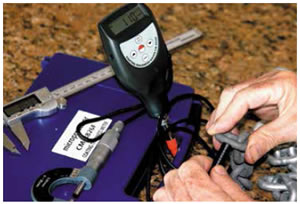
In order to impart corrosion resistance to steel, the items are commonly galvanized, immersed in a bath of molten zinc. Hot-dip galvanizing is well established and accepted, but there are alternate technologies like sherardizing.
Sherardizing was developed in the United Kingdom around 1900, where it was found that by packing steel parts in a sealed container with a mixture of sand and zinc powder and then heating and rotating the container, the zinc would sublimate (vaporize from the solid state without a liquid phase, like dry ice). The zinc diffused onto the steel, producing a zinc-rich external layer, a zinc/iron alloy. This resultant coating offered corrosion resistance and had good anti-wear and anti-abrasion properties.
Sherardizing requires the zinc to be mixed with the sand in order to keep the zinc from melting on the walls of the mixing container. Much of the zinc is not actually used in the process and simply oxidizes, and the sand is not easily recyclable. This is just one of several drawbacks to the inefficient process, which is subject to stringent and expensive environmental controls-if it is allowed at all.
Thermal diffusion galvanizing, a relatively new process licensed by Distek under the name Armorgalv seeks to overcome these inefficiencies. The process simply uses a powder of zinc that is alloyed so that it will sublimate around 250 degrees Celsius. The powder and the items to be coated are put in a sealed vessel that is placed in an oven and rotated to heat evenly. No sand is used in the process, and all the zinc is used, leaving behind only an inert powder that is easily disposed. According to Distek, the process can achieve an even coating of up to 200 microns.
The resultant Armorgalv coating contains no free zinc but is an alloy of iron and zinc, which is corrosion and abrasion resistant. Because the zinc diffuses into the steel, the coating is stronger than a conventional galvanized coating. Being a vapor process, the operation is ideal for intricate parts and for parts that demand a strict control of the thickness of coating (like nuts and bolts). The relatively low temperature of the process lends itself to the coating of high tensile, quench-and-tempered steel, which would otherwise be weakened by the temperature required for hot-dip galvanizing (around 465 degrees C). One report indicated that 1200 megapascal steel (G120 steel chain) can be treated without any harmful impact on the pre-coated steel physical properties.
So far, the focus of Armorgalvs claims have centered on the superior corrosion resistance and the ability to treat high-tensile steel without reducing its strength. The other characteristics of the end product: ductility, elasticity, stress corrosion cracking, notch sensitivity (reduction in strength due to the presence of a notch), etc. have not been documented.
Both Armorgalv and hot-dipped galvanizing produce iron/zinc-rich alloyed coatings. The characteristics of the coatings are different, however. A hot-dipped galvanized coating is much softer than an Armorgalv coating.
The major downside of the process is that large items cannot be treated. Chain, however, has not proven to be a problem, and treatment of shackles, hooks, and other lifting hardware is already part of standard production.