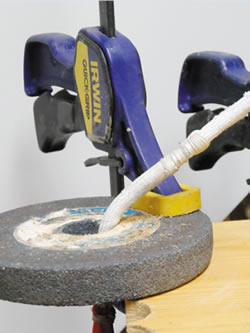
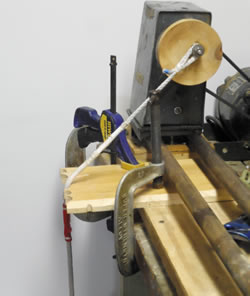
Testers first task was to determine whether any of these coatings could weaken line in the near term. To do this, we formed 20-inch loops of 1/8-inch polyester braid and nylon braid, coated a 1-inch length of the loop with each of the products, and broke these in our test rig.
To test for chafe protection, we started with polyester double-braid line (3/8-inch diameter) rather than stitched eyes because this reduced the number of variables. We focused on polyester double braid because it is the most common line, and even high-modulus lines commonly have polyester covers.
Our test machine was a wood lathe that we modified to chafe lines at a realistic speed. The setup was efficient and allowed us to select an ideal load and abrading surface. The machine pulled a test line back and forth at a fixed rate (amplitude was -inch at 7 hertz) and velocity (1.4 feet per second). For this article, we settled on three pounds of line tension (applied by a spring scale) and a deflection angle at the abrading surface of 45 degrees.
Our abrading surfaces were wood (fresh sawn surface for each trial) and a medium-grit, aluminum-oxide grinding stone. For coatings, we ran each test until the rope cover failed. For physical protectors, we ran each test until the physical cover failed. The accompanying Value Guide describes these important differences in the way testing was conducted for each type of product.
To test a stitched eyes ability to resist abrasion, we ran the stitched portion on our machine for a fixed period (the time required to abrade roughly 30 percent of our test ropes cover when unprotected), and then tested for strength. We tested both eyes that had been stitched using round stitching and basting. We tested polyester and Dyneema twine.
For long-term testing, we constructed 8-inch-long samples of the various products and left them to weather. After a fixed period of exposure, the samples will be break-tested. Another set of control samples are being stored inside. These samples will be break-tested every two years, for six years. Unprotected line, webbing, and whipping twine have also been left outdoors.
On a test boat that is stored on the water year round on Chesapeake Bay, we have installed a wide variety of covered splices, sewn and conventional, with the various protective materials. We also coated certain lines where abrasion has been a minor problem but where fitting bulkier chafe gear would be impractical.