural quality of the foam was poor, far inferior to the PVC foam used in boat building or the polyurethane foam shapers use to build surfboards. But that’s exactly what he was looking for, a material that provided the shape but left most of the load carrying capacity to the skin of the structure itself. This will place higher demands on the resins that PS is testing.
During the building process, it’s important to wet-out but not oversaturate the woven or stitched laminate. More fiber and less resin is the mantra, and with epoxy, there are a few tricks of the trade that really pay off. The first is to make sure that the fiber material you use has a finish that is compatible with epoxy resin. Remember, it’s the finish that’s been placed on the filaments during their manufacture that bonds with the resin. Not all fiber finishes will bond with both polyester and epoxy resin. Check with the cloth supplier about epoxy compatibility.
Use ambient heat to your advantage by timing the wet-out process to coincide with max air temperature, making sure that the mold and surrounding air temperature will either remain the same or gradually decrease as the epoxy gels. This will insure that the resin is both free flowing during the application process and that there’s less likelihood of out gassing and pinhole or void creation. Also, by choosing the proper hardener for a specific temperature range, you will be able to prevent the resin from gelling too quickly, which can lead to excess exothermic heat buildup caused by the chemical reaction. This extended workability window is a big advantage over poly and vinylester resins. It is extremely important, however, to make sure the resin-to-hardener ratio is carefully followed.
As with painting projects, start with small area product familiarization. Mix small batches and have a variety of tools at the ready (chip brushes, plastic squeegees, scissors, etc.) Mix the resin in cans or plastic containers rated for such chemical use. Wear gloves, skin and eye protection, and keep in mind that even though epoxy is not as aromatic as polyester resin, users can become highly allergic to the amine hardener and sanding dust (especially of recently cured material).
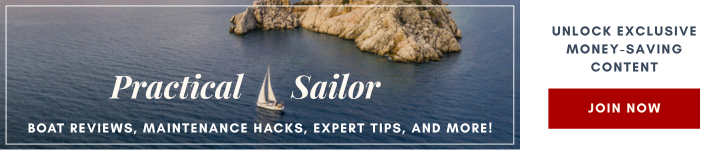