Making spare winch handles is a simple job for a competent metal worker. This I discovered because our Norlin designed Scampi, Windhover, has eight winches, all of which were manufactured before the world standardized on the 11/6″ winch handle lug size. Since Windhover’s 9/16″ size handles are difficult to obtain and impossible to find at discount I went to Frank “Red’ Grobelch, a superb metalsmith/welder of Waukegan, Illinois with some ideas for making up some spares for me. I’m so pleased with the results that I’d recommend the project to any reader who is a competent metal worker or has a friend who is. Even if you can use and buy standard 11/16” size handles, your mental state when clumsy Uncle Fred drops a handle overboard will be far more buoyant if you know you can easily replace the lost handle in your own shop.
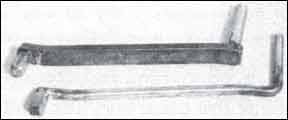
288
The photograph shows two examples of Red’s work. The handle at the top was the first effort; it’s made with a 1″ x1/2″ bar stock body, and is overkill on any boat under 40′.
The drawing shows the shape and dimensions used; they’re copied from a commercially manufactured handle. On this version, the body is a single piece of 1/2″ diameter stainless steel rod with a 1″ long piece of stainless key stock welded on for a lug.
Stainless steel was used because it is cheaper than bronze, because in good grades it is non-magnetic and hence won’t affect compasses, and because it’s rust proof.
Making the handle is accomplished by first bending the rod to shape, then welding on the lug.
The bending was accomplished by fastening the rod in a vise, heating it with a torch until cherry red, then bending by hand. The end upright was the first bend made, followed by the two jogs along the handle length. An even simpler job could leave out the jogs, but the result would not give the same working room over the winch body.
After the handle bodies are bent, the key stock lugs — of 11/16, 9/16, or whatever fits your winches — are cut to length with a hack saw, then welded on using a stainless steel welding rod.
Grind an angle at the bottom edges of the lugs, grind the welds, and grind off the sharp edges at the ends of the rod.
At this point, the handles are nearly finished, but the lugs require some shaping. If you look at a commercially made handle, you’ll see that the lugs are not perfectly square. As the drawing shows, in cross section the lugs have a very slight convex curve. Without this curve, the lugs will not fit easily (or at all) into the winch socket.
Part of the curve can be ground with an abrasive wheel using a commercially available handle lug as a rough guide, but the final fit is best accomplished with a file, using the file and fit method.
Finally, smooth and buff the handle; using a polishing wheel to remove any traces of filings.
Without a rotating grip, these handles will be less efficient than a readymade winch handle, and the small diameter of the rod will make the handle more difficult to hold while grinding the sheet or halyard.
-JP