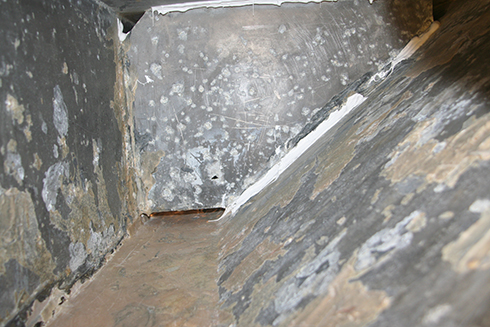
Patrick Childress
October is the time of year when the procrastinating catches up to us. The big projects we avoided all summer stare us in the face. Do nothing, and you risk a summer wasted pulling epoxy from your hair instead of sailing. If your boat is 20 years old or older, a fuel tank replacement—a bear of a project, even in ideal circumstances-might be that project you’re postponing. If it is, well, you’re in luck, because we’ve got a fair bit of information to help guide you through the process.
Several years ago, marine consultant and technical writer Steve D’Antonio did an extensive article for us on this topic, Diesel Fuel Tank Replacement. The following excerpt from that article deals explicitly with aluminum, but there are other options.
Aluminum is PSs replacement fuel tank material choice for most installations. It is easy to work with, readily available, comparatively inexpensive, light, strong, and corrosion resistant, although far from corrosion-proof. There are some prerequisites when selecting aluminum for fuel tank fabrication, and some important installation details that must be followed.
The alloy used must be 5052, 5083, or 5086 series and a minimum of .09 inches thick. This gauge is ABYC approved, however, 1/8-inch (.125 inches) is preferable, and 1/4-inch (.25 inches) should be considered for extreme applications, such as bilge installations or where maximum durability and longevity is sought. Every fraction of an inch of wall thickness will buy more years of life, particularly if the installation is less than perfect.
If aluminum possesses so many good attributes, why use anything else? Unfortunately, as many boat owners will attest, aluminum is anything but indestructible. One of its primary foibles is its susceptibility to some corrosion, particularly pitting, galvanic, and poultice. Pitting is caused by upsetting the corrosion-resistant film formed on the surface of aluminum, sometimes due to variations in available oxygen. Once it takes a foothold, the pit grows deeper, which creates a more powerful cell, accelerating the next form of corrosion, which is galvanic.
Galvanic corrosion is the interaction between dissimilar metals in the presence of an electrolyte. In aluminum tanks, this process may take place between a copper-alloy fitting (brass or bronze) and seawater, or between a pitted aluminum surface and seawater. You must ensure that all metals that are in contact with the tank are compatible with aluminum.
To prolong the tank’s life and minimize the chance of any potential harm, bonding the tank is also a good idea. Bonding the tank is an American Boat and Yacht Council requirement for several reasons: to prevent electrocution for shore-power-equipped vessels, to mitigate lightning damage, and to prevent side-flashes (electrical current jumping between metal components during a lightning strike). According to the ABYC, the boats bonding system, the DC negative system (which includes the engine block and battery negative), and the AC safety ground all should be connected and remain at the same potential.
The resistance between any two components in this system should not exceed 1 Ohm. (Its important to note that any bonding wire attached to the engine block must be sized to safely carry full engine cranking amperage.)
Bonding the tank minimizes the likelihood of damage caused by stray current corrosion, and it prevents static electricity build-up on or in the tank, which could lead to a spark and explosion (admittedly unlikely on diesel installations). If the tank is bonded, and the bonding system is properly attached to an underwater hull zinc anode, then this anode may provide some corrosion protection to the tank.
Poultice corrosion results when aluminum remains in constant contact with a wet surface, such as wood, carpeting, insulation, or stagnant water. If allowed to make contact, these demons are the harbingers of an early death for any aluminum tank. The result is prodigious amounts of white, gooey aluminum hydroxide. (It looks like freezer-burned vanilla ice cream.) This will quickly compromise the tank surface.
The best defense against this scenario is careful attention to installation details. No hygroscopic material should be allowed to make continuous contact with an aluminum tank, period.
A proper aluminum tank installation calls for 1/4-inch by 2-inch strips of non-hydroscopic material, such as neoprene or high-density plastic (Starboard for instance), spaced two inches apart and placed between the tank bottom and the shelf on which it is mounted. This will prevent the tank from resting in water, and enables air to circulate beneath the tank, while allowing condensation to evaporate. Additionally, the installer must be sure to bed or glue the insulating material to the bottom of the tank. If this is not done, water or condensation will find its way between it and the tank, and corrosion will set in. Any other mounting arrangements, such as cribs or beams, must include this insulating material.
For a more detailed discussion of fuel tank replacement see D’Antonio’s full report “Diesel Tank Replacement.” For more on bonding, lightning protection systems, and grounding, see Volume Two of our new five-volume ebook on Electrical Systems. Ed Sherman, past contributor to Practical Sailor and education director for ABYC, also covers bonding and testing for stray current leaks in detail in his excellent book Advanced Marine Electrics and Electronics troubleshooting. For more on protecting your existing system, PS Tech Editor contributor Drew Frye examined corrosion-fighting fuel additives.
If you suspect corrosion is eating away at your tank, and have addressed the cause, the late Patrick Childress, renowned circumnavigator and sailing writer who tragically died of COVID during the first wave, found a way to fix an aluminum water tank without replacing it. This might be something that can be done with a fuel tank. Unless you address the cause of the corrosion, any tank repairs would just be a time-consuming band-aid.
What are the first 2 pictures ? They look like an aluminum water tank interior ??
Aluminium tanks are quite suitable as fuel tanks indeed, but less for fresh water where chlorine and other purification salts, notably Ag salts containing silver, can seriously corrode the tanks.
The article suggests to me that aluminium is a poor choice as it needs so much care and protection. I want a tank material that I don’t want to think about, and aluminium doesn’t fit the bill.
I have large, GRP tanks, 50 years old, still going strong, not a care in the world. I have cleaned them out, as sludge had built up.
The weakness of aluminium tanks is corrosion of the bottom plate of the tank by water in the diesel collecting at the bottom. A simple temporary solution for a year or two is a few coats of P40 fibre putty (used as a filler on cars) on the outside of the bottom plate & a few inches up each side. The only permanent solution is if you can put P40 putty on the inside of the tank as well, but in most case access is impossible, so most people simply cut off the bottom of the tank & weld on a new Al plate. If I had to choose again I would use plastic tanks, no corrosion & easier to clean.