The first time I brought a handful of low friction rings (LFR) to the boat, I got funny looks from my partner. The plan was to set up a barber hauler. Familiar to small-boat sailers and racers, a barber hauler is effectively a moveable sheet lead that allows us to fine tune headsail trim (see PS September 2019, “Try a Barber Hauler for Better Sail Trim”).
Capable of trimming the jib sheet or spinnaker guy inboard, up, or down, the Barber hauler can control headsail twist, as well as allow you to open or close the “slot” where the headsail overlaps the main (or staysail, if fitted). On big boats, the lead would comprise a lightweight block (often a snatch block) attached to a lightweight line. Typically the block would be clapped onto the jib sheet after the clew.
While a barber hauler might not have such dramatic impact on the passage times of a fully-loaded cruiser, the headsail trim pays off handsomely on performance cruisers or daysailors like my F-24 Corsair trimaran.
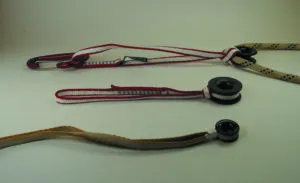
Any hardware linked to the jib sheet can become a tethered projectile as the jib flails, so the ideal barber hauler lead would be lightweight. In the past, barber haulers relied on lightweight bearing blocks to redirect the jib sheet. These days, simple and inexpensive low friction rings (LFRs) have become our default choice any time we want to redirect a line—especially when we are redirecting a line that is relatively lightly loaded.
Because bearing bocks offer more efficiency than low friction rings, they are preferred for high-load, high-friction jobs. Although LFRs served well in on our test boat’s 120-square foot jib, boats with much larger headsails might do better with bearing blocks for this purpose.
LOW FRICTION RINGS LESSONS
Our experience with low friction rings has prompted several new insights.
VALUE GUIDE: Low Friction Rings
Durability. We’ve installed blocks from Harken, Nautos, Ronstan, and Wichard, and most of these blocks are still with us. Heavy-duty applications on bigger boats might wear out these blocks, and corrosion can bring on the early demise of certain designs (see PS December 2009, “Gear Graveyard”). In contrast, the anodized low friction rings can provide decades or more of service without breaking a sweat. The most likely failure, salt-induced corrosion of the anodized coating, is easily detected before it becomes a problem and can be prevented with rinses and wipe-downs.
While the low-friction ring can outlast the boat owner, the Dyneema slings and lashings that secure them are vulnerable to UV damage and chafe. We replace the line portion at about the 8-year mark — which is on the conservative side of what manufacturers advise. Life expectancy of Dyneema depends on your latitude, type of use, and the safety factor that is acceptable to you for the application. For a comparison of the various rings, see PS March 2018, “The Slick Simplicity of Low Friction Rings”).
Tackles. As with any new fad, low friction rings entice sailors to use them for everything. They’re strong, durable, compact, and much cheaper than anything with the same working load. The downside? The friction is greater, which limits their use with polyester lines and in multi-part tackles.
Efficiency, as measured by the weight lifted divided by the force applied to the other leg after a 180 degree bend, ranges from 80-83 percent for a small 12-plait Dyneema line to only 50-60 percent for a fat polyester double braid. For comparison, ball bearing blocks are about 95-97 percent efficient. As a result of this friction, an 8:1 power ratio is the practical limit for Dyneema line, and a 4:1 power ratio is the practical limit for polyester.
If you need very high purchase, for a vang, cunningham, or backstay adjuster, one solution is to use a low friction ring cascade to build the first 4:1 purchase, taking advantage of LFR’s ability to carry high loads safely, with minimal weight, cost and bulk. Then, add a lightweight 4:1 ball bearing block and tackle to pull the tail. The ball bearing blocks are more efficient and can operate over a much shorter distance than a high purchase cascade.
Tackle efficiency also suffers when a line is passed multiple times through a pair of low friction blocks—a common way of tensioning a line or stay. In these lashings, which we’ve seen used to tension stays on some very pricey boats, each pass of the line squeezes and rubs against the previous ones. We studied this in “Lashing for Strength,” PS June 2014.
Dyneema webbing can be handy when faced with not-so-low friction rings, like pressed eyes in sails. The webbing’s smaller effective diameter reduces bending-related friction and the webbing suffers no appreciable reduction in strength.
TITANIUM LOW FRICTION RINGS
Sky International and other brands have begun offering titanium rings. In our view, a titanium ring is overkill for common applications on cruising boats. Aluminum rings are already as strong as the line and have lower friction. Titanium’s chief advantage is its compatibility carbon fiber, which is why they are frequently embedded in carbon fiber rigging terminals. Wichard is now making LFRs with a brass finish, if the black racer look disturbs your classic-boat vibe.
TEXTILE BLOCKS
If the rope is deflected through an angle that is tighter than 90 degrees, or if the rope has a polyester cover, friction remains the Achilles heel of low friction rings.
LFR textile blocks reduce friction by re-orienting the ring. Instead of leading the rope through the “donut hole” in the low friction ring, the rope is led around a groove in the outside. To keep the line in the groove, a spacer block is secured by a length of Dyneema which also serves as the “axle” for the LFR (see photo 6 on page 8).
The moving line runs in the outside groove, like a conventional pulley. The setup retains LFR’s massive working load and safety factor, with friction similar to a conventional pinand- bushing block (though still more friction than a ball-bearing block). The cost of this innovation is a little added complexity, but not much extra cost if you make the modifications yourself. Prices go up sharply, however, if you buy factory-built LFR textile blocks.
Wear on the LFR can be a problem for actively trimmed lines, such as sheets, but rings can make sense for halyard foot blocks, for example, where adjustment is infrequent, but loads are high. Ino, Ropeye, and Antal have introduced some innovative designs that would suit this purpose, but we haven’t seen enough in use to evaluate durability. There’s no question whether the rings—some of which are rated to handle several tons—can handle the load.
The Antal SectoRing (see photo 5 on page 8) takes a simpler approach. While other designs use a spacer block to guide the Dyneema axle/becket, the Antal’s lower-profile plastic “sector” serves only to prevent the rope from jumping out of the LFR groove. It is worth noting that in our last round of testing Antal’s rings were found to have the lowest friction.
The bottom line is that successful applications of LFRs have several things in common. The line is Dyneema. The line is at least four times smaller than the hole in the center. The line turns less than 90 degrees. If a purchase is required, it is made using a cascade rather than a conventional tackle, because it is simpler to rig, lighter, and has less friction loss. LFR textile blocks, on the other hand, are more like ball bearing blocks.
LOW FRICTION RING APPLICATIONS
Every time we look at a race boat our heads swim with the applications.
Barber haulers. Like so many sailors, we switched to low friction rings in our barber hauler to eliminate bulky ball bearing blocks hanging on the sheets. Though not ideal, LFRs work with polyester sheets because the line is turning through a small angle.
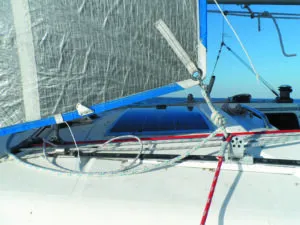
Rings make sense for replacing many of the smaller control blocks you find on cruising boats. An LFR could be used in outhauls, downhauls, and spinnaker twings.
Bobstays and backstays. Designed for high load capacity where failure has serious consequences, a properly sized LFR block-and-tackle can be used in either of these applications. Friction is not critical because adjustment is infrequent and the range of motion small.
Fairleads. Under a light load and with a minor change in direction, the friction is trivial, and certainly lower than other fairlead options. We’ve lashed LFRs to stanchions for furler line leads, and attached them with short slings where a “floating” lead (one that is not fixed directly to the deck) made more sense. We’ve even used them to redirect Dyneema cover bungee cord (yes, they exist).
Antal, Ronstan, and Harken now make aluminum low friction deck fairleads. They’ll far outlast plastic fairleads, but they can’t replace ball bearing deck organizers for leading halyards to the cockpit; there’s just too much friction. Too bad, because high loads can literally crush a deck organizer.
A conventional aluminum fairlead is not the same thing as a low friction ring. For example, Sea-dog aluminum fairleads have much shorter turning radius than most LFRs. Likewise, the stainless steel liners inside conventional plastic fairleads improve wear, but the friction is slightly greater than a LFR and they don’t have high working loads.
Makeshift repairs. Blocks break. A LFR with a strop attached can substitute in many cases. That, along with a few soft shackles can solve a good many contingency problems for a few ounces. (“Are You Ready to Klud Your Way Home,” February 2020)
Lashing Eyes. Sail maker’s thimbles are more economical in the smaller sizes, while still maintaining strength. In rigging applications, Colligo Marine’s low friction rings have advantages in inspectability and efficiency. But a standard LFR is particularly good at staying in the eye and not damaging the rope. Look for a deep groove, such as the Nautos or Antal rings. Wichard rings are a bit shallow.
Lazy Jacks. A perfect application. A sailmaker’s thimble will also serve this purpose on smaller boats.
Main outhaul. We have crushed ball bearing blocks in the high load, small space application. Plain bushing blocks could work, but LFRs paired with Dyneema are stronger and more durable. It’s not all about weight.
2:1 halyards. The critical limitation is usually hoisting space between the masthead and head grommet. LFRs have high load capacity, compact size, and work particularly well with Dyneema halyards. The most compact solution is to lash a ring to the head grommet with a lashing pinched with a tight seizing, securing the ring in the proper athwart ship orientation. Of course, it needs to be cut off when the sail is removed.
Vangs. You’ll see them on racing dinghies and sport boats were ounces count, but not so much on larger boats. The efficiency at high purchase numbers is not impressive, and a vang should be readily adjustable.
Sheet turning blocks. Simple LFRs can work on dinghies with Dyneema sheets, but an LFR textile block is the better bet for a cruisers or day sailors, and a ball bearing block is the best choice; Our DIY textile block was only an experiment.
Foot blocks at the mast. If you’ve got all-Dyneema halyards, why not? If they have polyester tails, our DIY low friction ring textile block is a possibility, but the splice must pass through the ring, an added strain.
Leading all of the halyards to the cockpit is a convenience, and in many cases a safety improvement, but this involves several 90 degrees turns, so we must minimize friction every chance we get. (We like halyards at the mast too; it’s easier to hoist a heady sail by simply hanging your weight on a halyard than grinding a winch that has been through several turning blocks.)
CONCLUSION
Get in the habit of asking yourself “Why not a low friction ring?” rather than “Why?” We like the durability, high working load, and compact size for many applications. But accept “no” as the answer when friction or wear are important factors, which they most often are. For now at least, ball bearing blocks are here to stay.
If you don’t have the time or inclination to make our DIY low friction ring textile block (see page 10), you’ll find a wide range of low-friction rings to suit specific purposes—from rigging, to becket blocks, to fairleads.
1. The Antal low friction mast outlet can serve many uses. It would be nice to have a screw-together twopiece version that could be used with thin decks or spars.
2. The Harken floating jib lead offers a clever way to rig a 3-way adjustable jib lead.
3. The INO textile block is paired with covered HMWPE line.
4. The spacer and Dyneema “axle” makes this H-block very slippery.
5. Antal SectoRing. The plastic insert at the lashing point keeps the line from jumping out of the LFR.
6. We are using a DIY textile block as a reacher turning block. Friction isn’t a problem with polyester line.
We wanted a lighter turning block for a pair of high friction reacher sheets, but we couldn’t bear the cost of the latest high tech offerings, so we built our own. These are only prototypes at this point, but we’ve tested them hauling logs and on the boat, with no obvious shortcoming so far.
The Mark I version, intended only to confirm dimensions, used a piece of masonite for the spreader plate, knots in place of splices, and a cable tie in place of a seizing. And it worked just fine, hauling logs in the back yard with an estimated load up to 500 pounds. The holes should match the size of the Dyneema rope. The seizing must keep the spreader plate close to the LFR to keep the Dyneema axle at the correct angle and to prevent the rope from jumping out. The dimensions are given below.
Our Mark II version used 1/8-inch aluminum plate for the spacer. It’s tough and functional, but we have some lingering concerns about chafe. Ideally, the plate thickness will be the 100-150 percent of the diameter of the sling line and the holes will be chamfered. Aluminum or composite are suitable materials.
A single Dyneema “axle” could be strong enough, but two axles are more stable. Some designs use a single axle, allowing the use of a long soft shackle in place of the loop.
To form the loop, you need to know how to make an end-toend splice with 12-strand Dyneema—not rocket science, but hard to describe. This will make more sense if you also watch this video (http://atlanticbraids.com/longer-end-to-end-splice/).
1. Thread the Dyneema through the end plate, and form loops of the desired length (3 x LFR diameter minimum, so that it can be looped around the anchor point).
2. Mark the two ends to be spliced where they will join, allowing extra length (about 4 extra rope diameters), because the loop will be shortened when the tails are buried.
3. Fold the ends over, cutting them off where they meet the spreader plate.
4. Insert a fid at into the core at one mark, and poke it back out through the strands near the spreader plate
5. Tape the cut end to the fid, and pull the tail through. Place a pin through point where the lines the cross so that the lines do not slip.
6. Repeat this process with the other tail, going in the opposite direction.
7. Remove the pin and pull the two tails until the crossover sets against itself.
8. Re-insert the pin and milk the cover over both ends, tapering before pulling them inside.
9. Place lock stitching over about 2 inches of the splice, on both sides of the joint marks. The bury is only about 20- 30 rope diameters, but with lock stitching and friction in the loop around the anchor point, this is just enough for full strength in this application.
10. Seize the throat under the spacer, close enough that the rope cannot slip between the spacer and the edges of the LFR. This is best done with a string of at least 8 half hitches, burying the tail with several pass through stitches when finished. Number 8 whipping twine is appropriate for ¼-inch Dyneema (see photos 1 & 3).
Our next version will use a slippery composite for the spacer and brand name Dyneema, instead of the cheap tow cable we used for our test version. We will cover the axle portion with an NER Spectra Chafe Sleeve to protect the loops. New England Ropes WR2 would also be good for this application.
The Mark II has a working load of 3000 pounds. The total cost is about $30 in parts plus 15 minutes in labor.
Allen Brothers in the UK make Low Friction Rings and 2 part threaded low friction rings (which they call deck bushes). The 2 part LFRs are designed to be installed in bulkheads or the deck where lines are to be ‘hidden’. Allen Brothers have a focus on performance dinghies and multihulls.
Take care, stay safe
Jonathan