Historically, fiberglass boat hulls and decks were molded separately, and then bonded at the deck seam. Bulkheads were added either with polyester or epoxy putty, and then taped into place with fiberglass tape. The putty should hold, if well done, but it could crack if twisted hard or subject to impact, and the extra taping added a lot of toughness.
More and more often, we see stringers, bulkheads, liners, and keel grids bonded into place with Plexus—no taping. The “miracle glue” is a leading brand of methyl methacrylate (MMA) adhesive from the global manufacturing company Illinois Tool Works (ITW), maker of several other familiar brands, like the anti-sieze coating Permatex. Most of the time, MMA does an outstanding job bonding marine structures. Occasionally, it fails spectacularly, and in most cases, the fault is due to poor installation or design errors. In this report, we wanted to take a closer look at the adhesive’s strengths and its shortcomings.
PHYSICAL PROPERTIES
Hardness, tensile elongation, and tensile modulus all tell us something about the stiffness of an adhesive. The higher the number in these areas, the stiffer the material. Methacrylates and G-Flex are roughly similar. The stiffest polyurethane, 3M 5200, is hundreds of times less stiff than MMA, and West Systems epoxy is about three times more stiff. The 3M adhesive 5200 has about 5-20 times less bond strength, which is in rough proportion to its lesser stiffness.
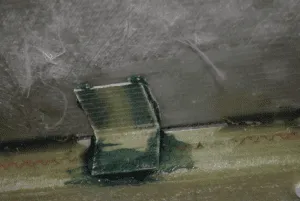
Bond strength. Although MMA’s bond strength is slightly weaker than that of epoxy on paper, in the real world of imperfect surface preparation the two are neck and neck. The cure time is much less, speeding work. Five-minute epoxies are fast, but as adhesives, they are not as strong.
With epoxy or polyester the entire bond area (about 6-8 inches wide for a taped joint) must be solvent cleaned sanded, and cleaned again. The bulkhead must be puttied (bonding filets) into place, the filets smoothed enough for glassing, and allowed to cure overnight. The area is then sanded again to smooth the fillet, cleaned again, and several layers of fiberglass brushed and rolled into place.
With Plexus, the builder marks the bond area, lays a bead of adhesive, and plops the bulkhead into the bead. Twenty minutes later it will have cured enough to remove any braces and keep working. Cleaning, sanding, and taping are eliminated. In fact, Plexus can be used to bond structures such as grids and liners where the bond area is not accessible for taping.
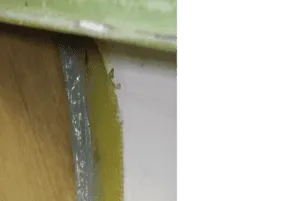
Toughness. Methyl methacrylate adhesives are tougher than other glues. Unlike epoxy and polyester resins, which are rigid and simply snap after curing unless reinforced, Plexus is more like G-Flex, a toughened epoxy that is harder than sealant but more flexible than epoxy. You don’t really want to use it where finish-sanding is required, and its elasticity (10 times greater than traditional epoxies) is sub-optimum for laminating glass or FRP structures that require rigidity or stiffness.
However, its bond is tenacious and minor flexing is less likely to loosen its grip. Is it as tough and strong as a filleted and taped seam? Not unless the joint includes a flange (see “Joint Design”), but the MMA will pull chunks out of the bulkhead before failing.
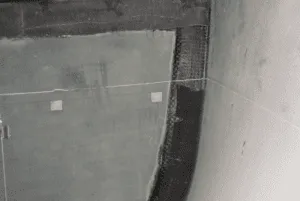
Surface Preparation. Strong solvents in methacrylate adhesives dissolve trace surface contamination, and the adhesive\penetrates the surface, reducing the sanding required to create a bonding profile. Gross contamination can inhibit bonding, so cleaning and sanding are still recommended.
In a production setting you should be able to control contamination, but mistakes happen. Case in point is the beam joint on a trimaran that opened up after 26 years. Unnoticed, this sort of failure gradually expands until the beam fails catastrophically. The designer felt it was a surface preparation issue, since the failures were spotty and only involved certain production periods.
In general, sanding still improves bond strength by 15-35 percent, depending on the substrate. Our advice is to prep as you would for epoxy.
Use Enough Adhesive. When bonding a grid or hull liner, how do you know if the adhesive has filled the gaps? How do you know the width of the gaps with certainty for a joint you cannot see? If you can see the joint, obviously you look for squeeze-out, but if it’s hidden, you are dependent on accurate molding, a good fit, and the proper amount of glue. There is no way to check later without cutting holes.
Speed. Bulkheads and grids are not the only applications. We like methacrylates for mounting studs, to which we will later mount equipment. Epoxies work, but methacrylates cure faster and are sticky enough to hold the stud in place for 15 minutes until a fixture set is achieved.
Weld-Mount, for example, uses a proprietary methacrylate adhesive. (See “Glue-On Fasteners,” PS July 2017). Five-minute epoxies cure quickly, but they are not as strong as conventional epoxies or MMAs and are further weakened by thickening agents. They have a vicious exotherm if used in more than tiny amounts; if you fill a bolt hole in warm weather it will boil right out, and thickened 5-minute epoxy layers must be kept thin. The only thing we recommend 5-minute epoxy for is tacking epoxy projects in place before proceeding with thickened epoxy filets and glass reinforcement.
Bonding Surfaces. Epoxies rely on both mechanical keying (sanded surface) and high surface energy (surfaces that don’t bead water well) to bond. Methacrylate adhesives, on the other hand, dissolve surface layers of many materials by strong solvency and can bond to lower surface-energy materials, including some plastics and most metals—but not copper and copper alloys, because copper inhibits MMA curing. Additionally, the increased flexibility of MMA reduces bond stress if the substrate flexes.
Odor. Epoxy has only a slightly musty odor and is relatively safe to work with, although a very few people will develop a sensitivity over time and can be put into shock. Polyester resins release a pungent styrene odor that can persist for weeks. Although polyester resin is not highly toxic (supplied air or vapor respirators and good ventilation are required), there have been numerous fatalities in confined spaces.
Methacrylate adhesives have a pungent odor coming from the solvent, monomer, and initiator. If you need a few milliliters to bond a broken part, no vapor emissions are no big deal, but if you are going to use more than 200 ml or work in a confined space, we suggest ample ventilation or a respirator fitted with an organic vapor cartridge (see OSHA exposure limits in SDS). Polyurethanes cure very slowly, contain few volatiles, and there is very little odor that you will notice.
No amine blush. Unlike many epoxies, and specifically West Systems products including G-Flex, there is no sticky blush to be scrubbed off before painting or additional bonding. Just sand and go.
Flexibility. The tensile modulus (the engineering measure of flexibility) is the same for MA-300 (135K-165 kpsi) and G-Flex (145 kpsi). We also glued small fiberglass panels together for long-term testing and observed flexibility. They flexed the same. Conventional epoxies are about three times stiffer, and thus more efficient for wetting and laminating fibers.
Cure Time. Methacrylates cure relatively fast. Everything they need to bond is in the tube, so like epoxies, they cure full depth. They can also exotherm like a fast cure epoxy, though this is typically not a problem when used as an adhesive in thin joints. Expect a “fixture” cure (means you can take the lamps and braces off) in 15-30 minutes and a full cure within hours. Epoxies are next, with a fixture cure within 2-4 hours and full cure overnight. Then there are polyurethanes, including 3M 5200, which require moisture to cure. In warm weather and high humidity, you can expect a fixture cure overnight and full strength in a few days to a week. However, if the air is dry (winter, even indoors), the joint deep, or the material is non-porous, the cure can take much longer, as much as months. Curing can be hastened by increasing humidity and temperature.
With all adhesives, decreased temperature slows the cure. Manufacturers often state a minimum temperature of 40F, but that is the minimum during the cure period, not the daily high, and the cure period will be days for all of these product in cool temperatures. We prefer not to work with adhesives until the daily highs are in the 60s and the lows well above freezing. Dew is also a problem.
Dispensing Guns. The smaller tubes (25 ml Devcon or 50 ml Plexus) are easily dispensed manually. The mixing tubes waste expensive product and sometimes the pistons stick a little, resulting in disproportional dispensing. For small projects, skip the gun and just mix with a putty knife. If you are going heavy duty with the 500 ml tubes, Plexus recommends the Cox M400XMR gun for about $92, a good value for a pro quality gun. Other guns will work, so if you have a 2-part gun, tests the fit before buying the Cox. You will need the mixing tubes, of course.
Shelf Life. Unlike epoxies, open methacrylates don’t last. Always test a small bit before anything critical; you’ll know if it is kicking properly within 30 minutes. Moisture and heat reduce shelf life, so keep open tubes in a sealed container in your “glue fridge” (where we keep our polyurethane sealants) and you may get a shelf life of one year. At room temperature, anything over 3 months is a crap shoot. Do not keep opened tubes in your car or on the boat, and don’t buy ahead of need. Do not use on copper, brass, or bronze.
CONCLUSION
MMAs most closely compare with toughened epoxies, which are really in a different category from standard resins. The difference is that MMAs bond better with plastics.
The specifications from lab tests don’t fully express the differences between the two glues, because they don’t take into account epoxies ability to bend with the substrate rather than pop off. You can thicken a toughened epoxy using the same materials you use with laminating epoxies. G-Flex takes overnight to fully harden. Dr. Sail’s products are faster and weaker.
Since we’re not building boats, what can a do-it-yourselfer use this super adhesive for? It is great for mounting threaded studs, seaming pre-cast fiberglass sheets, and repairing loose bulkheads that are too difficult to access with tape and epoxy. It will help seal leaky hull-to-deck seams that have opened up, repair worn blocks, or fix cracked plastic fittings.
Even if you are staying with epoxies for large bonding jobs, methacrylates have a place for small repairs and mounting projects. If something plastic breaks, try Devcon Plastic Welder as an introduction to Plexus and methacrylate adhesives.
VALUE GUIDE: COMPARING MMA ADHESIVES, EPOXIES, AND 3M 5200
Among the gifts from the people of the Pacific is the feast of words dealing with boats and the sea. The three principal structures in any multihull are more often referred to their Polynesian names vaka (hull), ama (float), and aka (cross-beam). In the case of our F-24 Corsair test boat, it was the aka giving us trouble.
1.A poor bonding job and constant flexing of the aka on the F-24 opened up a seam in the two molded shapes used to form the cross-beam.
2. After removing the trampoline lacing, we carefully opened the seam using a screwdriver and hacksaw blade.
3. With the seam opened up, we applied Devcon MA300 Plastic Welder, a methacrylate adhesive that is sold in small quantities online and at hardware stores. This “after” photo shows the seam repaired. New through-bolts reinforce the joint.
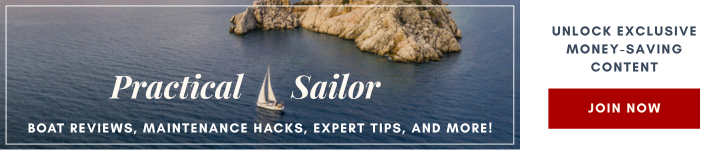
Devcon and Plexus are both ITW brands, so it stands to reason they share technology. Sure enough, Devcon Plastic Welder is actually re-branded Plexus MA300, which is very similar to Plexus MA310, used by boat builders for many tasks. The bonding and strength characteristics are very similar, but the pot life and fixture time is shorter, ideal for smaller jobs and mounting studs. We’ve used it with good success on jobs too small to justify a big tube of Plexus and the 2-part gun needed to dispense.
• For very small projects some suggest separating the two tubes and using them separately; it is actually easier to meter small amounts this way. The piston tends to hang up, pushing one side more than the other. However, if you are using more than ½ teaspoon it is simpler to keep them connected.
• When repairing something broken, consider reinforcing the break with fiberglass or other material of similar flex to the underlying material. For example, can lay in a few snippets of fiberglass? There is no point in using carbon with MMA; the resin is too flexible for such a stiff fiber.
• Mix small amounts and mix fast. Like 5-minute epoxies, you only have a few minutes to mix, spread, and clamp.
• If you will be using a respirator, get that first. You won’t have time once you start working. You probably won’t need it for small projects you might tackle with the Devcon Plastic Welder kit.
• Forget cleaning tools. Technically, acetone works, but you won’t have the time before it cures.
• Cover all surfaces. Unlike epoxies and polyurethanes, which can be wiped up with solvent, methacrylates tend to melt the surface, even of gelcoat, leaving a scar. Mask the edges of the application area.
Most 2-part plastic glues in hardware store bubble packs are actually toughened epoxies. Loctite Plastic Bonder, JB Weld Plastic Bonder, and JB Weld Plastic Welder are all epoxies. To our knowledge, Devcon Plastic Welder is the only MMA that is sold at retail stores in this size.
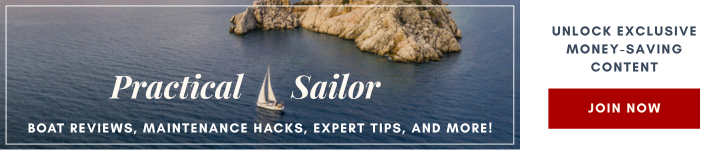
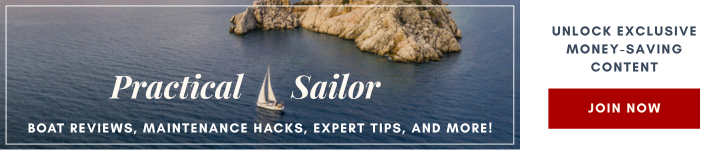